PRODUCT PARAMETERS
Description
Introduction of Rotary Industry KIln For Powder Sintering and Pellet Sintering
A rotary kiln is a kind of industrial equipment used for material heating and processing, which is widely used in cement, metallurgy, chemical industry, etc. Rotary Industry KIln For Powder Sintering and Pellet Sintering refers to various parts and components which are necessary for maintaining and repairing the normal operation of the rotary kiln, such as cylinder, baffle wheel, pallet, sealing device and so on.
Features and advantages of Rotary Industry KIln For Powder Sintering and Pellet Sintering
High-temperature resistance: Due to the extremely high temperature of the working environment of the rotary kiln, the spare parts are usually made of refractory materials or special alloys to ensure that they can work stably under high temperatures.
High abrasion resistance: Long time material friction and chemical erosion require spare parts to have excellent abrasion resistance to prolong service life.
High structural strength: in order to withstand heavy loads and the pressure of continuous operation, the design of spare parts will place special emphasis on structural strength and reliability.
Easy to install and maintain: Considering the need for frequent replacement, many spare parts are designed to be simpler and easier for quick installation and maintenance.
Strong adaptability: different industries have different needs for rotary kilns, so spare parts need to have good versatility and adaptability to meet diverse application conditions.
(Rotary Industry KIln For Powder Sintering and Pellet Sintering)
Specifications of Rotary Industry KIln For Powder Sintering and Pellet Sintering
The rotating kiln for powder sintering and pellet sintering handles high-temperature handling efficiently. The kiln body uses durable steel with heat-resistant alloy linings. It endures constant procedure at temperatures approximately 1700 ° C. The interior diameter ranges from 1.5 to 4 meters. The length varies between 15 and 50 meters. These dimensions suit various production scales. The turning rate changes from 0.5 to 5 RPM. This control guarantees even material motion. An equipment system and electrical motor drive the turning. The motor power depends upon kiln size. Criterion models utilize 30 to 200 kW electric motors.
The heater relies on gas, oil, or electric components. Fuel-based models include burners with specific flame control. Electric variations use silicon carbide rods for consistent warmth distribution. Thermal insulation layers reduce power loss. Refractory products line the interior. Alumina blocks and ceramic fiber modules take care of severe warmth. The kiln tilts a little for steady material circulation. Flexible tilt angles range from 2 to 5 degrees. This layout avoids blocking.
Temperature level zones split the kiln right into preheating, sintering, and cooling down areas. Sensors keep track of each zone. Real-time data feeds right into an automated control board. Operators change specifications remotely. The air conditioning system uses air or water jets. It lowers product temperatures to safe handling levels. Exhaust gases pass through filters. Exhaust standards satisfy ecological regulations.
The kiln refines products like steel powders, porcelains, and minerals. Feed prices vary from 500 kg to 20 loads per hour. Pellet sizes in between 5 mm and 50 mm work with adjustable settings. Moisture content in resources must stay listed below 5%. High-purity inert gases avoid oxidation throughout sintering. Gas circulation prices change based upon material type.
Maintenance access points simplify inspections. Detachable panels and assessment ports lower downtime. Safety and security functions include pressure safety valve and emergency situation shutdowns. The kiln structure utilizes corrosion-resistant finishings. Installment requires an enhanced concrete foundation. Power supply needs match regional commercial requirements. Functional training covers setup, security procedures, and troubleshooting. Manufacturing capacity ranges with modular layouts. Customized configurations sustain specific product requirements.
(Rotary Industry KIln For Powder Sintering and Pellet Sintering)
Applications of Rotary Industry KIln For Powder Sintering and Pellet Sintering
Rotary commercial kilns play a vital role in powder sintering and pellet sintering processes. These kilns are big turning cyndrical tubes heated up to high temperatures. They handle materials uniformly. This makes them suitable for industries requiring accurate thermal therapy.
In powder sintering, rotating kilns turn great powders right into solid products. The powders go into the kiln. Warmth triggers particles to bond without melting completely. This approach works for steels, porcelains, and composite materials. Uniform heating prevents hotspots. Constant item quality is attained. Industries like metallurgy and advanced porcelains rely on this. Production scales efficiently. Power use remains controlled.
Pellet sintering makes use of rotary kilns to solidify small ore or recycled product pellets. Raw pellets feed right into the rotating kiln. High temperatures create solid, dense pellets. These pellets deal with transportation and smelting much better. Steel and mining sectors utilize this. Thermal therapy guarantees uniformity. Completed pellets withstand damaging. This improves efficiency in steel extraction.
Rotating kilns adjust to different products. Changing rotation rate or temperature meets particular needs. Operators control air movement and gas mix. This versatility supports diverse industrial objectives. Kilns deal with rough or destructive products. Lasting liners decrease downtime. Upkeep remains simple.
Energy efficiency issues. Rotary kilns recycle heat from exhaust gases. Fuel prices drop. Discharges lower. Modern styles consist of warm healing systems. Environmental guidelines are satisfied. Functional expenses stay low.
Automation improves integrity. Sensors check temperature level and turning. Real-time information changes procedures. Human error is minimized. Safety and security boosts. Manufacturing runs nonstop. Outcome remains steady.
Rotating kilns serve crucial functions in sintering. They deliver precision, toughness, and effectiveness. Industries trust fund them for large-scale material processing. Efficiency meets high standards. Demanding applications are managed efficiently.
Company Introduction
Established in 2001, plant Machinery Equipment Co.,ltd. focus on metal research and mining machinery spare parts. 2 factories over an area of 13,300 square meters, based on 100+ sets of equipment, our production capacity reaches 12000 Tons/Year. has passed ISO 9001 quality managment system certification in 2008.
Our mainly products are dragline excavator spare parts,rotary kiln spare parts, large modulus gear (gear shaft), gearbox ect. 40+ patents with over 45 years experience to help focus on improve the service life of spare parts. We belive that more than 80% reason of mechanical parts’ working life depends on hot processing (steel making/forging/casting/welding/heat treatment). Eight material engineers will control the quality from the original resource.
If you are interested, please feel free to contact us.
Payment
L/C, T/T, Western Union, Paypal, Credit Card etc.
Shipment
By sea, by air, by express, as customers request.
5 FAQs of Rotary Industry KIln For Powder Sintering and Pellet Sintering
A rotary kiln for powder sintering and pellet sintering heats materials to high temperatures to bond particles. It rotates to ensure even heat distribution. This process improves material strength and stability. Here are common questions about rotary kilns in sintering.
What is a rotary kiln used for in sintering? It processes materials like metal powders or ceramic pellets by heating them. The rotation keeps materials moving. This prevents uneven sintering. The result is consistent product quality.
Why choose a rotary kiln over other sintering methods? Rotary kilns handle continuous production. They work for large batches. Heat distribution is better compared to static furnaces. This reduces energy waste. Maintenance costs stay low due to simple design.
What materials can a rotary kiln sinter? Metals like stainless steel, titanium, or iron powders are common. Ceramic materials include alumina or zirconia. Some composite materials with mixed powders work too. The kiln adjusts temperature profiles to match material needs.
What temperature range does a rotary kiln operate at for sintering? Most processes run between 1200°C and 1600°C. Exact temperatures depend on material properties. Thermocouples and control systems keep temperatures stable. This avoids overheating or under-sintering.
How is maintenance handled for a rotary kiln? Regular checks focus on the kiln’s seals and refractory lining. Rotation gears need lubrication. Burners and heat sensors are cleaned to prevent blockages. Downtime is scheduled between production cycles. Proper upkeep extends the kiln’s lifespan.
(Rotary Industry KIln For Powder Sintering and Pellet Sintering)
REQUEST A QUOTE
RELATED PRODUCTS
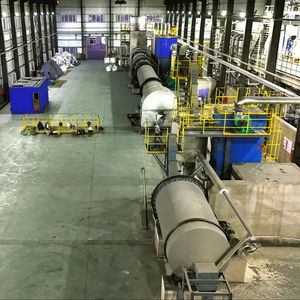
Rotary kiln and cement ball mill spare pasts wheel and ring gear large steel spur gear casting girth gear
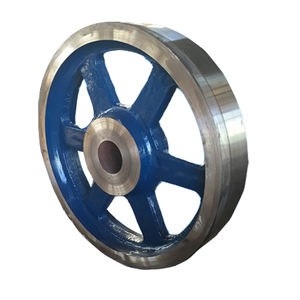
Clay Aggregate Production Line Ceramic Pelletizer LECA Rotary Kiln Factory Direct
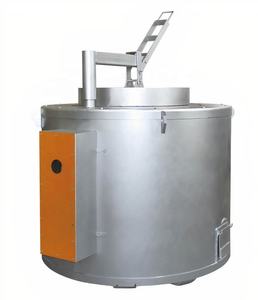
Four Channel Cement Rotary Kiln Industry Double Swirl Rotary Kiln Burner Double Swirl Rotary Kiln Burner For Cement Production
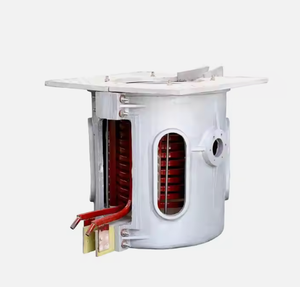
Roller and shaft of rotary kiln
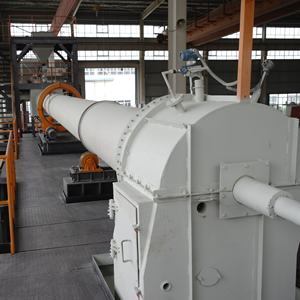
OEM Industry Machinery Parts Large Girth Gears and Pinions for Rotary Kiln /Ball Mill /Cement Mixer
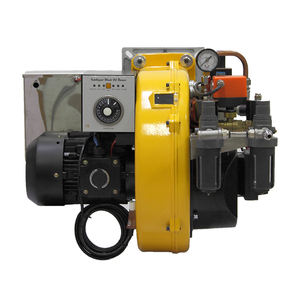