PRODUCT PARAMETERS
Description
Introduction of cement rotary kiln roller shaft with forging material
A rotary kiln is a kind of industrial equipment used for material heating and processing, which is widely used in cement, metallurgy, chemical industry, etc. cement rotary kiln roller shaft with forging material refers to various parts and components which are necessary for maintaining and repairing the normal operation of the rotary kiln, such as cylinder, baffle wheel, pallet, sealing device and so on.
Features and advantages of cement rotary kiln roller shaft with forging material
High-temperature resistance: Due to the extremely high temperature of the working environment of the rotary kiln, the spare parts are usually made of refractory materials or special alloys to ensure that they can work stably under high temperatures.
High abrasion resistance: Long time material friction and chemical erosion require spare parts to have excellent abrasion resistance to prolong service life.
High structural strength: in order to withstand heavy loads and the pressure of continuous operation, the design of spare parts will place special emphasis on structural strength and reliability.
Easy to install and maintain: Considering the need for frequent replacement, many spare parts are designed to be simpler and easier for quick installation and maintenance.
Strong adaptability: different industries have different needs for rotary kilns, so spare parts need to have good versatility and adaptability to meet diverse application conditions.
(cement rotary kiln roller shaft with forging material)
Specifications of cement rotary kiln roller shaft with forging material
The cement rotary kiln roller shaft is built for heavy-duty industrial use. The forging material ensures high strength and durability. This component supports the rotary kiln’s weight and handles continuous rotational stress. The shaft’s design prioritizes resistance to extreme temperatures and mechanical wear. Forged steel is the primary material. This choice enhances structural integrity under prolonged operation. The production process involves precision forging to eliminate internal defects. The result is a uniform grain structure for better load distribution.
Standard diameters range from 200mm to 1000mm. Lengths vary between 3000mm and 15000mm. Custom dimensions are available for specific kiln setups. The shaft’s surface undergoes machining to achieve tight tolerances. Surface roughness is controlled to reduce friction during rotation. Heat treatment processes like quenching and tempering are applied. These steps improve hardness and toughness. The final hardness typically reaches 200-300 HB. This ensures long-term performance in abrasive environments.
Load capacity depends on diameter and material grade. Axial loads up to 500 tons are manageable. Radial loads up to 300 tons are supported without deformation. Operating temperatures range from -20°C to 400°C. The shaft maintains stability even under thermal expansion. High-temperature alloys are optional for extreme heat applications. Anti-corrosion coatings can be added for humid or corrosive settings.
Quality checks include ultrasonic testing for internal flaws. Magnetic particle inspection detects surface cracks. Dimensional accuracy is verified with laser measurement tools. Each shaft is marked with production batch details for traceability. Installation guidelines specify alignment precision to prevent uneven stress. Regular lubrication is advised to minimize wear on bearing surfaces.
Custom designs accommodate unique kiln configurations. Flange connections or keyway slots are added as needed. Material certifications comply with international standards like ASTM or DIN. Technical drawings are provided for client approval before manufacturing. Lead times depend on order complexity and volume. Spare parts and maintenance services are available to extend equipment lifespan.
(cement rotary kiln roller shaft with forging material)
Applications of cement rotary kiln roller shaft with forging material
Company Introduction
Established in 2001, plant Machinery Equipment Co.,ltd. focus on metal research and mining machinery spare parts. 2 factories over an area of 13,300 square meters, based on 100+ sets of equipment, our production capacity reaches 12000 Tons/Year. has passed ISO 9001 quality managment system certification in 2008.
Our mainly products are dragline excavator spare parts,rotary kiln spare parts, large modulus gear (gear shaft), gearbox ect. 40+ patents with over 45 years experience to help focus on improve the service life of spare parts. We belive that more than 80% reason of mechanical parts’ working life depends on hot processing (steel making/forging/casting/welding/heat treatment). Eight material engineers will control the quality from the original resource.
If you are interested, please feel free to contact us.
Payment
L/C, T/T, Western Union, Paypal, Credit Card etc.
Shipment
By sea, by air, by express, as customers request.
5 FAQs of cement rotary kiln roller shaft with forging material
Cement rotary kiln roller shafts made from forging material are vital components in kiln systems. Common questions about these parts are answered here.
What makes forging material suitable for roller shafts? Forging material offers high strength and durability. The process aligns the metal’s grain structure, improving mechanical properties. This ensures the shaft withstands heavy loads and continuous rotation in harsh kiln environments.
How do forged roller shafts compare to cast ones? Forged shafts have fewer internal defects like voids or cracks. The forging process compacts the metal, enhancing density. Cast shafts may have inconsistencies due to cooling variations. Forged shafts handle stress better, reducing failure risks.
Can forged roller shafts resist high temperatures? Yes. They are made from heat-resistant alloy steels. These materials retain strength under extreme heat. Forging also improves thermal fatigue resistance. Proper heat treatment further boosts performance, ensuring stability in temperatures exceeding 1000°C.
What maintenance do forged roller shafts require? Regular inspections are critical. Check for surface cracks, wear, or deformation. Lubricate bearings and joints to minimize friction. Monitor alignment to prevent uneven stress. Clean debris to avoid abrasion. Maintenance schedules depend on operating conditions but are typically shorter than cast shafts’ schedules.
How long do forged roller shafts last? Lifespan varies with usage and maintenance. Properly maintained forged shafts last years longer than cast ones. Factors like load intensity, temperature, and alignment accuracy affect durability. High-quality forging materials and correct installation extend service life significantly.
(cement rotary kiln roller shaft with forging material)
REQUEST A QUOTE
RELATED PRODUCTS
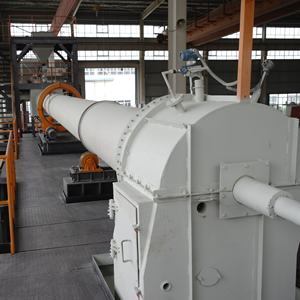
OEM Steel Rotary Kiln Support Roller Shaft
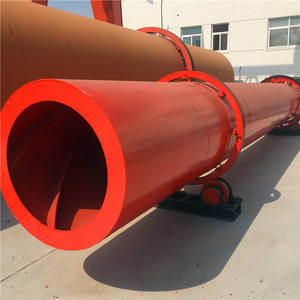
2024 OEM Rotary Kiln Spare parts trunnion roller Trunnion Wheels
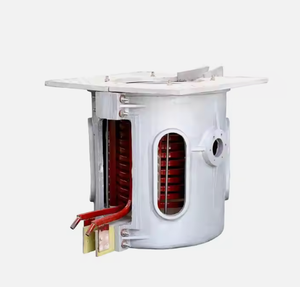
Rotary Industry KIln For Powder Sintering and Pellet Sintering
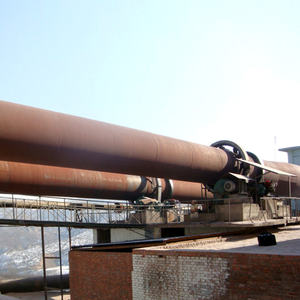
Large cement plant mill head rotary kiln spare parts welding ball mill welding drum
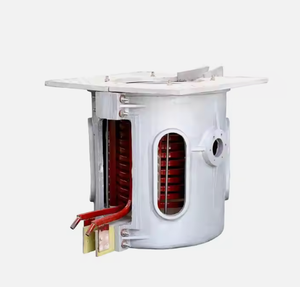
Roller and shaft of rotary kiln
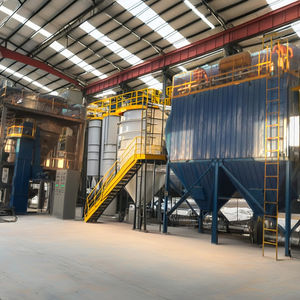