PRODUCT PARAMETERS
Description
Introduction of Cement Rotary Kiln Seal Rotary Kiln Barrel Parts
A rotary kiln is a kind of industrial equipment used for material heating and processing, which is widely used in cement, metallurgy, chemical industry, etc. Cement Rotary Kiln Seal Rotary Kiln Barrel Parts refers to various parts and components which are necessary for maintaining and repairing the normal operation of the rotary kiln, such as cylinder, baffle wheel, pallet, sealing device and so on.
Features and advantages of Cement Rotary Kiln Seal Rotary Kiln Barrel Parts
High-temperature resistance: Due to the extremely high temperature of the working environment of the rotary kiln, the spare parts are usually made of refractory materials or special alloys to ensure that they can work stably under high temperatures.
High abrasion resistance: Long time material friction and chemical erosion require spare parts to have excellent abrasion resistance to prolong service life.
High structural strength: in order to withstand heavy loads and the pressure of continuous operation, the design of spare parts will place special emphasis on structural strength and reliability.
Easy to install and maintain: Considering the need for frequent replacement, many spare parts are designed to be simpler and easier for quick installation and maintenance.
Strong adaptability: different industries have different needs for rotary kilns, so spare parts need to have good versatility and adaptability to meet diverse application conditions.
(Cement Rotary Kiln Seal Rotary Kiln Barrel Parts)
Specifications of Cement Rotary Kiln Seal Rotary Kiln Barrel Parts
Cement rotating kiln seals and barrel components are vital for efficient kiln procedure. The seals prevent air leakages and maintain temperature control. They use high-temperature alloys and ceramic fibers. These products manage severe warm up to 1500 ° C. The design includes numerous layers for far better insulation. The layers minimize warmth loss and improve power effectiveness. Seals adapt to kiln development during operation. They remain versatile under thermal tension. This flexibility prevents fractures and spaces. Maintenance is basic. Regular checks guarantee long life span. Replacements are uncommon if properly installed. Barrel components develop the primary framework of the kiln. They are made from durable steel. The steel resists buckling under heats. Barrel thickness varies from 40mm to 100mm. Thicker barrels take care of larger tons and higher heat. Welding methods guarantee smooth joints. Joints are examined for stamina and resilience. Barrel areas get in touch with accuracy. Alignment is important for smooth rotation. Misalignment causes uneven deterioration. Both seals and barrel parts work under constant turning. Rubbing is reduced through surface treatments. Unique finishings lower use from basic materials. Coatings likewise withstand chemical deterioration. This expands the life expectancy of components. All parts work with standard kiln sizes. Customized sizes are readily available for unique arrangements. Installation adheres to rigorous standards. Appropriate installation prevents functional concerns. Performance depends on correct component selection. Requirements match kiln capacity and manufacturing goals. High-capacity kilns require thicker barrels and progressed seals. Smaller kilns utilize lighter materials. Parts are evaluated in real-world conditions. Tests verify heat resistance and structural stability. Data from tests lead improvements. Upgrades focus on sturdiness and effectiveness. Normal lubrication of moving parts is needed. Lubes must withstand heats. Dust and particles prevail challenges. Seals block bits from going into the system. Tidy operation lowers maintenance regularity. Energy performance is a key advantage. Efficient seals cut fuel costs. Barrel honesty makes sure constant warmth distribution. Constant heat improves clinker top quality. Components are available from worldwide suppliers. Preparations vary based on personalization. Technical support helps with installment and troubleshooting. Security requirements fulfill market policies. Compliance makes sure reliable procedure. Applications consist of concrete plants, lime manufacturing, and mineral processing.
(Cement Rotary Kiln Seal Rotary Kiln Barrel Parts)
Applications of Cement Rotary Kiln Seal Rotary Kiln Barrel Parts
Cement rotary kiln seals and barrel parts play vital roles in commercial operations. These components make sure effective efficiency in high-temperature atmospheres. Rotating kiln seals stop gas leaks and preserve temperature level control inside the kiln. They decrease energy waste and shield tools from damage caused by exterior contaminants. Barrel components create the main framework of the kiln. They sustain rotational activity and deal with hefty tons throughout material handling. Both elements are important for smooth procedure in concrete manufacturing.
In cement manufacturing, rotating kiln seals aid handle warmth distribution. They keep combustion gases consisted of to optimize clinker development. Barrel components hold up against extreme warmth and mechanical stress and anxiety. Their resilient building and construction allows continual operation without frequent break downs. These components likewise help in lining up the kiln during rotation. Appropriate positioning decreases endure other machinery parts.
The steels market utilizes rotary kiln seals and barrels for ore processing. Seals prevent harmful fumes from running away during smelting. Barrel components supply a stable environment for chain reactions at heats. These reactions remove pure metals from raw ores. In chemical manufacturing, kiln seals ensure risk-free handling of unstable substances. Barrel materials stand up to rust from aggressive chemicals. This extends the devices’s lifespan.
Waste management systems rely upon rotating kiln innovation for incineration. Seals manage air movement to preserve burning performance. Barrel components handle rough waste materials without degrading. They make it possible for total failure of contaminated materials into inert residues. This procedure decreases ecological harm.
Rotary kiln seals and barrel components need regular maintenance. Inspection routines check for splits or put on in seals. Barrel surface areas are checked for bending or rust. Prompt substitutes avoid unanticipated shutdowns. Advanced products like refractory porcelains boost heat resistance. Customized develops adapt to particular industrial requirements.
Appropriate installment makes sure optimum performance of these parts. Skilled professionals straighten seals to avoid spaces. Barrel areas are bonded precisely to prevent misalignment. Training programs aid operators identify very early indicators of damage. Reputable providers provide top quality components examined under actual conditions. This assures compatibility with existing systems.
Rotating kiln innovation proceeds developing. Developments concentrate on power performance and resilience. Seals and barrel parts stay central to industrial procedures throughout industries. Their flexibility supports varied applications beyond typical concrete production.
Company Introduction
Established in 2001, plant Machinery Equipment Co.,ltd. focus on metal research and mining machinery spare parts. 2 factories over an area of 13,300 square meters, based on 100+ sets of equipment, our production capacity reaches 12000 Tons/Year. has passed ISO 9001 quality managment system certification in 2008.
Our mainly products are dragline excavator spare parts,rotary kiln spare parts, large modulus gear (gear shaft), gearbox ect. 40+ patents with over 45 years experience to help focus on improve the service life of spare parts. We belive that more than 80% reason of mechanical parts’ working life depends on hot processing (steel making/forging/casting/welding/heat treatment). Eight material engineers will control the quality from the original resource.
If you are interested, please feel free to contact us.
Payment
L/C, T/T, Western Union, Paypal, Credit Card etc.
Shipment
By sea, by air, by express, as customers request.
5 FAQs of Cement Rotary Kiln Seal Rotary Kiln Barrel Parts
Cement rotary kiln seals prevent material leakage and maintain temperature. They stop outside air from entering the kiln. This keeps combustion stable. Proper sealing reduces energy waste. It protects internal components from damage. Regular checks ensure seals stay effective. Dust buildup around seals should be cleaned often. Replace worn seals immediately to avoid bigger problems.
Rotary kiln barrel parts handle high heat and stress. They are made of heat-resistant steel. This steel lasts longer under extreme conditions. Barrel parts support the kiln’s rotation. They must align correctly to prevent uneven wear. Misalignment causes cracks or warping. Inspect barrel parts for cracks monthly. Fix small issues before they worsen.
Seal materials need durability and flexibility. Common options include ceramic fibers and metal alloys. Ceramic handles extreme temperatures. Metal alloys resist mechanical wear. The choice depends on kiln operating conditions. High-dust environments need abrasion-resistant materials. Check material compatibility with kiln processes before selecting.
Seal lifespan varies with usage and maintenance. Average seals last 6–12 months. Frequent temperature changes shorten lifespan. Poor alignment increases wear. Regular maintenance extends service life. Monitor seal condition during routine inspections. Replace seals showing cracks or thinning.
Faulty seals cause heat loss and inefficiency. Leaks reduce kiln temperature. This raises fuel consumption. Uncontrolled air inflow disrupts combustion. Product quality drops due to inconsistent heating. Dust leaks pose safety risks. Immediate seal replacement restores performance.
(Cement Rotary Kiln Seal Rotary Kiln Barrel Parts)
REQUEST A QUOTE
RELATED PRODUCTS
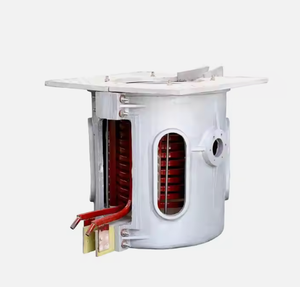
Roller and shaft of rotary kiln
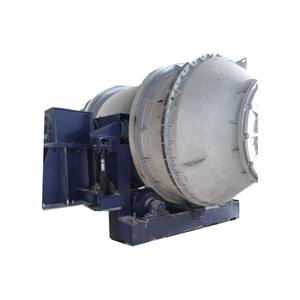
600 Tons Per Day Rotary Kiln/Calcining Kiln for Oil, Gas, and Coal Burning
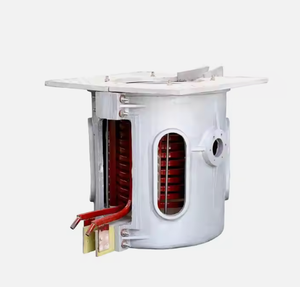
China factory identification of high quality hot ing unique kiln rotary calcining rotary kiln production line
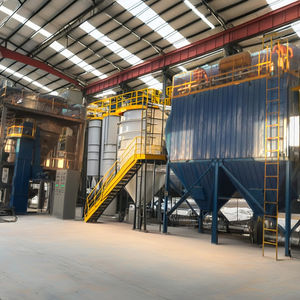
Laboratory Kiln 1100 1200 1400 1500 1600 1700 1800 Celsius Degree Electric Ceramic Box Melting Oven Vacuum Muffle Furnace
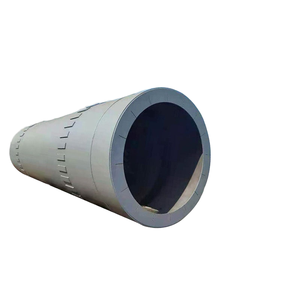
Continuous Non-metallic Rotary Kiln With 30-300kg/h Capacity
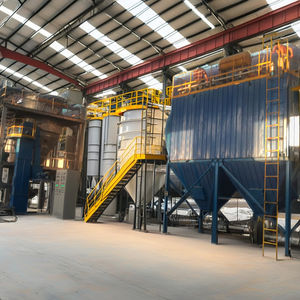