PRODUCT PARAMETERS
Description
Introduction of Roller and shaft of rotary kiln
A rotary kiln is a kind of industrial equipment used for material heating and processing, which is widely used in cement, metallurgy, chemical industry, etc. Roller and shaft of rotary kiln refers to various parts and components which are necessary for maintaining and repairing the normal operation of the rotary kiln, such as cylinder, baffle wheel, pallet, sealing device and so on.
Features and advantages of Roller and shaft of rotary kiln
High-temperature resistance: Due to the extremely high temperature of the working environment of the rotary kiln, the spare parts are usually made of refractory materials or special alloys to ensure that they can work stably under high temperatures.
High abrasion resistance: Long time material friction and chemical erosion require spare parts to have excellent abrasion resistance to prolong service life.
High structural strength: in order to withstand heavy loads and the pressure of continuous operation, the design of spare parts will place special emphasis on structural strength and reliability.
Easy to install and maintain: Considering the need for frequent replacement, many spare parts are designed to be simpler and easier for quick installation and maintenance.
Strong adaptability: different industries have different needs for rotary kilns, so spare parts need to have good versatility and adaptability to meet diverse application conditions.
(Roller and shaft of rotary kiln)
Specifications of Roller and shaft of rotary kiln
The roller and shaft setting up is a crucial part of a rotary kiln, created to support the kiln’s rotating cyndrical tube and make certain smooth, secure operation under high temperatures and hefty loads. Below are the crucial requirements for rollers and shafts in a rotary kiln system:
** Roller Specs **:.
– ** Product **: Normally fabricated from high-strength built steel or alloy steel (e.g., 42CrMo, 35CrMo) to hold up against severe mechanical anxiety and thermal growth. Warm therapy procedures like appeasing and toughening up improve hardness (as much as 50-60 HRC) and put on resistance.
– ** Capacities **: Size arrays from 500 mm to 2000 mm, depending on kiln size and lots capacity. Size varies to match the kiln covering’s size, with precision-machined surface areas for uniform contact with the tire.
– ** Tons Ability **: Developed to support kiln weights surpassing 1,000 lots, with tons distribution maximized to reduce deflection. Fixed and vibrant load scores are computed based upon kiln diameter, rotational speed, and material density.
– ** Surface Finish **: Ground to tight resistances (IT6-IT7) to make sure smooth turning and reduce friction. Hardened surfaces may consist of induction-hardened layers (2-5 mm deepness) to withstand abrasion.
– ** Placement **: Flexible roller bases permit exact positioning (within 0.1-0.3 mm/m) to keep kiln axis stability and protect against unequal tire wear.
** Shaft Specifications **:.
– ** Material **: High-grade carbon steel or alloy steel (e.g., 45 # steel, 40Cr) with exceptional torsional strength and fatigue resistance. Shafts go through ultrasonic testing to detect internal flaws.
– ** Size and Length **: Shaft sizes vary from 200 mm to 1,000 mm, symmetrical to the roller load. Length corresponds to the kiln’s support spacing, frequently exceeding 3-5 meters for big kilns.
– ** Bearings **: Fitted with round roller bearings or hydrodynamic bearings to suit axial and radial pressures. Bearing real estates are dust-sealed and lubed for high-temperature environments.
– ** Thermal Resistance **: Covered or heat-treated to sustain ambient temperature levels approximately 300 ° C, with cooling fins or water-cooled designs for extreme-heat applications.
– ** Tolerances **: Machined to exact straightness (≤ 0.05 mm/m) and concentricity (≤ 0.1 mm) to prevent vibration and ensure seamless power transmission from the drive system.
Both rollers and shafts are engineered for durability, with routine inspections advised to keep track of wear, placement, and lubrication. Custom-made styles are offered to match details kiln criteria, including inclination angle, rotational rate, and processing material. Compliance with worldwide criteria (ISO, ASTM, or hubbub) guarantees integrity in concrete, metallurgy, and chemical markets.
(Roller and shaft of rotary kiln)
Applications of Roller and shaft of rotary kiln
Roller and shaft systems are essential components in rotary kilns, playing a crucial duty in making sure reliable and trustworthy operation throughout numerous commercial procedures. Rotating kilns are high-temperature processing units utilized in sectors such as concrete production, metallurgy, chemical processing, and waste administration. The rollers and shafts support the kiln’s revolving cylinder, allowing it to deal with hefty tons, preserve positioning, and hold up against extreme thermal and mechanical tensions.
The main application of rollers in a rotating kiln is to supply architectural assistance and assist in smooth rotation. Kiln rollers are positioned under the kiln’s tires (riding rings) and birth the entire weight of the turning drum, which can exceed thousands of heaps. Precision-engineered rollers disperse the load evenly, decreasing wear and stopping contortion. They are normally made from high-grade steel or specialized alloys to withstand high temperatures, abrasion, and cyclic loading. Correct positioning of rollers guarantees the kiln rotates along its main axis, lowering vibration and mechanical failings.
Shafts in rotary kilns are essential to transmitting torque from the drive system to the kiln covering. They link to girth gears or drive settings up, enabling controlled turning at adjustable rates. Kiln shafts must resist torsional stress and anxieties, thermal expansion, and fatigue, often needing warm treatment or innovative metallurgy for durability. In addition, assistance shafts in drive roller assemblies assist handle axial movement triggered by thermal development during heating and cooling cycles, maintaining kiln security.
In cement manufacturing, rollers and shafts make sure regular clinker formation by enabling consistent warm circulation as the kiln turns. In metallurgy, they support calcination and reduction processes by maintaining precise rotational control. For waste incineration or unsafe product processing, robust rollers and shafts stand up to corrosive environments and fluctuating temperature levels.
Routine upkeep of these elements is essential. Monitoring wear, lubrication, and alignment avoids unexpected downtime and expands service life. Advanced creates integrate self-aligning rollers or hydraulic systems to automatically adjust positioning, enhancing operational performance. By combining mechanical stamina with thermal resistance, roller and shaft systems are crucial in optimizing rotating kiln efficiency, making sure productivity, safety, and cost-effectiveness in demanding industrial applications.
Company Introduction
Established in 2001, plant Machinery Equipment Co.,ltd. focus on metal research and mining machinery spare parts. 2 factories over an area of 13,300 square meters, based on 100+ sets of equipment, our production capacity reaches 12000 Tons/Year. has passed ISO 9001 quality managment system certification in 2008.
Our mainly products are dragline excavator spare parts,rotary kiln spare parts, large modulus gear (gear shaft), gearbox ect. 40+ patents with over 45 years experience to help focus on improve the service life of spare parts. We belive that more than 80% reason of mechanical parts’ working life depends on hot processing (steel making/forging/casting/welding/heat treatment). Eight material engineers will control the quality from the original resource.
If you are interested, please feel free to contact us.
Payment
L/C, T/T, Western Union, Paypal, Credit Card etc.
Shipment
By sea, by air, by express, as customers request.
5 FAQs of Roller and shaft of rotary kiln
What is the purpose of rollers and shafts in a rotary kiln? Rollers and shafts are critical components that support the kiln’s rotating cylinder, ensuring smooth rotation and even distribution of the kiln’s weight. The rollers act as bearings, reducing friction between the kiln shell and the supporting structure, while the shafts transmit rotational force and maintain alignment. Together, they enable efficient heat transfer and material processing within the kiln.
How do I maintain roller and shaft systems in a rotary kiln? Regular inspection is key. Check for wear, cracks, or deformation on roller surfaces and shafts. Lubricate bearings and joints to minimize friction and overheating. Monitor alignment using laser tools or traditional methods to prevent uneven stress. Clean debris and material buildup around rollers to avoid obstructions. Implement thermal imaging or vibration analysis to detect early signs of damage. Replace worn components promptly to prevent operational downtime.
What materials are used for manufacturing rollers and shafts? Rollers and shafts are typically made from high-grade alloy steels like 4340 or 316 stainless steel for strength and heat resistance. Surfaces are often hardened through processes like induction hardening or carburizing to withstand abrasion and high temperatures. Some applications use heat-resistant coatings or ceramic composites to enhance durability in extreme environments.
What are common issues affecting rollers and shafts? Misalignment is a frequent problem, leading to uneven wear and increased energy consumption. Bearing failures due to inadequate lubrication or contamination can cause overheating. Shaft bending or cracking may occur from excessive load or thermal stress. Roller surface pitting or scoring often results from abrasive materials or poor alignment. Regular monitoring and timely adjustments help mitigate these issues.
How long do rollers and shafts last in a rotary kiln? Lifespan varies based on operating conditions, material quality, and maintenance. Typically, rollers last 5–10 years, while shafts may endure 8–15 years with proper care. Harsh environments, high temperatures, or abrasive materials can shorten this. Signs of failure include abnormal noise, vibration, visible cracks, or uneven wear. Proactive replacement during scheduled downtime maximizes kiln efficiency and safety.
(Roller and shaft of rotary kiln)
REQUEST A QUOTE
RELATED PRODUCTS
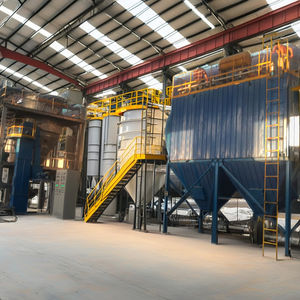
Cement Rotary Kiln Seal Rotary Kiln Barrel Parts
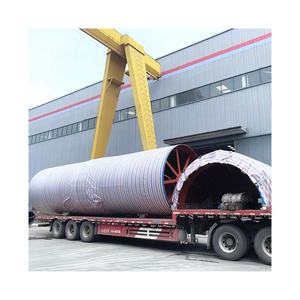
Design and manufacture environmental protection equipment rotary kiln incinerator equipment
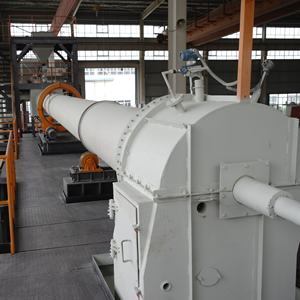
Small Scale Rotary Kiln Making Quick Active Lime Processing Plant
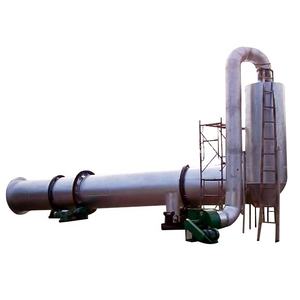
Motorcycle spare parts rubber damper GN125 GS125 motorcycle accessories para motos in china with high quality
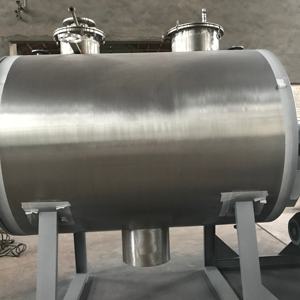
Cast Iron Steel Rotary Kiln Spare Parts Roller rotary Kiln Tyre rotary kiln wheel belt for cement and mining machinery
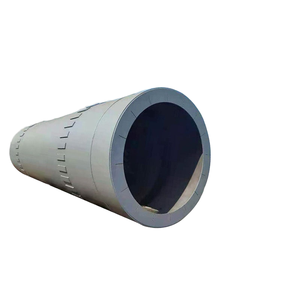