PRODUCT PARAMETERS
Description
Introduction of Yogie Energy rotary Dryer Drum rotary kiln Shell For Cement Making Machinery Plant
A rotary kiln is a kind of industrial equipment used for material heating and processing, which is widely used in cement, metallurgy, chemical industry, etc. Yogie Energy rotary Dryer Drum rotary kiln Shell For Cement Making Machinery Plant refers to various parts and components which are necessary for maintaining and repairing the normal operation of the rotary kiln, such as cylinder, baffle wheel, pallet, sealing device and so on.
Features and advantages of Yogie Energy rotary Dryer Drum rotary kiln Shell For Cement Making Machinery Plant
High-temperature resistance: Due to the extremely high temperature of the working environment of the rotary kiln, the spare parts are usually made of refractory materials or special alloys to ensure that they can work stably under high temperatures.
High abrasion resistance: Long time material friction and chemical erosion require spare parts to have excellent abrasion resistance to prolong service life.
High structural strength: in order to withstand heavy loads and the pressure of continuous operation, the design of spare parts will place special emphasis on structural strength and reliability.
Easy to install and maintain: Considering the need for frequent replacement, many spare parts are designed to be simpler and easier for quick installation and maintenance.
Strong adaptability: different industries have different needs for rotary kilns, so spare parts need to have good versatility and adaptability to meet diverse application conditions.
(Yogie Energy rotary Dryer Drum rotary kiln Shell For Cement Making Machinery Plant )
Specifications of Yogie Energy rotary Dryer Drum rotary kiln Shell For Cement Making Machinery Plant
The Yogie Energy Rotary Dryer Drum and Rotary Kiln Shell are built for cement-making machinery plants. These parts handle high heat and heavy loads. The drum and shell are made from strong steel. This steel resists wear and corrosion. It ensures long-lasting use in tough conditions.
The rotary dryer drum dries raw materials like limestone and clay. It works before the kiln process. The drum has a large diameter. This allows even heat spread. The drum’s thickness ranges from 15mm to 50mm. The exact size depends on plant needs. The drum’s length can reach 30 meters. Its rotation speed stays between 2-5 RPM. This slow speed ensures materials dry fully.
The rotary kiln shell heats materials to over 1400°C. It turns raw mix into clinker. The shell uses special refractory lining. This lining protects against extreme temperatures. The shell’s diameter varies from 2.5 to 6 meters. Its length can extend to 95 meters. The shell’s steel plates are 20-80mm thick. These plates are welded for tight seals. This stops heat loss and boosts efficiency.
Both parts use advanced welding methods. Automated systems check weld quality. This prevents cracks or leaks. The drum and shell include support rollers and thrust rollers. These keep rotation smooth and stable. Gears and motors are sized to match the plant’s power.
Custom designs are available. Customers pick sizes, thickness, and materials. The drum and shell come with heat-resistant coatings. These coatings cut maintenance needs. Installation is simple. Pre-assembled sections save time.
Testing happens before delivery. Pressure checks and heat trials ensure safety. Each part meets global standards like ISO and CE. Yogie Energy offers after-sales support. This includes technical help and spare parts.
The rotary dryer drum and kiln shell work in all cement plants. They handle raw material prep and clinker production. Durable builds reduce downtime. Energy-efficient designs lower operating costs. These parts keep cement plants running smoothly for years.
(Yogie Energy rotary Dryer Drum rotary kiln Shell For Cement Making Machinery Plant )
Applications of Yogie Energy rotary Dryer Drum rotary kiln Shell For Cement Making Machinery Plant
Yogie Energy’s rotary dryer drum and rotary kiln shell are vital components in cement production machinery. These parts handle high-temperature processing and heavy-duty material handling. The rotary dryer drum efficiently dries raw materials like limestone, clay, and slag. Moisture removal is critical before grinding. The drum’s design ensures even heat distribution. This reduces energy waste and speeds up drying. Its robust construction resists wear from abrasive materials. This makes it reliable for continuous operation.
The rotary kiln shell is central to clinker production. It rotates steadily to heat raw materials to extreme temperatures. Chemical reactions inside form clinker, the base for cement. The shell’s thick steel walls endure prolonged thermal stress. Advanced welding techniques prevent cracks or deformities. Insulation layers inside retain heat. This cuts fuel consumption and operating costs.
Both components adapt to diverse industrial needs. They process waste materials like fly ash or sludge. This supports eco-friendly cement production. The dryer drum handles wet byproducts from other processes. It recycles heat from kiln exhaust gases. This boosts overall plant efficiency.
Yogie Energy’s products prioritize durability and performance. High-grade alloys resist corrosion and oxidation. Custom sizes fit existing machinery setups. Precision engineering minimizes vibration and misalignment. This extends equipment lifespan. Easy maintenance access reduces downtime. Automated controls monitor temperature and rotation speed. Operators adjust settings for optimal output.
Installation is straightforward with modular designs. Pre-assembled sections cut setup time. Technical support ensures smooth integration into cement plants. Regular maintenance guidelines prevent unexpected breakdowns. Spare parts are readily available for quick replacements.
These rotary dryer drums and kiln shells suit large-scale cement plants. They also work in smaller facilities upgrading their systems. Consistent performance meets strict industry standards. Yogie Energy focuses on delivering solutions that enhance productivity. Their equipment handles the toughest conditions without faltering. Technical teams provide round-the-clock assistance for troubleshooting.
Company Introduction
Established in 2001, plant Machinery Equipment Co.,ltd. focus on metal research and mining machinery spare parts. 2 factories over an area of 13,300 square meters, based on 100+ sets of equipment, our production capacity reaches 12000 Tons/Year. has passed ISO 9001 quality managment system certification in 2008.
Our mainly products are dragline excavator spare parts,rotary kiln spare parts, large modulus gear (gear shaft), gearbox ect. 40+ patents with over 45 years experience to help focus on improve the service life of spare parts. We belive that more than 80% reason of mechanical parts’ working life depends on hot processing (steel making/forging/casting/welding/heat treatment). Eight material engineers will control the quality from the original resource.
If you are interested, please feel free to contact us.
Payment
L/C, T/T, Western Union, Paypal, Credit Card etc.
Shipment
By sea, by air, by express, as customers request.
5 FAQs of Yogie Energy rotary Dryer Drum rotary kiln Shell For Cement Making Machinery Plant
What is the Yogie Energy rotary dryer drum rotary kiln shell made of? The shell uses high-quality heat-resistant alloy steel. This material handles extreme temperatures in cement production. It resists corrosion and wear. This ensures long-term durability in harsh environments. Regular checks are recommended to maintain performance.
How does the rotary kiln shell improve cement-making efficiency? The design ensures even heat distribution inside the drum. This speeds up material drying and processing. Consistent heat reduces energy waste. Better heat transfer lowers fuel costs. Proper installation keeps the system running smoothly.
Can the kiln shell be customized for different plant sizes? Yes. The shell is available in multiple diameters and lengths. Sizes match small to large cement plants. Modifications include thickness adjustments or added support rings. Custom specs require detailed plant data. This ensures the shell fits existing machinery.
What maintenance does the rotary dryer drum shell need? Inspect the shell surface for cracks or warping monthly. Clean debris from the interior after each batch. Lubricate rotating parts weekly. Replace damaged sections immediately. Follow the manual’s guidelines for specific schedules. Proper care prevents unexpected downtime.
How is the kiln shell installed in a cement plant? Installation needs professional technicians. The shell aligns with the existing rotary drum frame. Secure it using heavy-duty bolts. Check alignment and balance before starting the system. Testing runs confirm stability. Yogie Energy offers onsite support if needed.
(Yogie Energy rotary Dryer Drum rotary kiln Shell For Cement Making Machinery Plant )
REQUEST A QUOTE
RELATED PRODUCTS
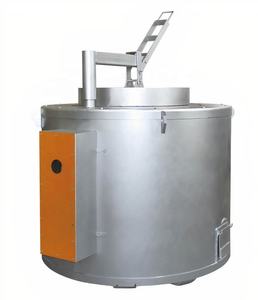
Four Channel Cement Rotary Kiln Industry Double Swirl Rotary Kiln Burner Double Swirl Rotary Kiln Burner For Cement Production
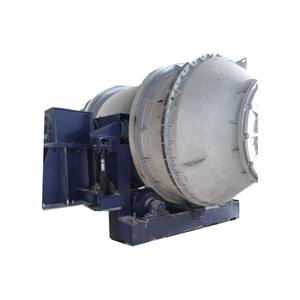
High temperature rotary tube furnace lithium battery powder sintering furnace rotary kiln non-standard customization
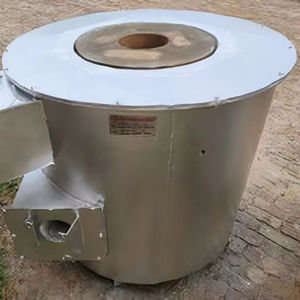
Ceramic Intalox Saddle Ring
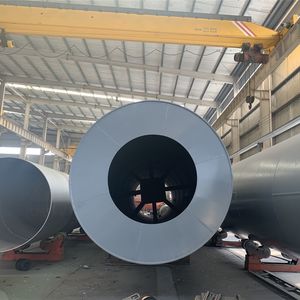
Rotary Kiln Spare Part Kiln Sealing/Big Gear Ring/Support Roller
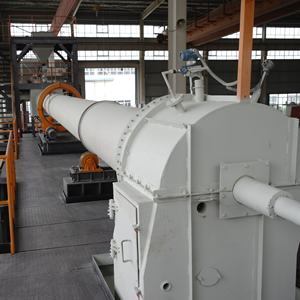
OEM Steel Rotary Kiln Support Roller Shaft
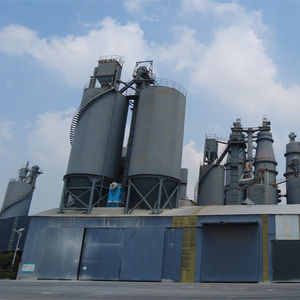