PRODUCT PARAMETERS
Description
Introduction of Industrial Metal Melting Furnace Arc Top ing Equipment Machine For Producing Parts By Powder Metallurgy Met
A rotary kiln is a kind of industrial equipment used for material heating and processing, which is widely used in cement, metallurgy, chemical industry, etc. Industrial Metal Melting Furnace Arc Top ing Equipment Machine For Producing Parts By Powder Metallurgy Met refers to various parts and components which are necessary for maintaining and repairing the normal operation of the rotary kiln, such as cylinder, baffle wheel, pallet, sealing device and so on.
Features and advantages of Industrial Metal Melting Furnace Arc Top ing Equipment Machine For Producing Parts By Powder Metallurgy Met
High-temperature resistance: Due to the extremely high temperature of the working environment of the rotary kiln, the spare parts are usually made of refractory materials or special alloys to ensure that they can work stably under high temperatures.
High abrasion resistance: Long time material friction and chemical erosion require spare parts to have excellent abrasion resistance to prolong service life.
High structural strength: in order to withstand heavy loads and the pressure of continuous operation, the design of spare parts will place special emphasis on structural strength and reliability.
Easy to install and maintain: Considering the need for frequent replacement, many spare parts are designed to be simpler and easier for quick installation and maintenance.
Strong adaptability: different industries have different needs for rotary kilns, so spare parts need to have good versatility and adaptability to meet diverse application conditions.
(Industrial Metal Melting Furnace Arc Top ing Equipment Machine For Producing Parts By Powder Metallurgy Met)
Specifications of Industrial Metal Melting Furnace Arc Top ing Equipment Machine For Producing Parts By Powder Metallurgy Met
The Industrial Steel Melting Furnace Arc Top-Loading Equipment Machine is created for high-efficiency melting and handling of steels in powder metallurgy applications. This devices is engineered to deal with a variety of steels, consisting of steel, titanium, copper, and specialized alloys, making certain exact temperature control and consistent melting for producing premium steel components. The heating system runs making use of an electrical arc system, delivering fast heating and energy-efficient efficiency. Key specifications consist of a power input variety of 380– 440V AIR CONDITIONING (three-phase) with a regularity of 50/60 Hz, making certain compatibility with commercial power grids. The melting ability varies between 500 kg to 5 lots per batch, relying on the design, with a maximum temperature level ranking of 1800 ° C to 3000 ° C to accommodate diverse metal melting points. The furnace includes a top-loading style with a water-cooled crucible made from high-purity graphite or refractory products, boosting resilience and thermal resistance. Advanced insulation using ceramic fiber or carbon composite cellular linings reduces heat loss and boosts energy effectiveness. The system incorporates a PLC-based control board for automated operation, enabling exact changes to arc size, temperature, and melting time. Real-time tracking via touchscreen user interfaces and data logging makes certain process uniformity and quality assurance. Safety and security systems consist of overcurrent protection, emergency closure, and water-cooling failure alarms. The furnace is furnished with a fume removal system to handle emissions and maintain a safe work space. Measurements vary from 3m x 2m x 2.5 m for portable designs to 6m x 4m x 4m for larger devices, with a weight of 5– 20 tons depending upon setup. Optional functions include vacuum melting capabilities, inert gas environments (argon or nitrogen), and robotic charging systems for automation. Compliance with ISO 9001, CE, and RoHS standards warranties dependability and ecological safety and security. Perfect for aerospace, vehicle, and tooling sectors, this furnace guarantees high-purity steel outputs with minimal oxidation, sustaining sophisticated powder metallurgy procedures such as sintering, warm isostatic pressing (HIP), and additive manufacturing. Maintenance needs are low because of tough building and modular parts, making sure long-term operational effectiveness.
(Industrial Metal Melting Furnace Arc Top ing Equipment Machine For Producing Parts By Powder Metallurgy Met)
Applications of Industrial Metal Melting Furnace Arc Top ing Equipment Machine For Producing Parts By Powder Metallurgy Met
Industrial Steel Melting Furnace Arc Top Devices Machines are crucial in modern-day production, specifically in generating high-performance parts by means of powder metallurgy. These heaters melt metals at extreme temperature levels to create exact alloys or steel powders, which are then compacted and sintered right into intricate parts. Their applications extend sectors requiring resilient, lightweight, and elaborately designed parts with marginal product waste.
In the automobile sector, these heating systems produce metal powders for equipments, bearings, and engine parts. The heater’s capability to melt steel, iron, or specialized alloys makes sure powders have uniform structure, enhancing part stamina and wear resistance. Similarly, aerospace relies on these systems to develop heat-resistant superalloys and titanium powders for generator blades, architectural components, and landing equipment, where precision and product honesty are non-negotiable.
Electronic devices manufacturing take advantage of the heater’s capability to process conductive metals like copper and silver, producing powders for adapters, warm sinks, and magnetic parts. The medical area makes use of biocompatible steels such as stainless-steel and cobalt-chromium, merged powders for surgical tools, dental implants, and joint substitutes, conference stringent health and resilience standards.
Industrial machinery industries use these heating systems to create tungsten or molybdenum powders for cutting devices and durable machinery parts, leveraging their high melting factors and put on resistance. In addition, the heating systems support lasting methods by recycling steel scrap into top notch powders, minimizing resources costs and ecological effect.
Secret advantages of Arc Top furnaces consist of energy efficiency, exact temperature control, and quick melting cycles, which enhance powder manufacturing. Their convenience in taking care of diverse metals– from common alloys to unique composites– guarantees consistent particle dimension and purity, crucial for sintering processes. By allowing cost-efficient, large-scale powder manufacturing with minimal waste, these systems are indispensable beforehand powder metallurgy, driving advancement throughout sectors that demand precision, dependability, and product efficiency.
Company Introduction
Established in 2001, plant Machinery Equipment Co.,ltd. focus on metal research and mining machinery spare parts. 2 factories over an area of 13,300 square meters, based on 100+ sets of equipment, our production capacity reaches 12000 Tons/Year. has passed ISO 9001 quality managment system certification in 2008.
Our mainly products are dragline excavator spare parts,rotary kiln spare parts, large modulus gear (gear shaft), gearbox ect. 40+ patents with over 45 years experience to help focus on improve the service life of spare parts. We belive that more than 80% reason of mechanical parts’ working life depends on hot processing (steel making/forging/casting/welding/heat treatment). Eight material engineers will control the quality from the original resource.
If you are interested, please feel free to contact us.
Payment
L/C, T/T, Western Union, Paypal, Credit Card etc.
Shipment
By sea, by air, by express, as customers request.
5 FAQs of Industrial Metal Melting Furnace Arc Top ing Equipment Machine For Producing Parts By Powder Metallurgy Met
**What is an industrial arc melting furnace, and how is it used in powder metallurgy?**
An industrial arc melting furnace uses high-voltage electric arcs to generate extreme heat (up to 3,000°C or higher) to melt metals. In powder metallurgy, it melts raw or scrap metals into liquid form, which is then atomized into fine powders. These powders are later pressed and sintered to create high-strength, precision components like gears or automotive parts.
**Which metals can be processed with this equipment?**
Arc melting furnaces handle refractory and high-melting-point metals, including stainless steel, titanium, tungsten, nickel-based superalloys, and specialty alloys. They’re ideal for metals requiring ultra-high purity or precise compositional control, commonly used in aerospace, medical devices, and energy sectors.
**What are the advantages of arc furnaces over other melting methods?**
Arc furnaces offer rapid heating, energy efficiency for large-scale operations, and superior temperature control, ensuring consistent molten metal quality. They produce less contamination compared to gas-fired furnaces and are adaptable for recycling scrap metals. Their ability to reach extreme temperatures makes them unmatched for processing refractory metals.
**What safety features are integrated into these furnaces?**
Key safety systems include water-cooled panels to prevent overheating, emergency arc shutdown mechanisms, insulated casings to contain heat/sparks, and automated pressure relief valves. Advanced models include real-time temperature monitoring and fault detection to minimize risks of electrical hazards or molten metal leaks.
**What maintenance ensures optimal furnace performance?**
Regular maintenance includes inspecting and replacing worn electrodes, cleaning slag buildup, checking cooling systems for leaks, and calibrating temperature sensors. Lubricating moving parts and updating control software are also critical. Annual professional inspections help identify wear in linings or electrical components, ensuring longevity and efficiency.
(Industrial Metal Melting Furnace Arc Top ing Equipment Machine For Producing Parts By Powder Metallurgy Met)
REQUEST A QUOTE
RELATED PRODUCTS
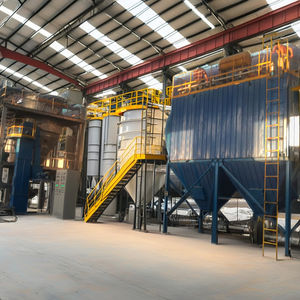
1100 Degree Indirect External Heating Rotary Kiln For Processing Active Carbon Carbonate Catalyst Mineral Powder Caclining
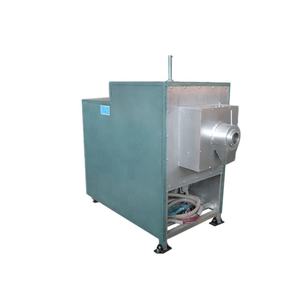
Lab Testing Kiln Small Rotary Kiln for Samples Calcination and Sintering
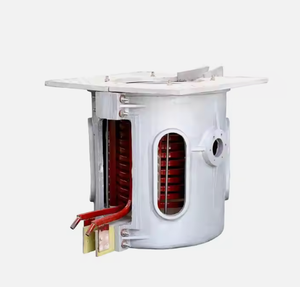
High quality Cement plant rotary kiln replacement parts large module ring gear
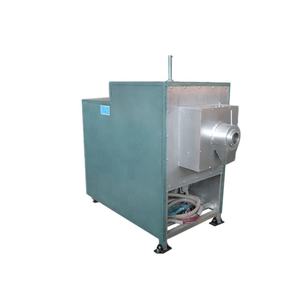
Rotary Kiln Bauxite RKB 83/80/75/70
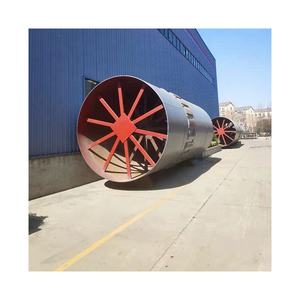
High Temperature Kiln Muffle Oven Lab 1100 1200 1400 1500 1600 1700 1800 Degree Electric Ceramic Box Melting Muffle Furnace
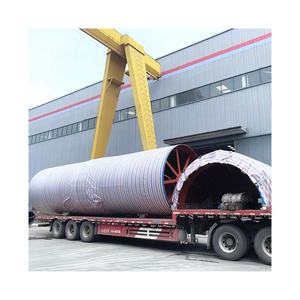