PRODUCT PARAMETERS
Description
Introduction of rotary kiln tyre & roller / rotary kiln spare parts
A rotary kiln is a kind of industrial equipment used for material heating and processing, which is widely used in cement, metallurgy, chemical industry, etc. rotary kiln tyre & roller / rotary kiln spare parts refers to various parts and components which are necessary for maintaining and repairing the normal operation of the rotary kiln, such as cylinder, baffle wheel, pallet, sealing device and so on.
Features and advantages of rotary kiln tyre & roller / rotary kiln spare parts
High-temperature resistance: Due to the extremely high temperature of the working environment of the rotary kiln, the spare parts are usually made of refractory materials or special alloys to ensure that they can work stably under high temperatures.
High abrasion resistance: Long time material friction and chemical erosion require spare parts to have excellent abrasion resistance to prolong service life.
High structural strength: in order to withstand heavy loads and the pressure of continuous operation, the design of spare parts will place special emphasis on structural strength and reliability.
Easy to install and maintain: Considering the need for frequent replacement, many spare parts are designed to be simpler and easier for quick installation and maintenance.
Strong adaptability: different industries have different needs for rotary kilns, so spare parts need to have good versatility and adaptability to meet diverse application conditions.
(rotary kiln tyre & roller / rotary kiln spare parts )
Specifications of rotary kiln tyre & roller / rotary kiln spare parts
Rotary Kilns are powerful equipment used for the dry firing of baked goods, chemicals, and other materials. They consist of a kiln body, kiln control system, fuel system, air delivery system, and auxiliary equipment such as rotary dryer, wheel, and mill. These components work together to ensure efficient burning and optimal temperature distribution.
One of the most important specifications in a rotary kiln is the size and shape of the kiln body. This can affect the amount of energy required for baking, as well as the efficiency of the kiln’s operation. The kiln body should be designed to provide sufficient space for the ingredients to be burned evenly and efficiently, while also minimizing heat loss through the walls.
Another important specification is the kiln control system. This includes sensors that monitor the temperature and pressure of the kiln, as well as control systems that allow operators to adjust these parameters as needed. A reliable and effective kiln control system is essential for ensuring accurate and consistent baking results.
The fuel system is responsible for providing the kiln with the necessary fuel for combustion. Different fuels have different properties, which can affect the performance of the kiln. It is important to choose the right fuel for the specific application of the kiln and to follow best practices for fuel management to maximize efficiency.
Air delivery systems are critical for maintaining proper oxygen levels within the kiln during baking. This helps to prevent overheating and ensures that baked goods reach their optimal texture and flavor. Air delivery systems can include pumps, valves, and filters, all of which need to be carefully maintained and checked for wear and tear.
Rotationally dryers, wheels, and mills are additional components of a rotary kiln that help to improve its overall performance. They are used to spread hot air evenly throughout the kiln and to dry baked goods efficiently. Rotationally dryers and wheels are typically located near the kiln control system, while rotationally dryers and mills are often located outside the kiln.
Overall, the specifications of a rotary kiln play an essential role in ensuring that baked goods arrive at their optimal texture and flavor. By choosing the right size and shape of the kiln body, designing a reliable and effective kiln control system, selecting the appropriate fuel, implementing effective air delivery systems, using rotationally dryers and wheels, and keeping all components in good condition, operators can produce high-quality baked goods every time.
(rotary kiln tyre & roller / rotary kiln spare parts )
Applications of rotary kiln tyre & roller / rotary kiln spare parts
Rotary kilns are essential machines used in many industries, including mining, cement production, and chemical manufacturing. The Kiln consists of several components such as the rotary drum, fuel tank, temperature control system, and exhaust fan.
One of the most critical components of a rotary kiln is the rotary drum, which is responsible for transporting hot air and gases to the blast furnace. The drum is made up of several layers of ceramic plates that are heated to high temperatures, causing them to expand and contract. This expansion and contraction causes the air inside the drum to heat up and form bubbles, which are then burned by the blast furnace.
Rotary kiln spare parts include everything from drum wearers to fire bricks. These parts are crucial for maintaining the efficiency and safety of the kiln. Drum wearers help to reduce wear on the drum and prevent it from breaking down. Fire bricks, on the other hand, provide an insulating layer between the drum and the surrounding atmosphere, reducing heat loss and increasing efficiency.
Other important components of a rotary kiln include the fuel tank, temperature control system, and exhaust fan. The fuel tank stores the fuel required to power the kiln, while the temperature control system regulates the temperature of the kiln’s environment. Finally, the exhaust fan helps to remove the waste gases produced during combustion, making the kiln more efficient and environmentally friendly.
In conclusion, rotary kiln spare parts play a vital role in ensuring the performance and safety of the kiln. From drum wearers to fire bricks, these parts are designed to last for long periods of time and to meet the unique needs of each individual kiln. With proper maintenance and care, these spare parts can help to ensure that your rotary kiln runs smoothly and efficiently, producing high-quality products at all times.
Company Introduction
Established in 2001, plant Machinery Equipment Co.,ltd. focus on metal research and mining machinery spare parts. 2 factories over an area of 13,300 square meters, based on 100+ sets of equipment, our production capacity reaches 12000 Tons/Year. has passed ISO 9001 quality managment system certification in 2008.
Our mainly products are dragline excavator spare parts,rotary kiln spare parts, large modulus gear (gear shaft), gearbox ect. 40+ patents with over 45 years experience to help focus on improve the service life of spare parts. We belive that more than 80% reason of mechanical parts’ working life depends on hot processing (steel making/forging/casting/welding/heat treatment). Eight material engineers will control the quality from the original resource.
If you are interested, please feel free to contact us.
Payment
L/C, T/T, Western Union, Paypal, Credit Card etc.
Shipment
By sea, by air, by express, as customers request.
5 FAQs of rotary kiln tyre & roller / rotary kiln spare parts
1. What is the purpose of a rotary kiln tire and roller?
The purpose of a rotary kiln tire and roller is to maintain consistent temperature and pressure in the kiln, which is crucial for ensuring proper heat distribution and efficiency of combustion. The tire and roller also help prevent overheating and reduce wear on the kiln.
2. How do I replace the tire and roller in a rotary kiln?
To replace the tire and roller in a rotary kiln, you will need to access the inner workings of the kiln. Locate the tire and roller, which are usually located on either side of the kiln or at the bottom of the kiln. Carefully remove the old tire and roller, then insert the new one in place. Ensure that the new tire and roller fit snugly and securely into place.
3. Can I reuse the same tire and roller for multiple applications?
Yes, it is possible to reuse the same tire and roller for multiple applications. However, it is important to ensure that the new tire and roller meet the appropriate specifications for your specific application, as using incompatible components can cause damage to the kiln or other equipment.
4. Are there any safety precautions I should take when working with the tire and roller in a rotary kiln?
Yes, there are several safety precautions you should take when working with the tire and roller in a rotary kiln. First, make sure that the kiln is properly ventilated and that there is no fuel or other flammable materials nearby. Second, use protective gear such as gloves and goggles to protect yourself from the hot metal surfaces of the tire and roller. Finally, be aware of potential electrical hazards and follow any electrical safety guidelines provided by your supplier or manufacturer.
5. Is there a cost associated with replacing the tire and roller in a rotary kiln?
The cost of replacing the tire and roller in a rotary kiln can vary depending on several factors, including the size and type of equipment, the location and availability of replacement parts, and any labor costs involved in removing and installing the old tire and roller. It is recommended to check with your supplier or manufacturer for the most up-to-date information on pricing and availability.
(rotary kiln tyre & roller / rotary kiln spare parts )
REQUEST A QUOTE
RELATED PRODUCTS
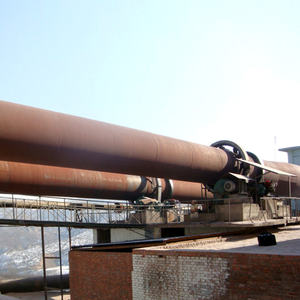
Large cement plant mill head rotary kiln spare parts welding ball mill welding drum
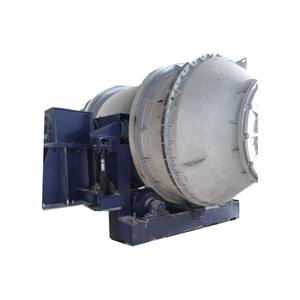
Rotary kiln for thermal processing Rotary kiln for energy-efficient operations Rotary kiln for environmental management
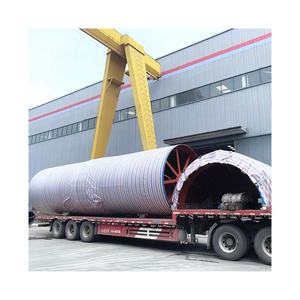
Design and manufacture environmental protection equipment rotary kiln incinerator equipment
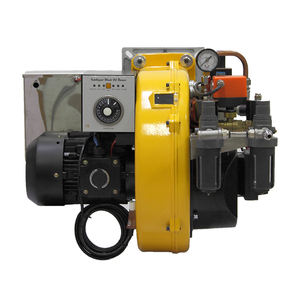
China Factory boiler air nozzle Boiler accessories Thermal power plant boiler air nozzle
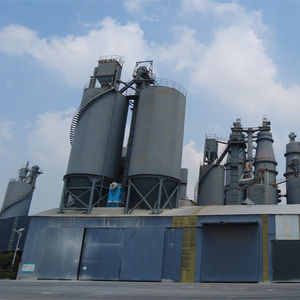
Rotary Kiln For lime, Cement Making Machinery Production Line Spare parts, Support Roller Quick Lime Rotary Kiln
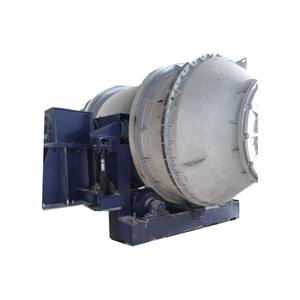