PRODUCT PARAMETERS
Description
Introduction of Top Quality large factory drum kiln rotary kiln
A rotary kiln is a kind of industrial equipment used for material heating and processing, which is widely used in cement, metallurgy, chemical industry, etc. Top Quality large factory drum kiln rotary kiln refers to various parts and components which are necessary for maintaining and repairing the normal operation of the rotary kiln, such as cylinder, baffle wheel, pallet, sealing device and so on.
Features and advantages of Top Quality large factory drum kiln rotary kiln
High-temperature resistance: Due to the extremely high temperature of the working environment of the rotary kiln, the spare parts are usually made of refractory materials or special alloys to ensure that they can work stably under high temperatures.
High abrasion resistance: Long time material friction and chemical erosion require spare parts to have excellent abrasion resistance to prolong service life.
High structural strength: in order to withstand heavy loads and the pressure of continuous operation, the design of spare parts will place special emphasis on structural strength and reliability.
Easy to install and maintain: Considering the need for frequent replacement, many spare parts are designed to be simpler and easier for quick installation and maintenance.
Strong adaptability: different industries have different needs for rotary kilns, so spare parts need to have good versatility and adaptability to meet diverse application conditions.
(Top Quality large factory drum kiln rotary kiln)
Specifications of Top Quality large factory drum kiln rotary kiln
High-grade huge manufacturing facility drum kiln rotary kilns are built for durable industrial use. These kilns handle high-temperature procedures like calcination, thermal processing, chain reactions. The layout focuses on resilience, efficiency, consistent performance. The drum is made from thick steel plates bonded with each other. Top-quality materials stop contorting under extreme warmth. The interior has a refractory lining. This lining resists temperatures over 1500 ° C. It secures the drum structure. It makes certain warmth keeps inside the processing zone.
Rotating kilns been available in sizes from 2 meters to 5 meters in diameter. Length arrays from 30 meters to 100 meters. Personalized dimensions match particular production demands. The kiln turns gradually. A gear-and-pinion drive system manages turning speed. Sturdy motors give consistent motion. Rotation speed readjusts in between 0.5 to 5 changes per min. Adjustable rate suits different products.
Heating unit use gas, oil, or solid gas. Advanced burners disperse warmth evenly. Temperature level control is accurate. Sensing units keep an eye on warmth zones. Operators readjust setups in real time. Warm recuperation systems record waste energy. They recycle it to preheat incoming air. This cuts gas expenses. It reduces environmental impact.
Material enters via a sealed feed system. It moves with the kiln as the drum turns. The incline of the kiln controls product flow. Adjustable tilt angles manage processing time. Discharge systems remove refined material effectively. Dirt seals prevent leakages. They maintain the work space tidy.
Safety functions include emergency quit systems. Overheat alarms safeguard equipment. Pressure sensors identify clogs. Automatic closure protects against damage. Upkeep access points are developed right into the layout. Workers check parts without dismantling the kiln.
These kilns work in cement production, mining, chemical manufacturing. They refine limestone, clay, ores, industrial waste. High thermal performance lowers running costs. Tough building lowers downtime. Minimal upkeep expands life span.
Discharge control systems satisfy strict laws. Filters catch particulates. Scrubbers get rid of harmful gases. Noise decrease tech keeps work environments safe. Conformity with global ecological requirements is basic.
Energy-efficient designs save power. Insulation layers maintain heat loss listed below 10%. Automated controls optimize fuel use. Performance data is tracked electronically. Operators monitor effectiveness from another location. Real-time informs advise of problems. Quick solutions stop hold-ups.
These kilns are built for 20+ years of solution. Regular upkeep ensures integrity. Spare components are easy to replace. Technical support is offered worldwide. Educating programs instruct secure procedure.
(Top Quality large factory drum kiln rotary kiln)
Applications of Top Quality large factory drum kiln rotary kiln
Large manufacturing facility drum kilns, called rotating kilns, offer important duties across numerous sectors. These sturdy makers handle high-temperature processes successfully. Their layout enables continuous operation under extreme warm, making them suitable for large manufacturing needs.
In cement manufacturing, rotary kilns transform basic materials like limestone and clay into clinker. The clinker gets ground into cement powder. The kiln’s revolving action guarantees also home heating, which is crucial for constant item top quality. High warmth inside the kiln sets off chemical reactions, changing raw mix into long lasting concrete.
Lime manufacturing relies on rotating kilns to process limestone right into quicklime. The kiln heats up sedimentary rock to over 900 ° C, breaking it down right into calcium oxide. This product is vital for steelmaking, water therapy, and building and construction. The kiln’s accurate temperature control stops under- or over-burning, taking full advantage of output purity.
Metallurgical procedures make use of rotary kilns to fine-tune steel ores. Iron ore pellets, as an example, go through solidifying in these kilns before smelting. The process removes wetness and boosts ore toughness. This step makes certain reliable heating system efficiency in steel plants. Non-ferrous metals like aluminum and copper likewise depend upon kilns for calcination and reduction.
Chemical sectors apply rotary kilns to produce materials like alumina and titanium dioxide. These substances develop the basis for paints, porcelains, and electronics. The kiln’s capability to maintain specific thermal profiles supports complicated chemical changes. Waste gas treatment systems in kilns decrease discharges, lining up with environmental regulations.
Ecological fields deploy rotary kilns for hazardous waste disposal. The kilns blaze toxic materials at heats, reducing the effects of hazardous components. This method manages commercial sludge, medical waste, and infected dirt safely. The procedure minimizes ecological effect while recovering power from waste.
Minerals like gypsum and kaolin undergo handling in rotating kilns to boost residential properties. Gypsum calcination creates plaster for construction. Kaolin treatment improves illumination for paper and porcelains. The kiln’s adjustable rotation speed and temperature level settings satisfy diverse product demands.
Resilience and reduced maintenance make rotating kilns cost-effective for heavy industries. Advanced insulation lowers warm loss, reducing power use. Adjustable sizes and setups fit various production scales. These attributes guarantee rotating kilns stay central to commercial procedures worldwide.
Company Introduction
Established in 2001, plant Machinery Equipment Co.,ltd. focus on metal research and mining machinery spare parts. 2 factories over an area of 13,300 square meters, based on 100+ sets of equipment, our production capacity reaches 12000 Tons/Year. has passed ISO 9001 quality managment system certification in 2008.
Our mainly products are dragline excavator spare parts,rotary kiln spare parts, large modulus gear (gear shaft), gearbox ect. 40+ patents with over 45 years experience to help focus on improve the service life of spare parts. We belive that more than 80% reason of mechanical parts’ working life depends on hot processing (steel making/forging/casting/welding/heat treatment). Eight material engineers will control the quality from the original resource.
If you are interested, please feel free to contact us.
Payment
L/C, T/T, Western Union, Paypal, Credit Card etc.
Shipment
By sea, by air, by express, as customers request.
5 FAQs of Top Quality large factory drum kiln rotary kiln
A drum kiln rotary kiln is a large industrial oven used for processing materials at high temperatures. It rotates slowly to heat materials evenly. Common industries using these kilns include cement production, lime manufacturing, and iron ore processing. The rotation ensures consistent heat distribution, improving product quality and process efficiency.
Regular maintenance is critical for keeping a drum kiln rotary kiln running smoothly. Key parts like rollers, gears, and seals need frequent checks. Inspections prevent unexpected breakdowns and extend equipment life. Cleaning the interior removes buildup that could affect performance. Lubricating moving parts reduces friction and wear. Maintenance schedules should match the kiln’s usage intensity.
Temperature control in a drum kiln rotary kiln relies on advanced sensors and automated systems. These tools monitor heat levels in real time. Operators adjust settings based on material requirements. Consistent temperatures ensure uniform processing and prevent defects. Overheating damages the kiln lining, while low temperatures slow production. Modern kilns use software to optimize heating cycles automatically.
Drum kiln rotary kilns can be customized to fit specific industrial needs. Sizes vary based on production capacity. Linings use different refractory materials depending on processed substances. Heating methods include gas, coal, or electric systems. Custom designs might include extra insulation or specialized cooling zones. Manufacturers work with clients to modify kilns for unique workflows or material types.
Safety features in drum kiln rotary kilns prevent accidents and protect workers. Emergency stop buttons halt operations immediately. Pressure release valves avoid dangerous buildup inside the chamber. Thermal sensors trigger alarms if temperatures exceed safe limits. Protective gear like heat-resistant suits and helmets is mandatory for operators. Regular safety drills ensure staff know how to handle emergencies. Proper ventilation systems reduce exposure to harmful fumes.
(Top Quality large factory drum kiln rotary kiln)
REQUEST A QUOTE
RELATED PRODUCTS
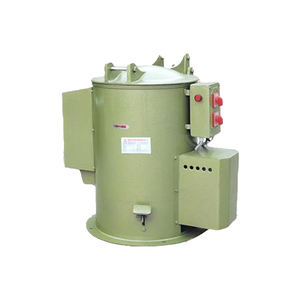
Refractory Cordierite Ceramic Heating parts Factory Direct
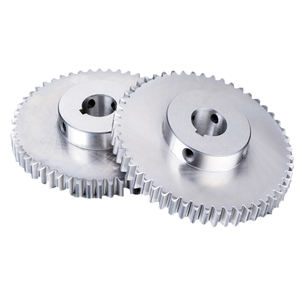
High Quality Custom Sand Iron Casting Services Foundry Roller part Cast Iron Spare Parts Grey Iron Casting Cnc Machining GG20
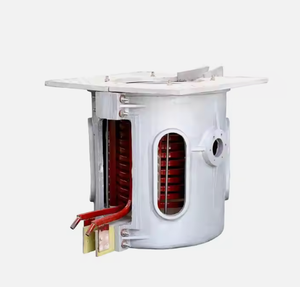
High Quality Large Cement Plant Rotary Kiln Parts Large Diameter Gear Ring
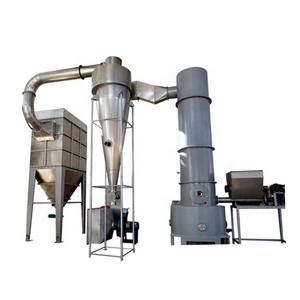
Wide Adaptability High Strength Double Swirl Rotary Kiln Burner Low Cost Double Swirl Rotary Kiln Burner
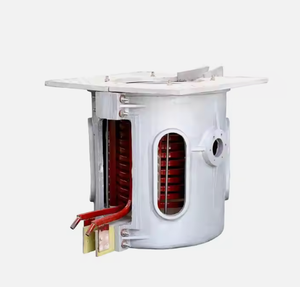
Rotary Industry KIln For Powder Sintering and Pellet Sintering
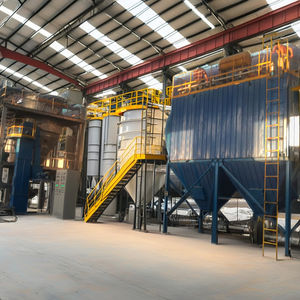