PRODUCT PARAMETERS
Description
Introduction of High Temperature Laboratory Rotary Kiln Tilting Rotating Sintering Tube Furnace Rotary Furnace For Processing Activated Carbon
A rotary kiln is a kind of industrial equipment used for material heating and processing, which is widely used in cement, metallurgy, chemical industry, etc. High Temperature Laboratory Rotary Kiln Tilting Rotating Sintering Tube Furnace Rotary Furnace For Processing Activated Carbon refers to various parts and components which are necessary for maintaining and repairing the normal operation of the rotary kiln, such as cylinder, baffle wheel, pallet, sealing device and so on.
Features and advantages of High Temperature Laboratory Rotary Kiln Tilting Rotating Sintering Tube Furnace Rotary Furnace For Processing Activated Carbon
High-temperature resistance: Due to the extremely high temperature of the working environment of the rotary kiln, the spare parts are usually made of refractory materials or special alloys to ensure that they can work stably under high temperatures.
High abrasion resistance: Long time material friction and chemical erosion require spare parts to have excellent abrasion resistance to prolong service life.
High structural strength: in order to withstand heavy loads and the pressure of continuous operation, the design of spare parts will place special emphasis on structural strength and reliability.
Easy to install and maintain: Considering the need for frequent replacement, many spare parts are designed to be simpler and easier for quick installation and maintenance.
Strong adaptability: different industries have different needs for rotary kilns, so spare parts need to have good versatility and adaptability to meet diverse application conditions.
(High Temperature Laboratory Rotary Kiln Tilting Rotating Sintering Tube Furnace Rotary Furnace For Processing Activated Carbon)
Specifications of High Temperature Laboratory Rotary Kiln Tilting Rotating Sintering Tube Furnace Rotary Furnace For Processing Activated Carbon
The High Temperature Research Laboratory Rotating Kiln Tilting Rotating Sintering Tube Heater is crafted for advanced thermal handling applications, including the manufacturing and activation of carbon products. Developed to withstand extreme temperatures, this furnace guarantees specific control, toughness, and effectiveness for commercial and research study use. Below are the vital specifications:
** Temperature level Range **: The heater operates at an optimum temperature level of 1700 ° C, ideal for sintering, calcination, and pyrolysis processes. Consistent home heating is accomplished using a multi-zone control system, with temperature level precision of ± 1 ° C. ** Heating Elements **: Furnished with high-grade silicon carbide (SiC) or molybdenum disilicide (MoSi2) burner, ensuring fast heat-up prices and resistance to oxidation at heats.
** Rotary System **: The heating system features a tilting and turning tube design with flexible rotation rate (1-10 RPM) and tilt angle (0-45 °), allowing homogeneous material mixing and managed discharge. The turning is driven by a robust motor with variable frequency control for smooth procedure.
** Tube Dimensions **: Customizable tube diameters (80-200 mm) and sizes (1000-3000 mm), crafted from high-purity alumina ceramic or refractory alloys to stand up to thermal stress and harsh settings.
** Atmosphere Control **: Supports inert (N2, Ar) or reactive gas environments, with gas flow regulators and impermeable seals. Optional vacuum cleaner compatibility for specialized procedures.
** Power Supply **: Offered in 220V or 380V setups, with power ratings varying from 12 kW to 45 kW depending on model dimension.
** Control System **: Advanced PID temperature controller with touchscreen user interface, programmable heating/cooling curves (approximately 30 sectors), and real-time information logging. RS-485/ USB connectivity for remote monitoring.
** Safety Features **: Over-temperature defense, auto-shutdown mechanisms, and emergency situation air conditioning systems. Shielded double-layer housing reduces outside warm radiation.
** Applications **: Activated carbon handling, stimulant synthesis, ceramic sintering, metallurgical testing, and chemical vapor deposition (CVD).
** Cooling System **: Optional water-cooling or forced-air cooling for fast quenching and extended furnace life.
** Construction **: Stainless steel frame with refractory block insulation and ceramic fiber modules for energy performance.
** Accessories **: Includes crucible sets, sample push rods, thermocouples (Kind S, B, or K), and gas flow meters.
** Guarantee & Assistance **: 1-2 years warranty, with technological aid and spare components availability.
This rotary kiln heater combines accuracy design with durable building and construction, making it a trusted solution for high-temperature material handling in research laboratories and pilot-scale production.
(High Temperature Laboratory Rotary Kiln Tilting Rotating Sintering Tube Furnace Rotary Furnace For Processing Activated Carbon)
Applications of High Temperature Laboratory Rotary Kiln Tilting Rotating Sintering Tube Furnace Rotary Furnace For Processing Activated Carbon
The High Temperature Laboratory Rotary Kiln Tilting Rotating Sintering Tube Heater is a flexible, precision-engineered system designed for sophisticated thermal handling applications, especially in the production and optimization of turned on carbon. This furnace incorporates high-temperature capacities (typically approximately 1700 ° C or higher) with a rotating drum and tilting mechanism, making sure uniform warm circulation, reliable material blending, and seamless discharge. Its robust construction enables controlled handling in inert, oxidizing, or lowering environments, making it ideal for laboratory-scale research study, process advancement, and small-batch production.
In turned on carbon handling, the rotary heating system plays a crucial function in both carbonization and activation phases. During carbonization, natural forerunners like coconut coverings or wood are warmed in an oxygen-free atmosphere to eliminate unstable components, forming a carbon-rich char. The heater’s turning makes sure also thermal disintegration, lessening hotspots. The subsequent activation stage– either physical (vapor or carbon dioxide) or chemical (utilizing representatives like KOH)– relies on the heater’s precise temperature level control to develop an extremely porous structure. The turning feature simplifies sample handling, enabling quick transfer of products in between phases or post-process analysis.
Beyond turned on carbon, this heater supports sintering, calcination, and pyrolysis of ceramics, catalysts, and metal oxides. Its programmable temperature level profiles and adjustable rotation rates allow scientists to enhance specifications for material thickness, surface, and reactivity. For instance, in stimulant synthesis, uniform heat therapy makes sure consistent energetic website distribution, while in environmental applications, it assists in creating adsorbents for toxin elimination.
Key benefits consist of scalability from lab to pilot-scale production, energy-efficient insulation, and compatibility with real-time tracking systems. The combination of electronic controls improves reproducibility, essential for R&D. By making it possible for accurate manipulation of thermal and mechanical variables, this rotating heater increases advancement in materials science, environmental engineering, and industrial chemistry, serving as a foundation device for progressing high-temperature procedures.
Company Introduction
Established in 2001, plant Machinery Equipment Co.,ltd. focus on metal research and mining machinery spare parts. 2 factories over an area of 13,300 square meters, based on 100+ sets of equipment, our production capacity reaches 12000 Tons/Year. has passed ISO 9001 quality managment system certification in 2008.
Our mainly products are dragline excavator spare parts,rotary kiln spare parts, large modulus gear (gear shaft), gearbox ect. 40+ patents with over 45 years experience to help focus on improve the service life of spare parts. We belive that more than 80% reason of mechanical parts’ working life depends on hot processing (steel making/forging/casting/welding/heat treatment). Eight material engineers will control the quality from the original resource.
If you are interested, please feel free to contact us.
Payment
L/C, T/T, Western Union, Paypal, Credit Card etc.
Shipment
By sea, by air, by express, as customers request.
5 FAQs of High Temperature Laboratory Rotary Kiln Tilting Rotating Sintering Tube Furnace Rotary Furnace For Processing Activated Carbon
What is the maximum temperature range of this rotary kiln furnace, and is it adjustable?
The High Temperature Laboratory Rotary Kiln Furnace operates within a temperature range of up to 1700°C, making it ideal for high-heat processes like sintering, calcination, and activation of carbon. The temperature is fully adjustable via a digital PID controller, allowing precise customization for different materials or stages of processing. This ensures optimal thermal conditions for activating carbon while maintaining energy efficiency.
How does the tilting and rotating mechanism improve activated carbon processing?
The tilting feature allows the furnace tube to be angled between 0° and 90°, enabling controlled discharge of processed materials without manual intervention. The 360° rotating function ensures uniform heat distribution and consistent exposure of raw carbon to high temperatures, minimizing hotspots and enhancing product homogeneity. This dual motion also accelerates reaction rates, reduces processing time, and improves yield in carbon activation.
What safety features are included to handle high-temperature operations?
The furnace is equipped with over-temperature protection, automatic power-off in case of system faults, and reinforced insulation to prevent external overheating. A robust cooling system manages heat dissipation, while safety interlocks restrict access during operation. Additionally, the furnace structure is made of heat-resistant alloys and ceramics to withstand prolonged high-temperature use, ensuring operator safety and equipment durability.
Can this furnace handle different atmospheres for specialized carbon activation?
Yes, the rotary kiln supports inert (e.g., nitrogen, argon) or reactive (e.g., oxygen, steam) atmospheres, critical for tailoring activated carbon’s porosity and surface area. Gas flow rates are adjustable via integrated valves, and the sealed tube design prevents leaks. This flexibility ensures compatibility with chemical vapor deposition (CVD) or pyrolysis processes required for advanced carbon modification.
What maintenance is required to ensure long-term performance?
Regular maintenance includes cleaning residual carbon deposits from the tube, inspecting heating elements for wear, and lubricating rotating parts to prevent friction. The furnace’s modular design allows easy replacement of components like thermocouples or seals. Users should perform monthly calibration of temperature sensors and ensure proper ventilation to avoid particulate buildup, extending the furnace’s lifespan and maintaining precision.
(High Temperature Laboratory Rotary Kiln Tilting Rotating Sintering Tube Furnace Rotary Furnace For Processing Activated Carbon)
REQUEST A QUOTE
RELATED PRODUCTS
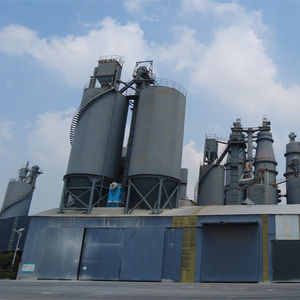
Rotary Kiln For lime, Cement Making Machinery Production Line Spare parts, Support Roller Quick Lime Rotary Kiln
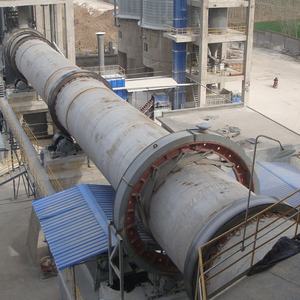
Citic Rotary kiln spare parts Rotary kiln forging supporting wheel
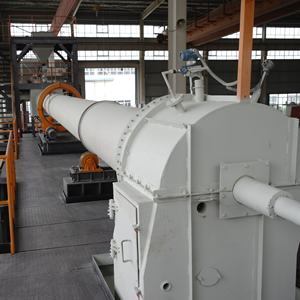
OEM Steel Rotary Kiln Support Roller Shaft
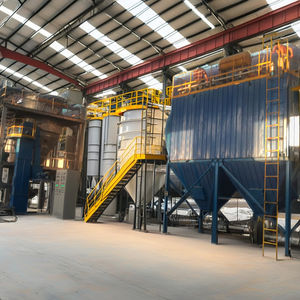
1100 Degree Indirect External Heating Rotary Kiln For Processing Active Carbon Carbonate Catalyst Mineral Powder Caclining
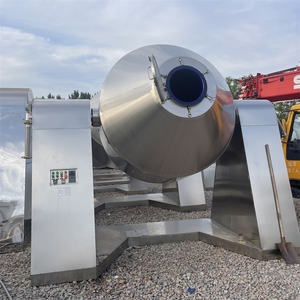
OEM good quality Cement kiln spare parts shell of rotary kiln with different parameter /Rotary kiln Shell made to order
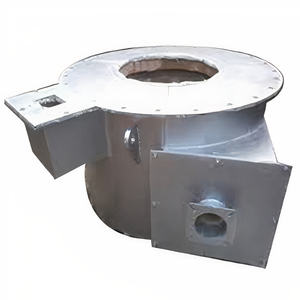