PRODUCT PARAMETERS
Description
Introduction of Rotary Kiln For lime, Cement Making Machinery Production Line Spare parts, Support Roller Quick Lime Rotary Kiln
A rotary kiln is a kind of industrial equipment used for material heating and processing, which is widely used in cement, metallurgy, chemical industry, etc. Rotary Kiln For lime, Cement Making Machinery Production Line Spare parts, Support Roller Quick Lime Rotary Kiln refers to various parts and components which are necessary for maintaining and repairing the normal operation of the rotary kiln, such as cylinder, baffle wheel, pallet, sealing device and so on.
Features and advantages of Rotary Kiln For lime, Cement Making Machinery Production Line Spare parts, Support Roller Quick Lime Rotary Kiln
High-temperature resistance: Due to the extremely high temperature of the working environment of the rotary kiln, the spare parts are usually made of refractory materials or special alloys to ensure that they can work stably under high temperatures.
High abrasion resistance: Long time material friction and chemical erosion require spare parts to have excellent abrasion resistance to prolong service life.
High structural strength: in order to withstand heavy loads and the pressure of continuous operation, the design of spare parts will place special emphasis on structural strength and reliability.
Easy to install and maintain: Considering the need for frequent replacement, many spare parts are designed to be simpler and easier for quick installation and maintenance.
Strong adaptability: different industries have different needs for rotary kilns, so spare parts need to have good versatility and adaptability to meet diverse application conditions.
(Rotary Kiln For lime, Cement Making Machinery Production Line Spare parts, Support Roller Quick Lime Rotary Kiln)
Specifications of Rotary Kiln For lime, Cement Making Machinery Production Line Spare parts, Support Roller Quick Lime Rotary Kiln
The Rotary Kiln for lime and cement production is a high-efficiency industrial furnace designed for calcining limestone, dolomite, and other raw materials to produce quicklime or cement clinker. It features a robust cylindrical steel shell lined with refractory bricks to withstand extreme temperatures (up to 1450°C for cement). Standard specifications include a diameter range of 1.9–4.8 meters and a length of 36–150 meters, customizable based on capacity requirements. The kiln operates at a tilt of 3–4 degrees and rotates at 0.5–1.5 RPM, ensuring optimal material mixing and heat transfer. Production capacity varies from 200–1200 tons per day for lime and up to 10,000 tons daily for large-scale cement plants. Fuel options include coal, natural gas, oil, or biomass, with automated control systems for temperature, airflow, and rotation speed.
Support rollers are critical spare parts in rotary kiln systems, designed to bear the kiln’s weight and ensure smooth rotation. Constructed from high-strength alloy steel (e.g., ZG42CrMo), they undergo heat treatment for durability under heavy loads (up to 500 tons) and high temperatures. Standard roller diameters range from 600–2000 mm, with widths of 400–1200 mm. They feature advanced lubrication systems and are mounted on adjustable bases for alignment precision.
Quick Lime Rotary Kilns emphasize energy efficiency, with preheaters to recover waste heat and reduce fuel consumption by 20–30%. They include dust removal systems (bag filters/ESP) to meet environmental standards. Key components include drive systems (main motor: 55–200 kW, gear reducers), thrust rollers, and kiln seals to prevent air leakage.
Spare parts like girth gears, pinions, bearings (spherical roller type), and refractory linings are engineered for longevity and compatibility with major kiln brands. Customizable solutions are available for wear-prone parts, including heat-resistant alloy castings.
Applications span cement plants, lime factories, and metallurgy. Benefits include high thermal efficiency, low maintenance, and adaptability to diverse raw materials. Support rollers ensure operational stability, minimizing downtime. For inquiries, technical support and global logistics ensure timely delivery of machinery and spare parts.
(Rotary Kiln For lime, Cement Making Machinery Production Line Spare parts, Support Roller Quick Lime Rotary Kiln)
Applications of Rotary Kiln For lime, Cement Making Machinery Production Line Spare parts, Support Roller Quick Lime Rotary Kiln
Rotary kilns are versatile thermal processing machines integral to industries like lime and cement production. In lime manufacturing, rotary kilns calcine limestone (calcium carbonate) at high temperatures (900–1,200°C) to produce quicklime (calcium oxide). This process, known as calcination, drives off carbon dioxide, yielding a material critical for steelmaking, water treatment, chemical production, and construction. Rotary kilns for lime are designed for efficient heat transfer, uniform temperature distribution, and controlled retention time, ensuring high-purity quicklime with minimal energy consumption. Their robust construction handles abrasive materials, making them ideal for large-scale industrial applications.
In cement production, rotary kilns are the heart of the manufacturing line, facilitating the conversion of raw materials like limestone, clay, and silica into clinker. The kiln’s high-temperature zones (up to 1,450°C) enable key reactions: calcination, sintering, and nodulization. Integrated with preheaters and coolers, modern rotary kilns optimize energy efficiency and output. Cement kilns require precision engineering to manage thermal expansion, mechanical stress, and abrasive wear, ensuring continuous operation in harsh environments.
Spare parts for cement and lime production lines are vital for minimizing downtime and maintaining productivity. Critical components include refractory linings (heat resistance), gaskets (sealing), burner nozzles (fuel efficiency), and drive systems (rotation control). High-quality spare parts enhance kiln longevity, reduce maintenance costs, and ensure process consistency. Customized solutions, such as alloy-based wear parts or advanced refractory materials, address specific operational challenges.
Support rollers are essential for rotary kiln functionality, bearing the kiln’s weight and enabling smooth rotation. Designed with heavy-duty alloys and heat-resistant coatings, they withstand extreme loads and temperatures. Proper alignment and lubrication prevent uneven wear, vibration, and mechanical failure. Regular inspection and timely replacement of support rollers are crucial to avoid operational disruptions. Upgraded designs with self-aligning features or automated lubrication systems further enhance reliability.
In summary, rotary kilns drive efficiency in lime and cement industries, supported by durable machinery and precision-engineered components. Investing in high-performance spare parts and robust support rollers ensures operational continuity, cost-effectiveness, and long-term ROI for production lines.
Company Introduction
Established in 2001, plant Machinery Equipment Co.,ltd. focus on metal research and mining machinery spare parts. 2 factories over an area of 13,300 square meters, based on 100+ sets of equipment, our production capacity reaches 12000 Tons/Year. has passed ISO 9001 quality managment system certification in 2008.
Our mainly products are dragline excavator spare parts,rotary kiln spare parts, large modulus gear (gear shaft), gearbox ect. 40+ patents with over 45 years experience to help focus on improve the service life of spare parts. We belive that more than 80% reason of mechanical parts’ working life depends on hot processing (steel making/forging/casting/welding/heat treatment). Eight material engineers will control the quality from the original resource.
If you are interested, please feel free to contact us.
Payment
L/C, T/T, Western Union, Paypal, Credit Card etc.
Shipment
By sea, by air, by express, as customers request.
5 FAQs of Rotary Kiln For lime, Cement Making Machinery Production Line Spare parts, Support Roller Quick Lime Rotary Kiln
1. **What is the role of a support roller in a rotary kiln for lime or cement production?**
Support rollers are critical components in rotary kilns, responsible for bearing the kiln’s weight and ensuring smooth rotation. They align the kiln shell, minimize friction, and distribute thermal and mechanical stresses evenly. Properly functioning support rollers prevent misalignment, reduce wear on tires and rollers, and maintain operational stability, directly impacting kiln efficiency and longevity.
2. **How often should support rollers be inspected or maintained?**
Support rollers require regular inspections every 3–6 months, depending on operational intensity and environmental conditions. Key checks include monitoring lubrication levels, wear patterns, alignment, and surface cracks. Preventive maintenance, such as regrinding rollers or replacing worn-out bearings, should be performed immediately if uneven wear, vibrations, or overheating are detected to avoid unplanned downtime.
3. **What causes premature wear in rotary kiln support rollers?**
Common causes include misalignment of the kiln axis, improper lubrication, excessive load due to uneven tire wear, or material buildup on rollers. Environmental factors like dust, moisture, or high temperatures can accelerate corrosion or surface degradation. Regular alignment checks, using high-temperature-resistant greases, and ensuring clean roller surfaces help mitigate these issues.
4. **How do I choose the right spare support rollers for my rotary kiln?**
Select rollers based on compatibility with your kiln’s specifications, including diameter, load capacity, and rotational speed. Opt for rollers made from high-grade alloy steel with heat treatment for durability. Partner with OEM-certified suppliers or reputable manufacturers to ensure dimensional accuracy and material quality. Customized solutions may be needed for kilns with unique operating conditions.
5. **Can upgrading support rollers improve kiln performance?**
Yes. Advanced support rollers with improved materials (e.g., forged steel), precision-machined surfaces, or anti-wear coatings enhance load distribution and reduce friction. Upgrades like automated lubrication systems or self-aligning roller designs can further optimize kiln stability, lower energy consumption, and extend service intervals. Always consult technical experts to align upgrades with your kiln’s operational requirements.
(Rotary Kiln For lime, Cement Making Machinery Production Line Spare parts, Support Roller Quick Lime Rotary Kiln)
REQUEST A QUOTE
RELATED PRODUCTS
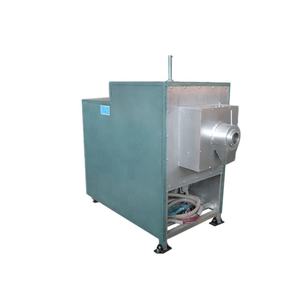
Rotary Kiln Bauxite RKB 83/80/75/70
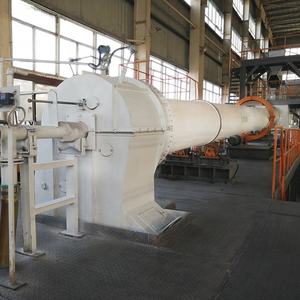
MIDDIA Industrial Electrical Technical Machinery Custom High Heat Resistant Ceramics Alumina Structural parts
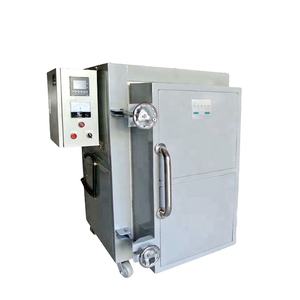
Large Gear For rotary kiln Casting Steel rotary kiln parts Ball Mill Gears For
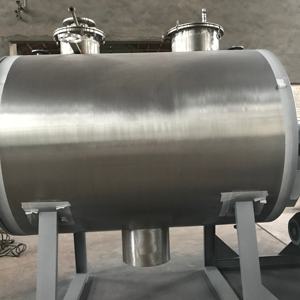
Cast Iron Steel Rotary Kiln Spare Parts Roller rotary Kiln Tyre rotary kiln wheel belt for cement and mining machinery

rotary kiln tyre & roller / rotary kiln spare parts
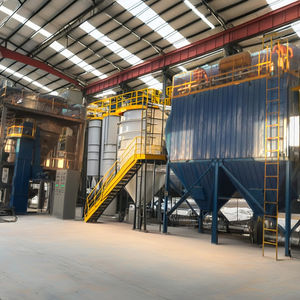