PRODUCT PARAMETERS
Description
Introduction of High temperature rotary tube furnace lithium battery powder sintering furnace rotary kiln non-standard customization
A rotary kiln is a kind of industrial equipment used for material heating and processing, which is widely used in cement, metallurgy, chemical industry, etc. High temperature rotary tube furnace lithium battery powder sintering furnace rotary kiln non-standard customization refers to various parts and components which are necessary for maintaining and repairing the normal operation of the rotary kiln, such as cylinder, baffle wheel, pallet, sealing device and so on.
Features and advantages of High temperature rotary tube furnace lithium battery powder sintering furnace rotary kiln non-standard customization
High-temperature resistance: Due to the extremely high temperature of the working environment of the rotary kiln, the spare parts are usually made of refractory materials or special alloys to ensure that they can work stably under high temperatures.
High abrasion resistance: Long time material friction and chemical erosion require spare parts to have excellent abrasion resistance to prolong service life.
High structural strength: in order to withstand heavy loads and the pressure of continuous operation, the design of spare parts will place special emphasis on structural strength and reliability.
Easy to install and maintain: Considering the need for frequent replacement, many spare parts are designed to be simpler and easier for quick installation and maintenance.
Strong adaptability: different industries have different needs for rotary kilns, so spare parts need to have good versatility and adaptability to meet diverse application conditions.
(High temperature rotary tube furnace lithium battery powder sintering furnace rotary kiln non-standard customization)
Specifications of High temperature rotary tube furnace lithium battery powder sintering furnace rotary kiln non-standard customization
The high-temperature rotary tube furnace is designed for sintering lithium battery powder. It handles non-standard customization to meet specific industrial needs. The furnace operates at temperatures up to 1700°C. It ensures precise thermal processing for materials like cathode or anode powders. The rotary kiln structure uses a cylindrical tube made of high-purity alumina or quartz. The tube rotates continuously to guarantee uniform heating. This prevents material agglomeration during sintering. The rotation speed adjusts between 1-10 RPM. Users control it via a digital interface for consistency. Heating elements are silicon carbide or molybdenum disilicide. These materials provide rapid heat-up rates. They maintain stable temperatures even under prolonged operation. The furnace chamber is insulated with ceramic fiber. This minimizes heat loss. It improves energy efficiency. The system supports multiple gas atmospheres. Options include nitrogen, argon, or hydrogen. Gas flow rates are adjustable through mass flow controllers. This ensures optimal sintering conditions for different battery materials. Temperature uniformity is within ±5°C across the heating zone. A programmable logic controller manages all parameters. Users set temperature profiles, rotation speeds, and gas settings via a touchscreen. Data logging features record process details for quality control. Safety mechanisms include over-temperature alarms, automatic power cutoff, and gas leakage detectors. The furnace structure uses stainless steel for durability. Custom tube diameters and lengths are available. Common sizes range from 80mm to 300mm in diameter. Heating zone lengths vary from 500mm to 2000mm. Electrical requirements depend on furnace size. Standard models use 220V or 380V power supplies. Installation includes optional cooling systems. Water or air cooling prevents external overheating. The design accommodates batch or continuous processing. Feed and discharge ports are customizable for automated integration. Maintenance involves periodic inspection of heating elements and tube integrity. Spare parts are replaceable without dismantling the entire system. Technical support covers installation, calibration, and troubleshooting. The furnace suits research labs and production facilities. It meets strict requirements for lithium-ion battery material synthesis.
(High temperature rotary tube furnace lithium battery powder sintering furnace rotary kiln non-standard customization)
Applications of High temperature rotary tube furnace lithium battery powder sintering furnace rotary kiln non-standard customization
High-temperature rotary tube furnaces serve critical roles in advanced manufacturing processes. These systems handle lithium battery powder sintering with precision. The furnace heats materials to extreme temperatures. This creates uniform thermal environments necessary for producing high-performance battery components. Cathode and anode materials undergo controlled sintering here. The process enhances their electrochemical properties. Consistency in particle structure improves battery efficiency and lifespan.
Rotary kiln designs in these furnaces enable continuous processing. Materials rotate inside a cylindrical chamber. Heat distribution remains even throughout. This prevents hotspots and ensures product quality. Customization options allow adaptation to specific industrial needs. Non-standard designs accommodate unique material types or production scales. Adjustments include chamber dimensions, heating zones, and gas atmospheres. Nitrogen or argon environments prevent oxidation during sintering.
These furnaces support multiple industries beyond lithium batteries. Ceramic processing, metal alloy treatment, and catalyst preparation benefit from similar setups. The flexibility of non-standard designs makes them versatile. Users modify temperature ranges, rotation speeds, and cooling rates. Automation features integrate with existing production lines. PLC systems monitor and adjust parameters in real time. This reduces manual intervention and human error.
Durability is a key focus. High-grade refractory materials line the chamber. Heating elements resist degradation under extreme conditions. Thermal insulation minimizes energy loss. Maintenance requirements stay low despite continuous operation. Safety mechanisms protect against over-temperature or gas leaks.
Custom orders involve collaboration between engineers and clients. Technical specifications align with production goals. Testing phases verify performance before full-scale deployment. The result is a tailored solution matching exact operational demands. Scalability ensures small labs and large factories both find suitable configurations.
Energy efficiency remains a priority. Advanced heating technology reduces power consumption. Heat recovery systems reuse waste energy. Operational costs decrease without sacrificing output quality. Rapid heating and cooling cycles shorten production times. This boosts overall throughput.
High-temperature rotary tube furnaces address complex material processing challenges. Their adaptability and reliability make them indispensable in modern manufacturing. Custom-built solutions push the boundaries of material science and industrial efficiency.
Company Introduction
Established in 2001, plant Machinery Equipment Co.,ltd. focus on metal research and mining machinery spare parts. 2 factories over an area of 13,300 square meters, based on 100+ sets of equipment, our production capacity reaches 12000 Tons/Year. has passed ISO 9001 quality managment system certification in 2008.
Our mainly products are dragline excavator spare parts,rotary kiln spare parts, large modulus gear (gear shaft), gearbox ect. 40+ patents with over 45 years experience to help focus on improve the service life of spare parts. We belive that more than 80% reason of mechanical parts’ working life depends on hot processing (steel making/forging/casting/welding/heat treatment). Eight material engineers will control the quality from the original resource.
If you are interested, please feel free to contact us.
Payment
L/C, T/T, Western Union, Paypal, Credit Card etc.
Shipment
By sea, by air, by express, as customers request.
5 FAQs of High temperature rotary tube furnace lithium battery powder sintering furnace rotary kiln non-standard customization
What is a high-temperature rotary tube furnace for lithium battery powder sintering? This furnace heats materials to extreme temperatures in a controlled rotating chamber. It processes lithium battery powders like cathode and anode materials. The rotation ensures even heat distribution. This improves material consistency and performance.
Can the furnace be customized for specific needs? Yes. Customization options include size adjustments, heating element types, gas atmosphere controls, and cooling systems. Modifications align with production volume, material properties, or space constraints. Non-standard designs require detailed client input. Engineers then develop tailored solutions.
What temperature range does the furnace achieve? Standard models reach 1700°C. Higher temperatures are possible with advanced heating elements or insulation upgrades. Precise temperature control ensures optimal sintering. This prevents material degradation. Uniform heating avoids hotspots that damage powders.
What safety features are included? Systems include automatic shut-off for overheating, gas leakage detectors, and emergency cooling. Thermal sensors monitor real-time conditions. Alarms trigger if parameters exceed limits. Protective casings reduce external heat exposure. Safety protocols protect operators and equipment.
How long does delivery take after ordering? Lead time depends on customization complexity. Standard units ship in 4-6 weeks. Custom designs may take 8-12 weeks. Clients must share specifications early. Engineers confirm feasibility before production starts. Delays happen if design changes occur mid-process.
(High temperature rotary tube furnace lithium battery powder sintering furnace rotary kiln non-standard customization)
REQUEST A QUOTE
RELATED PRODUCTS
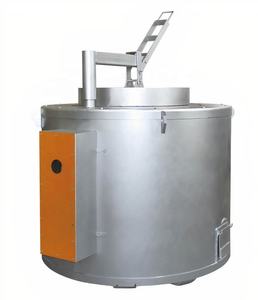
Four Channel Cement Rotary Kiln Industry Double Swirl Rotary Kiln Burner Double Swirl Rotary Kiln Burner For Cement Production
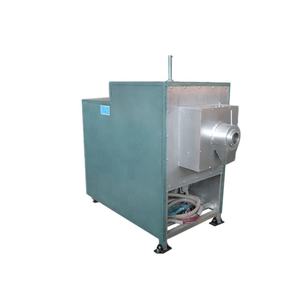
Lab Testing Kiln Small Rotary Kiln for Samples Calcination and Sintering
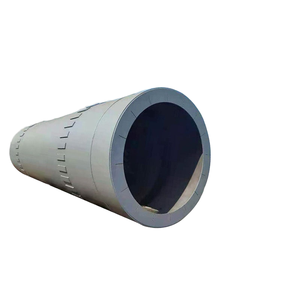
Custom Cast Steel Cement Plant Rotary Kiln Parts Riding Ring Tyre
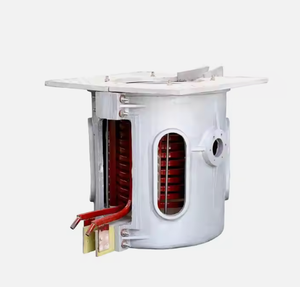
High Quality Large Cement Plant Rotary Kiln Parts Large Diameter Gear Ring
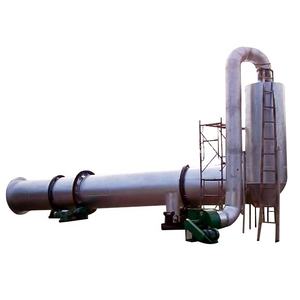
Motorcycle spare parts rubber damper GN125 GS125 motorcycle accessories para motos in china with high quality
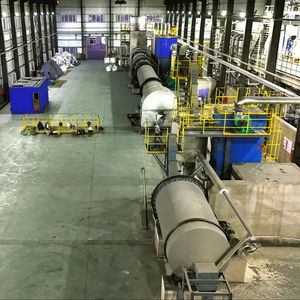