PRODUCT PARAMETERS
Description
Introduction of Rotary Kiln Support Wheel Roller And Drive Shaft Rotary Kiln Parts
A rotary kiln is a kind of industrial equipment used for material heating and processing, which is widely used in cement, metallurgy, chemical industry, etc. Rotary Kiln Support Wheel Roller And Drive Shaft Rotary Kiln Parts refers to various parts and components which are necessary for maintaining and repairing the normal operation of the rotary kiln, such as cylinder, baffle wheel, pallet, sealing device and so on.
Features and advantages of Rotary Kiln Support Wheel Roller And Drive Shaft Rotary Kiln Parts
High-temperature resistance: Due to the extremely high temperature of the working environment of the rotary kiln, the spare parts are usually made of refractory materials or special alloys to ensure that they can work stably under high temperatures.
High abrasion resistance: Long time material friction and chemical erosion require spare parts to have excellent abrasion resistance to prolong service life.
High structural strength: in order to withstand heavy loads and the pressure of continuous operation, the design of spare parts will place special emphasis on structural strength and reliability.
Easy to install and maintain: Considering the need for frequent replacement, many spare parts are designed to be simpler and easier for quick installation and maintenance.
Strong adaptability: different industries have different needs for rotary kilns, so spare parts need to have good versatility and adaptability to meet diverse application conditions.
(Rotary Kiln Support Wheel Roller And Drive Shaft Rotary Kiln Parts)
Specifications of Rotary Kiln Support Wheel Roller And Drive Shaft Rotary Kiln Parts
Rotary kiln support wheel rollers and drive shafts are critical components in rotary kiln systems. These parts ensure stable operation and efficient performance. Support wheel rollers carry the kiln’s weight and guide its rotation. They are made from high-strength steel alloys like ASTM A148 or equivalent grades. This ensures durability under heavy loads and high temperatures. The rollers have a hardened surface to resist wear from constant friction. Typical diameters range from 1.5 to 3 meters, depending on kiln size. Widths vary between 400 and 800 millimeters. Each roller is precision-machined to maintain alignment with the kiln shell. Proper alignment prevents uneven stress and extends equipment life. Lubrication systems are integrated to reduce friction between rollers and the kiln’s riding ring. Regular inspection of roller surfaces and bearings is necessary to detect cracks or wear early.
Drive shafts transmit power from the motor to the kiln’s girth gear. They are constructed from forged alloy steel, such as ASTM A322 grade 4140, for high torsional strength. Shaft diameters typically measure 200 to 500 millimeters. Lengths match the kiln’s drive assembly requirements. The shafts are machined to precise tolerances to ensure smooth power transfer. Keyways or splines are added to securely connect the shaft to couplings or gears. Heat treatment processes like quenching and tempering enhance hardness and fatigue resistance. Drive shafts operate under continuous torque, so balancing is critical to minimize vibration. Bearings and seals are installed to handle radial and axial loads while preventing contamination.
Both components require robust mounting systems. Support rollers use adjustable bases to correct minor misalignment during operation. Drive shafts are paired with flexible couplings to accommodate thermal expansion. Maintenance schedules include checking bolt tightness, lubrication levels, and surface conditions. Replacement intervals depend on operating conditions like temperature and load cycles. Proper installation and alignment during initial setup reduce long-term wear. These parts are designed for compatibility with various kiln sizes and configurations. Material quality and manufacturing precision directly impact their performance and lifespan.
(Rotary Kiln Support Wheel Roller And Drive Shaft Rotary Kiln Parts)
Applications of Rotary Kiln Support Wheel Roller And Drive Shaft Rotary Kiln Parts
Rotary kiln support wheel rollers and drive shafts are key parts in rotary kiln systems. These components handle heavy loads and high temperatures. They make sure the kiln rotates smoothly. Support wheel rollers hold the kiln’s weight. They keep the kiln aligned during rotation. This prevents uneven wear on the kiln shell. Drive shafts transfer power from the motor to the kiln. They control rotation speed. This is critical for consistent material processing. Both parts work together to maintain stable operation in harsh industrial environments.
Rotary kilns are used in cement production. Support wheel rollers and drive shafts ensure steady rotation of the kiln during clinker formation. High temperatures and heavy loads stress these parts. They are built with durable materials like alloy steel. This helps them resist wear and deformation. In metallurgy, rotary kilns process ores and metal powders. The support rollers keep the kiln balanced during heating. Drive shafts adjust rotation to match processing needs. This improves efficiency in reducing or roasting materials.
Chemical industries use rotary kilns for calcination and sintering. Support wheel rollers handle thermal expansion. Drive shafts maintain precise speed control. This ensures uniform heating of chemicals. Waste treatment plants rely on rotary kilns for incineration. The rollers and shafts endure corrosive gases and fluctuating temperatures. Their robust design minimizes downtime. Regular maintenance checks are needed. Lubrication reduces friction. Alignment tests prevent mechanical failures.
Mining operations use rotary kilns to process minerals. Support rollers stabilize the kiln during long runs. Drive shafts adapt to varying material loads. This keeps production consistent. These parts are also used in lime production. They support the kiln as limestone transforms into quicklime. Heat resistance and mechanical strength are vital here.
Quality matters for support wheel rollers and drive shafts. Precision machining ensures smooth operation. Proper installation extends their lifespan. Operators must monitor temperature and vibration. Early detection of issues avoids costly repairs. Reliable performance of these parts directly impacts kiln productivity.
Company Introduction
Established in 2001, plant Machinery Equipment Co.,ltd. focus on metal research and mining machinery spare parts. 2 factories over an area of 13,300 square meters, based on 100+ sets of equipment, our production capacity reaches 12000 Tons/Year. has passed ISO 9001 quality managment system certification in 2008.
Our mainly products are dragline excavator spare parts,rotary kiln spare parts, large modulus gear (gear shaft), gearbox ect. 40+ patents with over 45 years experience to help focus on improve the service life of spare parts. We belive that more than 80% reason of mechanical parts’ working life depends on hot processing (steel making/forging/casting/welding/heat treatment). Eight material engineers will control the quality from the original resource.
If you are interested, please feel free to contact us.
Payment
L/C, T/T, Western Union, Paypal, Credit Card etc.
Shipment
By sea, by air, by express, as customers request.
5 FAQs of Rotary Kiln Support Wheel Roller And Drive Shaft Rotary Kiln Parts
Rotary kiln support wheel rollers and drive shafts are critical for smooth operation. Here are common questions about these parts. What maintenance do support wheel rollers need? Inspect them every 1-2 months. Check for wear, cracks, or misalignment. Clean surfaces to remove debris. Lubricate bearings regularly. Proper maintenance prevents uneven wear and extends lifespan.
Why do support wheel rollers sometimes cause alignment issues? Misalignment happens over time. Heavy loads and high temperatures stress components. Loose bolts or foundation shifts change roller positions. Monitor alignment during routine checks. Adjust rollers using hydraulic jacks if needed. Correct alignment reduces strain on the kiln shell.
What materials are used for drive shafts? High-grade alloy steel is common. It handles high torque and heat. Some shafts have protective coatings against corrosion. Material choice depends on kiln size and operating conditions. Weak materials lead to fractures or bending. Replace worn shafts immediately to avoid downtime.
How do I know if a support wheel roller is failing? Listen for unusual grinding or squeaking noises. Check for uneven tread wear or flat spots. Excessive vibration during rotation signals trouble. Inspect roller surfaces for cracks or pitting. Address issues early to prevent kiln stoppages.
What causes drive shaft overheating? Friction from poor lubrication is a main cause. Misaligned gears or couplings increase resistance. Blockages in cooling systems raise temperatures. Monitor shaft temperature during operation. Ensure proper lubrication and alignment. Clean cooling channels regularly. Overheating damages bearings and gear systems.
Regular inspection and timely repairs keep these parts functional. Follow manufacturer guidelines for maintenance schedules. Use quality replacement parts to ensure reliability. Train staff to identify early signs of wear or damage. Proper care reduces unexpected breakdowns and production losses.
(Rotary Kiln Support Wheel Roller And Drive Shaft Rotary Kiln Parts)
REQUEST A QUOTE
RELATED PRODUCTS
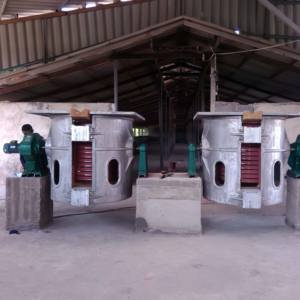
Customized Various Sizes Rotary Kiln Spare Parts Cement Ball Mill Drive Large Casting Gears
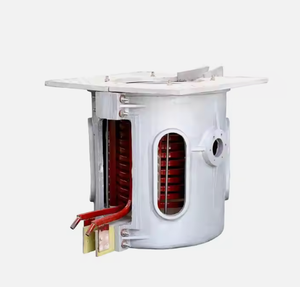
New Typesmall rotary tunnel kiln used kiln for red brick soil brick
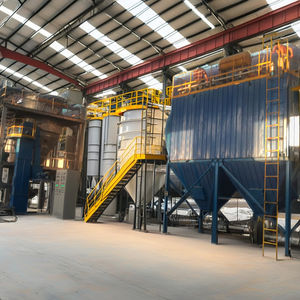
Factory Hongxing Mini 180TPD rotary kiln for calcining cement clinker lean iron ore nickel and aluminum plant with good
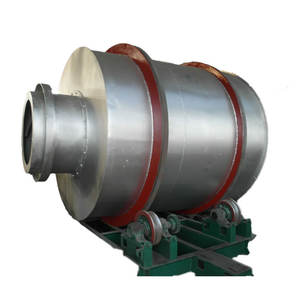
Citic Rotary kiln spare parts Rotary kiln supporting wheel bearing device Rotary kiln
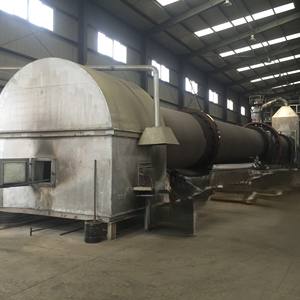
bauxite periodic rotary kiln cement 1000c cement kiln cooling fan and spare parts rotary valve for kiln machine
