PRODUCT PARAMETERS
Description
Introduction of Metal Metallurgy Machinery Top ing For Producing Parts Advanced Machines High Quality Arc Metal Industrial Sintering Furnace
A rotary kiln is a kind of industrial equipment used for material heating and processing, which is widely used in cement, metallurgy, chemical industry, etc. Metal Metallurgy Machinery Top ing For Producing Parts Advanced Machines High Quality Arc Metal Industrial Sintering Furnace refers to various parts and components which are necessary for maintaining and repairing the normal operation of the rotary kiln, such as cylinder, baffle wheel, pallet, sealing device and so on.
Features and advantages of Metal Metallurgy Machinery Top ing For Producing Parts Advanced Machines High Quality Arc Metal Industrial Sintering Furnace
High-temperature resistance: Due to the extremely high temperature of the working environment of the rotary kiln, the spare parts are usually made of refractory materials or special alloys to ensure that they can work stably under high temperatures.
High abrasion resistance: Long time material friction and chemical erosion require spare parts to have excellent abrasion resistance to prolong service life.
High structural strength: in order to withstand heavy loads and the pressure of continuous operation, the design of spare parts will place special emphasis on structural strength and reliability.
Easy to install and maintain: Considering the need for frequent replacement, many spare parts are designed to be simpler and easier for quick installation and maintenance.
Strong adaptability: different industries have different needs for rotary kilns, so spare parts need to have good versatility and adaptability to meet diverse application conditions.
(Metal Metallurgy Machinery Top ing For Producing Parts Advanced Machines High Quality Arc Metal Industrial Sintering Furnace)
Specifications of Metal Metallurgy Machinery Top ing For Producing Parts Advanced Machines High Quality Arc Metal Industrial Sintering Furnace
The Top Ing Industrial Sintering Heating system is a modern metallurgy machine crafted for producing high-precision steel elements with sophisticated sintering processes. Designed for demanding industrial settings, it incorporates durable building and construction, premium thermal monitoring, and user-friendly controls to ensure consistent manufacturing of high-grade components. Perfect for automotive, aerospace, tooling, and electronic devices sectors, this furnace masters processing steel powders, alloys, and porcelains into dense, sturdy components.
Trick specs consist of a maximum operating temperature of 2000 ° C, attained through high-resistance alloy heating elements for uniform heat distribution. The heater includes a customizable chamber, readily available in standard sizes from 200x200x200mm to 500x500x800mm, accommodating varied production scales. An accuracy PID temperature control system ensures ± 1 ° C precision, while programmable setups allow multi-stage sintering cycles for complex product requirements. The incorporated gas environment system supports inert atmospheres (argon, nitrogen) or vacuum cleaner conditions, critical for oxidation-sensitive products.
Safety mechanisms include automatic over-temperature closure, emergency air conditioning, and real-time pressure monitoring. Built with double-layer stainless-steel and ceramic fiber insulation, the furnace lessens warm loss, enhancing energy effectiveness. A water-cooled jacket ensures quick cooling, decreasing downtime between cycles. Power requirements range from 380V/50Hz to 480V/60Hz, with 20kW to 100kW setups based on chamber dimension.
The Top Ing heater focuses on durability with corrosion-resistant components and marginal upkeep demands. Its straightforward interface consists of a touchscreen for cycle programs, data logging, and remote surveillance via commercial IoT compatibility. Conformity with ISO 9001 and CE requirements assurances dependability and safety and security. By incorporating rapid home heating rates (as much as 20 ° C/min), exact ambience control, and scalable layout, this sintering heater enhances manufacturing effectiveness, reduces energy costs, and guarantees repeatable outcomes for high-volume or specific steel part production.
(Metal Metallurgy Machinery Top ing For Producing Parts Advanced Machines High Quality Arc Metal Industrial Sintering Furnace)
Applications of Metal Metallurgy Machinery Top ing For Producing Parts Advanced Machines High Quality Arc Metal Industrial Sintering Furnace
Steel metallurgy machinery plays a critical role in modern-day commercial manufacturing, specifically in generating high-performance components for advanced devices. Amongst these modern technologies, the Top quality Arc Metal Industrial Sintering Heater attracts attention as an essential device for changing raw metal powders into sturdy, precision-engineered parts. This furnace makes use of sophisticated sintering processes, where heat and stress fuse metal particles without melting them, guaranteeing marginal material waste and improved structural honesty.
The applications of this sintering furnace span sectors calling for robust, high-precision parts. In aerospace, it creates generator blades and engine components that withstand extreme temperatures and tension. Automotive producers rely on it to develop light-weight yet long lasting transmission gears and brake systems, enhancing fuel efficiency and safety and security. The energy market benefits from sintered parts in wind turbines and nuclear reactors, where corrosion resistance and durability are non-negotiable. Electronics industries utilize the heater to fabricate conductive components and warm sinks crucial for gadgets and wiring.
An essential benefit of the Arc Steel Industrial Sintering Furnace is its capacity to process a wide variety of materials, consisting of stainless steel, titanium, tungsten, and progressed alloys. Its high-temperature arc innovation makes certain consistent home heating, exact temperature control, and fast air conditioning cycles, which are vital for attaining constant thickness and mechanical residential or commercial properties in sintered products. The heater’s vacuum cleaner or inert gas ambience protects against oxidation, preserving material purity and surface area top quality.
Created for commercial scalability, this machinery sustains both set and continuous production, meeting demands for high-volume outcome without compromising accuracy. Its energy-efficient procedure minimizes operational expenses, while automated controls minimize human mistake and boost repeatability. Producers also value its modular style, permitting personalization for specific product requirements or part geometries.
In recap, the Premium quality Arc Metal Industrial Sintering Furnace is crucial for generating innovative equipment components that require stamina, precision, and reliability. By making it possible for cost-efficient, lasting production with minimal material waste, it drives innovation across markets, from aerospace to renewable energy, sealing its role as a keystone of contemporary metallurgical engineering.
Company Introduction
Established in 2001, plant Machinery Equipment Co.,ltd. focus on metal research and mining machinery spare parts. 2 factories over an area of 13,300 square meters, based on 100+ sets of equipment, our production capacity reaches 12000 Tons/Year. has passed ISO 9001 quality managment system certification in 2008.
Our mainly products are dragline excavator spare parts,rotary kiln spare parts, large modulus gear (gear shaft), gearbox ect. 40+ patents with over 45 years experience to help focus on improve the service life of spare parts. We belive that more than 80% reason of mechanical parts’ working life depends on hot processing (steel making/forging/casting/welding/heat treatment). Eight material engineers will control the quality from the original resource.
If you are interested, please feel free to contact us.
Payment
L/C, T/T, Western Union, Paypal, Credit Card etc.
Shipment
By sea, by air, by express, as customers request.
5 FAQs of Metal Metallurgy Machinery Top ing For Producing Parts Advanced Machines High Quality Arc Metal Industrial Sintering Furnace
What is an Arc Metal Industrial Sintering Furnace? An Arc Metal Industrial Sintering Furnace is a high-temperature machine designed for sintering metal or ceramic powders into dense, durable components. It uses controlled heat and atmospheric conditions to bond particles without melting them, making it ideal for producing complex parts with precise mechanical properties. This furnace is commonly used in industries like automotive, aerospace, and tool manufacturing for creating high-performance components.
How does the sintering furnace work in producing metal parts? The furnace heats compacted metal or ceramic powder to a temperature just below its melting point in a controlled environment. This process causes particles to bond at the atomic level, forming a solid structure with minimal porosity. Advanced models use electric arcs or induction heating for rapid, uniform temperature distribution, ensuring consistent part quality. The result is a strong, wear-resistant component with tailored mechanical characteristics.
What are the key advantages of using this furnace? Key benefits include high energy efficiency, precise temperature control, and the ability to process a wide range of materials, including refractory metals. It produces parts with superior density, strength, and dimensional accuracy compared to conventional methods. The furnace’s advanced automation reduces labor costs, while its robust construction ensures long-term reliability in industrial settings.
What safety features are included? Modern sintering furnaces integrate multiple safety systems, such as automatic shutdown during overheating, gas leakage detectors, and emergency cooling mechanisms. Insulated chambers, pressure relief valves, and real-time monitoring via sensors prevent operational hazards. Safety interlocks ensure the furnace only operates when conditions are stable, protecting both operators and equipment.
How to maintain the furnace for optimal performance? Regular maintenance includes cleaning the chamber to remove residue, inspecting heating elements and thermocouples for wear, and checking gas or vacuum seals for leaks. Lubricate moving parts, calibrate temperature controls periodically, and replace worn components as needed. Follow the manufacturer’s guidelines for atmosphere gas purity and thermal cycling to extend the furnace’s lifespan. Training staff on proper usage and maintenance protocols is also critical.
(Metal Metallurgy Machinery Top ing For Producing Parts Advanced Machines High Quality Arc Metal Industrial Sintering Furnace)
REQUEST A QUOTE
RELATED PRODUCTS
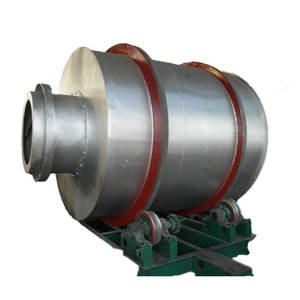
China top Rotary kiln /Rotary kiln incinerator
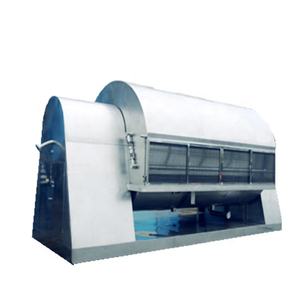
Rotary Kiln Spare Parts Steel 35 kiln tyre Large Casting Steel Kiln Riding Ring
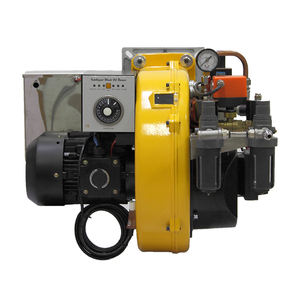
China Factory boiler air nozzle Boiler accessories Thermal power plant boiler air nozzle
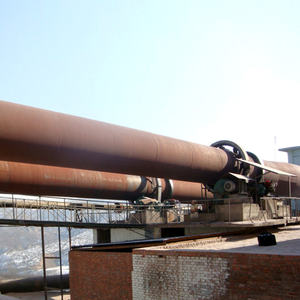
Large cement plant mill head rotary kiln spare parts welding ball mill welding drum
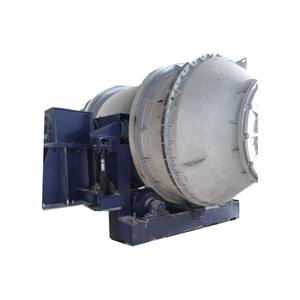
600 Tons Per Day Rotary Kiln/Calcining Kiln for Oil, Gas, and Coal Burning
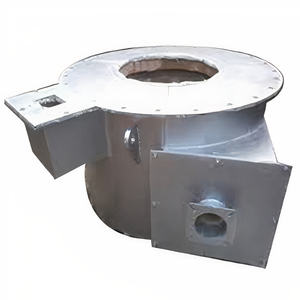