PRODUCT PARAMETERS
Description
Introduction of China factory identification of high quality hot ing unique kiln rotary calcining rotary kiln production line
A rotary kiln is a kind of industrial equipment used for material heating and processing, which is widely used in cement, metallurgy, chemical industry, etc. China factory identification of high quality hot ing unique kiln rotary calcining rotary kiln production line refers to various parts and components which are necessary for maintaining and repairing the normal operation of the rotary kiln, such as cylinder, baffle wheel, pallet, sealing device and so on.
Features and advantages of China factory identification of high quality hot ing unique kiln rotary calcining rotary kiln production line
High-temperature resistance: Due to the extremely high temperature of the working environment of the rotary kiln, the spare parts are usually made of refractory materials or special alloys to ensure that they can work stably under high temperatures.
High abrasion resistance: Long time material friction and chemical erosion require spare parts to have excellent abrasion resistance to prolong service life.
High structural strength: in order to withstand heavy loads and the pressure of continuous operation, the design of spare parts will place special emphasis on structural strength and reliability.
Easy to install and maintain: Considering the need for frequent replacement, many spare parts are designed to be simpler and easier for quick installation and maintenance.
Strong adaptability: different industries have different needs for rotary kilns, so spare parts need to have good versatility and adaptability to meet diverse application conditions.
(China factory identification of high quality hot ing unique kiln rotary calcining rotary kiln production line)
Specifications of China factory identification of high quality hot ing unique kiln rotary calcining rotary kiln production line
China factories create high-quality rotating kiln assembly line for calcining hot ingots. These systems handle high-temperature processing of products like metals and minerals. The layout focuses on efficiency and toughness. The kiln utilizes heat-resistant steel and unique refractory cellular linings. These materials take care of temperatures up to 1500 ° C. The framework resists wear and thermal stress and anxiety over long periods. This ensures stable efficiency in harsh commercial problems.
The rotating kiln’s home heating procedure is specific. Advanced temperature control systems keep heat circulation also. This stays clear of hot spots and material waste. The turning rate readjusts instantly. This matches the needs of various products. The system helps oxides, carbonates, and various other compounds. It guarantees consistent item top quality set after batch.
Power effectiveness is a key function. The kiln reuses waste warmth from exhaust gases. This reduces fuel usage and operating costs. Insulation layers decrease warm loss. Burners support several fuels like gas, oil, or coal. Individuals choose based upon accessibility and expense. The kiln’s reduced emissions satisfy environmental standards. Dirt collection agencies and filters decrease pollution.
The production line consists of a preheater and colder. The preheater elevates material temperature prior to entering the kiln. This conserves power. The cooler lowers item temperature after handling. This secures downstream equipment from damage. Conveyors and feeders relocate products smoothly in between phases. Automation minimizes manual work and errors.
The kiln’s drive system utilizes heavy-duty gears and electric motors. These offer trusted rotation under hefty tons. Sensors check rate, temperature, and pressure in actual time. Operators adjust setups remotely. Upkeep is easy. Access points and modular parts allow quick repair services. Technical assistance teams assist with installation and training.
Customization is available. Kiln sizes vary from small pilot versions to big commercial devices. Arrangements adapt to particular products or result goals. Factories examine each kiln prior to distribution. This assures efficiency suits specs. Spare components are standard for easy substitute.
The assembly line suits sectors like metallurgy, chemicals, and building and construction. It refines materials for concrete, alumina, or iron ore. The robust style makes certain long service life. It manages constant operation with marginal downtime. Running costs remain reduced as a result of energy-saving functions. Security systems secure employees and devices from accidents.
After-sales solution consists of normal assessments and troubleshooting. Technical teams give updates for enhancing efficiency. Individuals get outlined overviews for operation and upkeep.
(China factory identification of high quality hot ing unique kiln rotary calcining rotary kiln production line)
Applications of China factory identification of high quality hot ing unique kiln rotary calcining rotary kiln production line
The China factory’s high-grade hot ingot rotating calcining kiln assembly line manages commercial materials needing high-temperature processing. This system heats basic materials uniformly. It serves markets like cement, metallurgy, and chemicals. The rotating kiln’s style makes certain efficient warm transfer. This decreases energy waste. It works for refining limestone, gypsum, and metal ores.
The assembly line utilizes innovative automation. Sensors monitor temperature level, stress, and turning speed in real time. Operators readjust settings easily. This decreases human mistake. The kiln’s framework resists extreme warm. Durable products extend tools life. Upkeep costs stay low.
Constant item top quality is an essential advantage. The rotating kiln’s slow-moving rotation mixes materials extensively. Warm circulation remains also. This prevents unequal calcination. Result meets strict market criteria. It suits large production. Manufacturing facilities attain greater yields with less issues.
Power effectiveness is prioritized. Warm healing systems reuse excess thermal power. Fuel intake decreases. Discharges reduce. This aligns with ecological regulations. Companies reduced operational costs. Sustainability objectives are sustained.
Personalization choices exist. The production line adapts to different material types and result demands. Elements like preheaters or colders are included as required. This adaptability meets varied customer needs. Little and large projects are suited.
The kiln’s turning cylinder is developed for security. High-grade steel alloys deal with anxiety. Wear-resistant linings protect inner surfaces. Downtime is reduced. Manufacturing runs smoothly. Technical assistance groups assist with installation and training. Worldwide customers depend on this system for integrity.
After-sales services include components provide and fixing. Normal upkeep strategies protect against unanticipated break downs. Clients receive updates on performance optimization. Long-lasting partnerships are common. Responses drives continual improvements. The production line develops with industry demands.
Company Introduction
Established in 2001, plant Machinery Equipment Co.,ltd. focus on metal research and mining machinery spare parts. 2 factories over an area of 13,300 square meters, based on 100+ sets of equipment, our production capacity reaches 12000 Tons/Year. has passed ISO 9001 quality managment system certification in 2008.
Our mainly products are dragline excavator spare parts,rotary kiln spare parts, large modulus gear (gear shaft), gearbox ect. 40+ patents with over 45 years experience to help focus on improve the service life of spare parts. We belive that more than 80% reason of mechanical parts’ working life depends on hot processing (steel making/forging/casting/welding/heat treatment). Eight material engineers will control the quality from the original resource.
If you are interested, please feel free to contact us.
Payment
L/C, T/T, Western Union, Paypal, Credit Card etc.
Shipment
By sea, by air, by express, as customers request.
5 FAQs of China factory identification of high quality hot ing unique kiln rotary calcining rotary kiln production line
China factories producing high-quality hot ing unique kiln rotary calcining rotary kiln production lines often face common questions. Here are five FAQs with answers. What defines a high-quality rotary calcining kiln? High-quality rotary kilns use durable materials like heat-resistant alloys and advanced refractory bricks. These materials ensure long-term stability under extreme temperatures. Precise engineering reduces energy waste and improves heat distribution. How do factories control temperature during calcination? Factories use automated systems with real-time sensors. These systems adjust fuel flow and airflow automatically. Operators monitor data on screens to prevent overheating or uneven heating. What materials work best for this type of kiln? High-grade steel forms the kiln’s outer shell. Refractory linings inside handle direct contact with raw materials. Special alloys in critical parts resist corrosion and wear. Can the production line be customized for different industries? Yes. Factories adjust the kiln’s length, diameter, and rotation speed based on client needs. Heating methods vary too—options include gas, coal, or electric heating. Custom setups match specific material processing requirements. How do factories ensure consistent product quality? Strict quality checks happen at every stage. Raw materials are tested before use. During production, technicians sample outputs to verify chemical composition and physical properties. Regular equipment maintenance prevents unexpected breakdowns. Final products undergo third-party certification for reliability.
(China factory identification of high quality hot ing unique kiln rotary calcining rotary kiln production line)
REQUEST A QUOTE
RELATED PRODUCTS
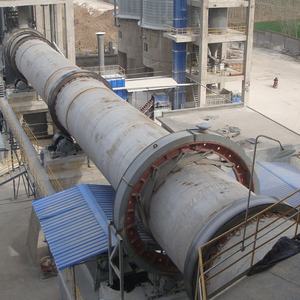
Citic Rotary kiln spare parts Rotary kiln forging supporting wheel
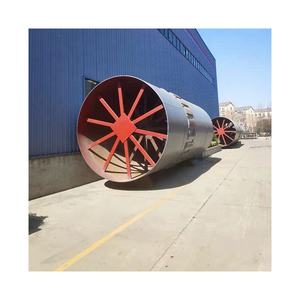
Rotary Kiln
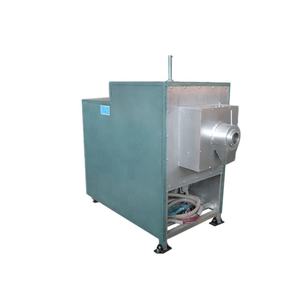
Lab Testing Kiln Small Rotary Kiln for Samples Calcination and Sintering
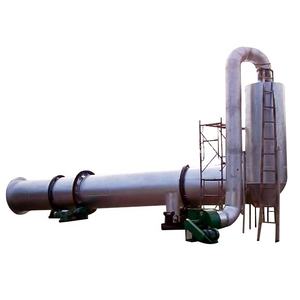
OEM Manufacture Casting Steel Rotary Kiln Spare Parts Ball Mill End Cover Casting Hollow Shaft
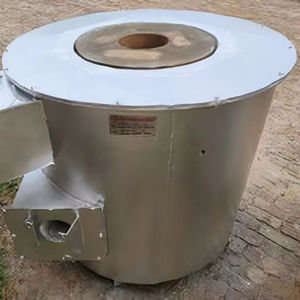
Ceramic Intalox Saddle Ring
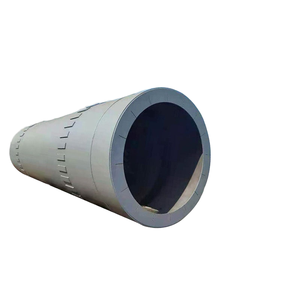