PRODUCT PARAMETERS
Description
Introduction of Design and manufacture environmental protection equipment rotary kiln incinerator equipment
A rotary kiln is a kind of industrial equipment used for material heating and processing, which is widely used in cement, metallurgy, chemical industry, etc. Design and manufacture environmental protection equipment rotary kiln incinerator equipment refers to various parts and components which are necessary for maintaining and repairing the normal operation of the rotary kiln, such as cylinder, baffle wheel, pallet, sealing device and so on.
Features and advantages of Design and manufacture environmental protection equipment rotary kiln incinerator equipment
High-temperature resistance: Due to the extremely high temperature of the working environment of the rotary kiln, the spare parts are usually made of refractory materials or special alloys to ensure that they can work stably under high temperatures.
High abrasion resistance: Long time material friction and chemical erosion require spare parts to have excellent abrasion resistance to prolong service life.
High structural strength: in order to withstand heavy loads and the pressure of continuous operation, the design of spare parts will place special emphasis on structural strength and reliability.
Easy to install and maintain: Considering the need for frequent replacement, many spare parts are designed to be simpler and easier for quick installation and maintenance.
Strong adaptability: different industries have different needs for rotary kilns, so spare parts need to have good versatility and adaptability to meet diverse application conditions.
(Design and manufacture environmental protection equipment rotary kiln incinerator equipment)
Specifications of Design and manufacture environmental protection equipment rotary kiln incinerator equipment
The rotating kiln incinerator is a high-efficiency environmental protection tools designed for risk-free and certified disposal of hazardous, clinical, industrial, and community solid waste. Its durable construction and advanced engineering make certain optimum burning, minimal discharges, and compliance with international environmental criteria.
** Layout Specifications **:.
– ** Framework **: The system makes up a key rotating kiln chamber and a secondary burning chamber. The rotating kiln is a cylindrical, refractory-lined steel covering tilted at a minor angle, revolving at 0.5– 5 RPM to make sure continual waste motion.
– ** Material **: State-of-the-art stainless-steel and refractory products (alumina, silica, or chrome-based linings) stand up to temperature levels approximately 1,300 ° C( 2,372 ° F) in the main chamber and 1,600 ° C( 2,912 ° F) in the secondary chamber. -** Thermal Capacity **: Customizable for waste throughputs varying from 50 kg/hr to 20,000 kg/hr, depending upon application.
– ** Temperature Control **: Precision heaters and automated temperature level sensing units preserve burning security. Primary chamber runs at 800– 1,000 ° C( 1,472– 1,832 ° F), while the secondary chamber ensures complete oxidation at 1,100– 1,300 ° C( 2,012– 2,372 ° F).
– ** House Time **: Adjustable rotational rate makes certain waste continues to be in the kiln for 30– 90 minutes, guaranteeing complete burnout.
** Manufacturing and Operational Features **:.
– ** Exhaust Control **: Integrated air contamination control systems include satiate towers, cyclones, scrubbers (wet/dry), turned on carbon shot, and baghouse filters to reduce the effects of acidic gases (SOx, NOx, HCl), particulates, and dioxins.
– ** Automation **: PLC-based control systems allow real-time monitoring of temperature, stress, oxygen levels, and emissions. Remote procedure and information logging make certain conformity with EPA, EU Directive 2000/76/EC, and various other guidelines.
– ** Safety **: Explosion-proof layout, emergency situation closure devices, and gas leakage discovery systems enhance operational safety.
– ** Energy Healing **: Optional waste heat central heating boilers or warm exchangers recuperate power for steam/power generation, boosting sustainability.
– ** Longevity **: Corrosion-resistant components and modular layout minimize maintenance downtime. Access ports and evaluation factors facilitate simple maintenance.
** Applications **: Suitable for contaminated materials treatment plants, medical facilities, chemical markets, and metropolitan waste administration. The rotating kiln burner ensures 99.9% damage performance of natural pollutants, conference stringent ecological standards while prioritizing power effectiveness and operational integrity. Certifications include ISO 14001, CE, and ASME compliance. Custom-made arrangements are offered to address particular waste compositions and regulatory demands.
(Design and manufacture environmental protection equipment rotary kiln incinerator equipment)
Applications of Design and manufacture environmental protection equipment rotary kiln incinerator equipment
Rotary kiln burner devices represents an important advancement in environmental management innovation, created to resolve the expanding difficulties of waste administration and air pollution control. This equipment is crafted to thermally treat a wide range of waste materials, making certain safe disposal while reducing ecological effect. Its durable style and functional performance make it a keystone option for industries, communities, and medical care sectors making every effort to satisfy rigorous environmental regulations.
A key application of rotary kiln burners is the disposal of hazardous waste, including chemical by-products, contaminated dirts, and industrial deposits. The high-temperature combustion procedure (typically between 850 ° C and 1,200 ° C)makes certain total failure of hazardous materials, reducing unsafe exhausts. Likewise, clinical centers rely on these systems to securely ruin contagious waste, pharmaceuticals, and biohazard products, reducing public health and wellness threats. Municipalities utilize rotating kilns for taking care of metropolitan strong waste (MSW), converting non-recyclable products into power while minimizing landfill dependency. Industrial markets, such as petrochemicals and manufacturing, release this modern technology to process sludge, tars, and other intricate by-products, straightening with circular economy concepts.
The layout of modern-day rotary kiln burners stresses environmental sustainability. A revolving round chamber makes sure uniform warm circulation, enhancing combustion effectiveness and minimizing unburned deposits. Advanced exhaust control systems– such as scrubbers, bag filters, and selective catalytic decrease (SCR) units– capture particulate matter, acidic gases, and dioxins, making certain conformity with international air high quality criteria. Energy recuperation systems transform excess warm into heavy steam or electrical power, enhancing operational cost-effectiveness and reducing carbon footprints.
Longevity and adaptability are trademarks of this devices. Constructed from refractory materials immune to severe temperatures and destructive substances, rotary kilns provide long-term reliability. Their versatility in taking care of diverse waste kinds– solid, fluid, or aeriform– makes them essential for markets focusing on lasting waste services. By integrating sophisticated automation, these systems allow real-time monitoring of burning specifications, guaranteeing ideal efficiency and governing compliance.
In an age of rising environmental awareness, rotating kiln burners stand as an aggressive option for lowering environmental injury while promoting source performance. Their duty in changing waste into energy, curbing pollution, and sustaining governing adherence emphasizes their value in promoting a cleaner, more sustainable future.
Company Introduction
Established in 2001, plant Machinery Equipment Co.,ltd. focus on metal research and mining machinery spare parts. 2 factories over an area of 13,300 square meters, based on 100+ sets of equipment, our production capacity reaches 12000 Tons/Year. has passed ISO 9001 quality managment system certification in 2008.
Our mainly products are dragline excavator spare parts,rotary kiln spare parts, large modulus gear (gear shaft), gearbox ect. 40+ patents with over 45 years experience to help focus on improve the service life of spare parts. We belive that more than 80% reason of mechanical parts’ working life depends on hot processing (steel making/forging/casting/welding/heat treatment). Eight material engineers will control the quality from the original resource.
If you are interested, please feel free to contact us.
Payment
L/C, T/T, Western Union, Paypal, Credit Card etc.
Shipment
By sea, by air, by express, as customers request.
5 FAQs of Design and manufacture environmental protection equipment rotary kiln incinerator equipment
What is a rotary kiln incinerator and how does it work? A rotary kiln incinerator is a thermal treatment system designed to safely dispose of hazardous and non-hazardous waste through high-temperature combustion. The waste is fed into a rotating cylindrical chamber (kiln) inclined to allow gradual movement of materials. Primary combustion occurs at temperatures between 800°C and 1,200°C, breaking down organic compounds. Gases then pass into a secondary chamber for further oxidation, ensuring complete destruction of harmful substances. Ash and residues are collected for safe disposal, while flue gases are treated to meet emission standards.
What types of waste can a rotary kiln incinerator process? These systems handle diverse waste types, including medical, industrial, chemical, and municipal solid waste. They are effective for liquids, sludges, gases, and solids, including toxic, flammable, or corrosive materials. High-temperature operation ensures safe treatment of complex wastes like pharmaceuticals, pesticides, and contaminated soils. The rotary design accommodates varying waste consistencies and calorific values, making it versatile for different industries.
How does the equipment ensure compliance with environmental regulations? Rotary kiln incinerators integrate advanced emission control technologies such as scrubbers, bag filters, and selective catalytic reduction (SCR) systems to neutralize pollutants. Continuous monitoring of flue gases (e.g., dioxins, NOx, SO2, particulate matter) ensures adherence to standards like EPA, EU Directive 2000/76/EC, or regional guidelines. Automated controls optimize combustion efficiency, minimizing carbon footprint and preventing release of untreated emissions.
What maintenance is required for rotary kiln incinerators? Routine maintenance includes inspecting refractory linings, seals, and rotational mechanisms to prevent heat loss or mechanical failure. Burners, fans, and emission control systems require periodic cleaning and calibration. Downtime is minimized through predictive maintenance strategies, with most components designed for durability under high-stress conditions. Annual shutdowns for comprehensive checks ensure long-term reliability and operational safety.
Are rotary kiln incinerators cost-effective for industrial use? While initial investment is higher than simpler incinerators, rotary kilns offer long-term cost savings due to high waste throughput, energy recovery capabilities (e.g., steam or electricity generation), and reduced landfill costs. Their efficiency in treating diverse waste streams lowers regulatory risks and disposal expenses. Businesses also benefit from scalability, with systems tailored to specific waste volumes, ensuring operational flexibility and ROI over time.
(Design and manufacture environmental protection equipment rotary kiln incinerator equipment)
REQUEST A QUOTE
RELATED PRODUCTS
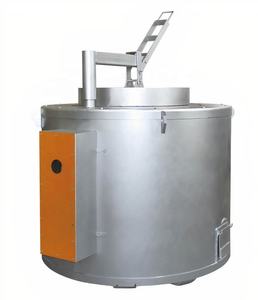
Four Channel Cement Rotary Kiln Industry Double Swirl Rotary Kiln Burner Double Swirl Rotary Kiln Burner For Cement Production
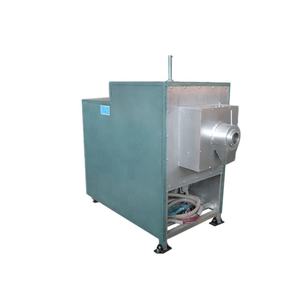
Lime Powder Rotary Drum Kiln Furnace Rotary Limestone Kiln Cement Rotary Kiln for
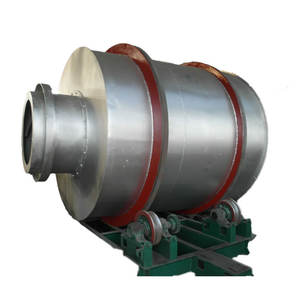
Citic Rotary kiln spare parts Rotary kiln supporting wheel bearing device Rotary kiln
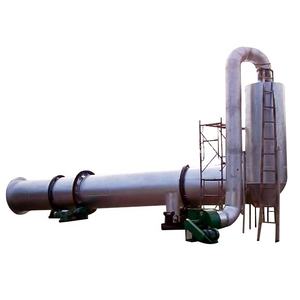
Motorcycle spare parts rubber damper GN125 GS125 motorcycle accessories para motos in china with high quality
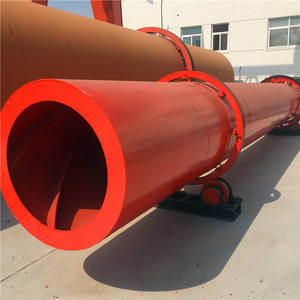