PRODUCT PARAMETERS
Description
Introduction of Rotary kiln for thermal processing Rotary kiln for energy-efficient operations Rotary kiln for environmental management
A rotary kiln is a kind of industrial equipment used for material heating and processing, which is widely used in cement, metallurgy, chemical industry, etc. Rotary kiln for thermal processing Rotary kiln for energy-efficient operations Rotary kiln for environmental management refers to various parts and components which are necessary for maintaining and repairing the normal operation of the rotary kiln, such as cylinder, baffle wheel, pallet, sealing device and so on.
Features and advantages of Rotary kiln for thermal processing Rotary kiln for energy-efficient operations Rotary kiln for environmental management
High-temperature resistance: Due to the extremely high temperature of the working environment of the rotary kiln, the spare parts are usually made of refractory materials or special alloys to ensure that they can work stably under high temperatures.
High abrasion resistance: Long time material friction and chemical erosion require spare parts to have excellent abrasion resistance to prolong service life.
High structural strength: in order to withstand heavy loads and the pressure of continuous operation, the design of spare parts will place special emphasis on structural strength and reliability.
Easy to install and maintain: Considering the need for frequent replacement, many spare parts are designed to be simpler and easier for quick installation and maintenance.
Strong adaptability: different industries have different needs for rotary kilns, so spare parts need to have good versatility and adaptability to meet diverse application conditions.
(Rotary kiln for thermal processing Rotary kiln for energy-efficient operations Rotary kiln for environmental management)
Specifications of Rotary kiln for thermal processing Rotary kiln for energy-efficient operations Rotary kiln for environmental management
Rotary kilns are industrial thermal handling systems designed for high-temperature applications such as calcination, pyrolysis, incineration, and material drying. These cylindrical, revolving heating systems are crafted to deal with diverse products, from minerals and ores to hazardous waste, ensuring consistent warm circulation and ideal handling. Secret specifications include a robust steel covering lined with refractory materials (e.g., high-alumina blocks or ceramic fiber) to endure temperatures as much as 1,600 ° C. Kiln sizes range from 1.5 to 5 meters, with lengths extending up to 100 meters, depending on throughput demands. Variable-speed drives (0.5– 5 RPM) and flexible tilt (2– 5 °) allow specific control over product retention time, critical for process performance. Warm sources include gas, oil, biomass, or waste-derived fuels, incorporated with advanced burner systems for steady burning. Energy-efficient operations are achieved via warmth recuperation systems, such as preheaters or recuperators, which reuse exhaust warmth to preheat incoming product or combustion air, lowering fuel consumption by approximately 30%. Insulation upgrades and lessened air leakages even more enhance thermal efficiency. Environmental management functions consist of exhaust control systems like electrostatic precipitators, baghouse filters, or scrubbers to record particle matter, acidic gases (SOx, HCl), and unstable organic compounds (VOCs). Low-NOx heaters and organized burning restriction nitrogen oxide discharges, while real-time surveillance by means of gas analyzers makes certain conformity with air top quality standards. Rotating kilns likewise sustain waste co-processing, transforming industrial by-products or contaminated materials right into alternate gas, minimizing garbage dump reliance. Automated control systems maximize temperature level profiles, air flow, and feed rates, making certain consistent outcome while decreasing energy use and exhausts. Created for sturdiness and scalability, rotating kilns offer sectors like cement, metallurgy, chemicals, and waste management, aligning thermal processing with sustainability goals through power recuperation, emission decrease, and source performance.
(Rotary kiln for thermal processing Rotary kiln for energy-efficient operations Rotary kiln for environmental management)
Applications of Rotary kiln for thermal processing Rotary kiln for energy-efficient operations Rotary kiln for environmental management
Rotating kilns are versatile thermal processing systems extensively made use of across sectors for high-temperature material therapy. In cement production, they promote calcination, converting sedimentary rock into lime, while in metallurgy, they refine ores and steels with decrease and roasting. The ceramics and refractories sectors rely on rotary kilns for sintering and vitrification, ensuring sturdy end products. Furthermore, these kilns handle dangerous and clinical waste by breaking down facility pollutants at extreme temperature levels, rendering them inert. Their capacity to maintain constant, controlled heat makes them suitable for varied thermal applications, from chemical manufacturing to advanced product synthesis. Power effectiveness is a hallmark of contemporary rotary kilns. Advanced makes incorporate warm healing systems that capture exhaust gases to preheat incoming products, lowering gas consumption. Insulation upgrades lessen thermal loss, while optimized airflow makes sure consistent temperature level circulation. Variable-speed drives change rotational speed based on real-time lots demands, reducing energy waste. Some kilns leverage alternative gas like biomass or waste-derived materials, reducing nonrenewable fuel source dependancy and functional expenses. Indirect home heating configurations better boost effectiveness by isolating combustion gases from processed materials, preserving warmth honesty. These technologies align with international sustainability goals, using markets a course to lower carbon impacts without compromising productivity. Ecological management is an additional crucial application. Rotating kilns master exhaust control, using heats to break down unstable natural substances (VOCs) and unsafe air pollutants (HAPs). They securely treat contaminated dirts and industrial by-products, converting contaminants right into secure deposits. For material recycling, kilns recover beneficial metals from digital waste or invested catalysts, drawing away waste from landfills. Integrated pollution control systems– such as scrubbers, baghouses, and electrostatic precipitators– capture particulate matter and neutralize acidic gases, making sure compliance with stringent environmental laws. By sustaining waste-to-energy campaigns and circular economy methods, rotating kilns lower ecological impact while allowing resource recovery. Their versatility throughout thermal, power, and environmental applications positions them as important devices for markets making every effort to balance functional efficiency with sustainability.
Company Introduction
Established in 2001, plant Machinery Equipment Co.,ltd. focus on metal research and mining machinery spare parts. 2 factories over an area of 13,300 square meters, based on 100+ sets of equipment, our production capacity reaches 12000 Tons/Year. has passed ISO 9001 quality managment system certification in 2008.
Our mainly products are dragline excavator spare parts,rotary kiln spare parts, large modulus gear (gear shaft), gearbox ect. 40+ patents with over 45 years experience to help focus on improve the service life of spare parts. We belive that more than 80% reason of mechanical parts’ working life depends on hot processing (steel making/forging/casting/welding/heat treatment). Eight material engineers will control the quality from the original resource.
If you are interested, please feel free to contact us.
Payment
L/C, T/T, Western Union, Paypal, Credit Card etc.
Shipment
By sea, by air, by express, as customers request.
5 FAQs of Rotary kiln for thermal processing Rotary kiln for energy-efficient operations Rotary kiln for environmental management
Rotary kilns are essential for high-temperature thermal processing. How do they maintain consistent heat distribution? Rotary kilns use a rotating cylinder to ensure materials are evenly exposed to heat, preventing hotspots and ensuring uniform processing. Advanced temperature control systems and refractory linings optimize thermal efficiency, making them ideal for processes like calcination or pyrolysis.
What makes rotary kilns energy-efficient? Modern designs incorporate heat recovery systems, such as preheaters and waste heat boilers, which reuse exhaust heat to preheat incoming materials or generate power. Insulation upgrades and optimized combustion systems reduce fuel consumption, lowering operational costs and carbon footprint. Variable-speed drives also adjust rotation to match processing demands, saving energy.
How do rotary kilns support environmental management? They are equipped with emission control technologies like scrubbers, bag filters, and selective catalytic reduction (SCR) systems to capture particulate matter, NOx, SOx, and volatile organic compounds. Some kilns co-process industrial waste, converting hazardous materials into inert byproducts while recovering energy, aligning with circular economy principles and reducing landfill dependency.
Can rotary kilns handle diverse materials? Yes. Their flexible design accommodates varying material sizes, moisture levels, and chemical compositions. Adjustable rotation speed, inclination, and temperature profiles allow customization for minerals, biomass, waste, or chemicals. This versatility ensures efficient processing across industries like cement, metallurgy, and waste management without compromising output quality.
What maintenance ensures long-term reliability? Regular inspections of refractory linings, seals, and bearings prevent unexpected downtime. Predictive maintenance tools monitor vibration, temperature, and wear patterns, enabling timely repairs. Proper alignment and lubrication of rotating components extend lifespan, while automated control systems reduce human error, ensuring stable, eco-friendly operations. These practices minimize environmental risks and sustain energy efficiency over the kiln’s lifecycle.
(Rotary kiln for thermal processing Rotary kiln for energy-efficient operations Rotary kiln for environmental management)
REQUEST A QUOTE
RELATED PRODUCTS
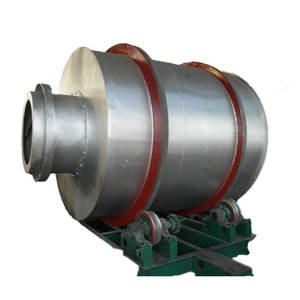
China top Rotary kiln /Rotary kiln incinerator
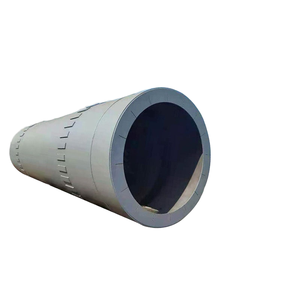
Continuous Non-metallic Rotary Kiln With 30-300kg/h Capacity
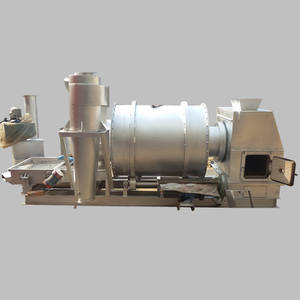
Professional rotary kiln spare parts steel plate/roller/refractory bricks rotary kiln
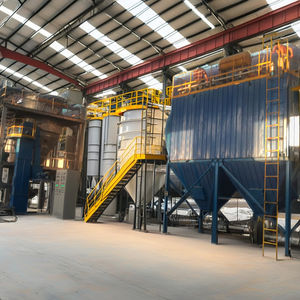
Cement Rotary Kiln Seal Rotary Kiln Barrel Parts
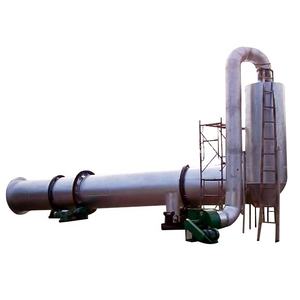
Motorcycle spare parts rubber damper GN125 GS125 motorcycle accessories para motos in china with high quality
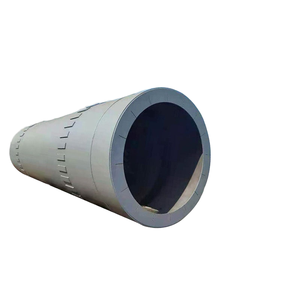