PRODUCT PARAMETERS
Description
Introduction of Best Energy-saving Rotary Dryer Furnace Kiln for Chemical/mining metallurgy Rotary Kiln
A rotary kiln is a kind of industrial equipment used for material heating and processing, which is widely used in cement, metallurgy, chemical industry, etc. Best Energy-saving Rotary Dryer Furnace Kiln for Chemical/mining metallurgy Rotary Kiln refers to various parts and components which are necessary for maintaining and repairing the normal operation of the rotary kiln, such as cylinder, baffle wheel, pallet, sealing device and so on.
Features and advantages of Best Energy-saving Rotary Dryer Furnace Kiln for Chemical/mining metallurgy Rotary Kiln
High-temperature resistance: Due to the extremely high temperature of the working environment of the rotary kiln, the spare parts are usually made of refractory materials or special alloys to ensure that they can work stably under high temperatures.
High abrasion resistance: Long time material friction and chemical erosion require spare parts to have excellent abrasion resistance to prolong service life.
High structural strength: in order to withstand heavy loads and the pressure of continuous operation, the design of spare parts will place special emphasis on structural strength and reliability.
Easy to install and maintain: Considering the need for frequent replacement, many spare parts are designed to be simpler and easier for quick installation and maintenance.
Strong adaptability: different industries have different needs for rotary kilns, so spare parts need to have good versatility and adaptability to meet diverse application conditions.
(Best Energy-saving Rotary Dryer Furnace Kiln for Chemical/mining metallurgy Rotary Kiln)
Specifications of Best Energy-saving Rotary Dryer Furnace Kiln for Chemical/mining metallurgy Rotary Kiln
The Very Best Energy-saving Rotary Dryer Heater Kiln for Chemical/Mining Metallurgy Rotating Kiln provides high performance in industrial drying out and thermal handling. Constructed for heavy-duty procedures, it manages products like ores, minerals, and chemical substances efficiently. The kiln makes use of sophisticated warmth healing systems to cut power use by as much as 30% compared to standard designs. This reduces functional costs while maintaining output high quality. Its style includes a multi-layer refractory cellular lining to trap heat inside the chamber. This guarantees even temperature level circulation throughout the drum. The external shell is made from wear-resistant alloy steel, appropriate for harsh settings. The rotating drum’s incline and rotation speed adjust immediately based on product kind and wetness degrees. This prevents getting too hot or under-drying. The kiln runs within a temperature level variety of 300 ° C to 1200 ° C, adaptable to various handling needs. A smart control system keeps track of real-time data like temperature level, stress, and air movement. Operators adjust setups through an user-friendly user interface, minimizing manual treatment. The kiln’s drive system utilizes a regularity converter for smooth speed adjustments, lowering mechanical tension. This extends the devices’s life-span. Maintenance is streamlined with conveniently obtainable assessment ports and exchangeable parts. The kiln’s combustion chamber supports several gas types, consisting of gas, diesel, and biomass. This adaptability assists industries comply with local exhaust requirements. Security attributes consist of automatic closure throughout pressure spikes or temperature level discrepancies. Emergency air conditioning systems activate if malfunctions take place. The kiln’s compact structure conserves floor room in commercial configurations. Noise degrees stay listed below 75 dB throughout procedure, conference work environment safety and security guidelines. Customizable drum sizes (1.5 m to 4.5 m) and lengths (15m to 50m) deal with varying production scales. Installation consists of optional dust removal systems to catch particulate emissions. Corrosion-resistant coatings safeguard internal parts from chemical reactions. The kiln sustains continuous 24/7 operation with marginal downtime. Yearly energy usage records assist track efficiency enhancements. Third-party qualifications validate conformity with worldwide safety and ecological guidelines.
(Best Energy-saving Rotary Dryer Furnace Kiln for Chemical/mining metallurgy Rotary Kiln)
Applications of Best Energy-saving Rotary Dryer Furnace Kiln for Chemical/mining metallurgy Rotary Kiln
The energy-saving rotating clothes dryer furnace kiln offers chemical, mining, and metallurgy industries. It refines materials like ores, minerals, and chemical compounds. The layout concentrates on cutting power usage while preserving high performance. Warmth recuperation systems capture waste warmth from exhaust gases. This heat is recycled to preheat incoming products. Fuel intake drops greatly. Running prices minimize with time.
The kiln’s insulation makes use of advanced products to reduce warm loss. Uniform temperature level distribution is achieved via enhanced air movement. Processing efficiency boosts. Material quality remains constant. Automated controls readjust temperature level, turning speed, and air flow in genuine time. Human error risks lower. System security boosts. Upkeep needs reduction.
In mining, the kiln dries out and calcines ores. Metallic concentrates are refined efficiently. Chemical markets utilize it to create stimulants and specialized powders. Metallurgy applications include toasting steel oxides and reducing steel substances. Contaminated materials treatment is one more vital usage. Hazardous substances are broken down safely. Environmental conformity is guaranteed.
Energy-saving functions minimize carbon exhausts. Business satisfy stricter ecological laws. Long life span comes from sturdy construction products. Wear-resistant liners handle unpleasant products. Downtime is lessened. Production routines remain trusted. Initial investment expenses are offset by long-term cost savings.
The rotating kiln adapts to varying product sizes and dampness levels. Personalized configurations match specific industry demands. Installation is simple. Training for drivers is straightforward. Technical assistance is offered for fixing. International markets rely on this devices for lasting, cost-effective processing.
Company Introduction
Established in 2001, plant Machinery Equipment Co.,ltd. focus on metal research and mining machinery spare parts. 2 factories over an area of 13,300 square meters, based on 100+ sets of equipment, our production capacity reaches 12000 Tons/Year. has passed ISO 9001 quality managment system certification in 2008.
Our mainly products are dragline excavator spare parts,rotary kiln spare parts, large modulus gear (gear shaft), gearbox ect. 40+ patents with over 45 years experience to help focus on improve the service life of spare parts. We belive that more than 80% reason of mechanical parts’ working life depends on hot processing (steel making/forging/casting/welding/heat treatment). Eight material engineers will control the quality from the original resource.
If you are interested, please feel free to contact us.
Payment
L/C, T/T, Western Union, Paypal, Credit Card etc.
Shipment
By sea, by air, by express, as customers request.
5 FAQs of Best Energy-saving Rotary Dryer Furnace Kiln for Chemical/mining metallurgy Rotary Kiln
The Best Energy-Saving Rotary Dryer Furnace Kiln for Chemical/Mining Metallurgy Rotary Kiln reduces energy use. It handles high-temperature processing for materials like ores and chemicals. Below are common questions about this equipment.
What makes this rotary kiln energy-efficient? The kiln uses advanced heat recovery systems. These systems capture waste heat. The heat gets reused in the drying process. Insulation layers prevent heat loss. Automated controls adjust temperature and airflow. This cuts fuel consumption.
How does the rotary kiln work? Materials enter the rotating drum. The drum tilts slightly. This lets materials move from the higher end to the lower end. Burners or electric heaters warm the drum. Hot gases or indirect heating dry or process the materials. Rotation ensures even exposure to heat.
What materials can this kiln process? It handles minerals, metal ores, chemical powders, and industrial waste. It works for drying, calcining, roasting, or sintering. The high-temperature range suits different industrial needs. Users must check material compatibility with the kiln’s lining.
What maintenance does the kiln need? Regular inspection prevents breakdowns. Check the drum’s lining for wear. Clean heat exchangers and ducts. Lubricate rotating parts. Monitor sensors and controls. Follow the manufacturer’s schedule. Proper maintenance keeps efficiency high.
Are safety features included? Yes. The kiln has temperature sensors. These trigger alarms if overheating occurs. Pressure relief valves prevent explosions. Emergency shutdown systems activate during malfunctions. Safety locks protect workers during operation. Training is needed to handle equipment safely.
(Best Energy-saving Rotary Dryer Furnace Kiln for Chemical/mining metallurgy Rotary Kiln)
REQUEST A QUOTE
RELATED PRODUCTS
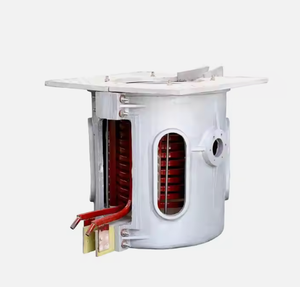
New Typesmall rotary tunnel kiln used kiln for red brick soil brick
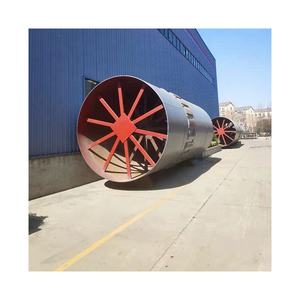
High Temperature Kiln Muffle Oven Lab 1100 1200 1400 1500 1600 1700 1800 Degree Electric Ceramic Box Melting Muffle Furnace
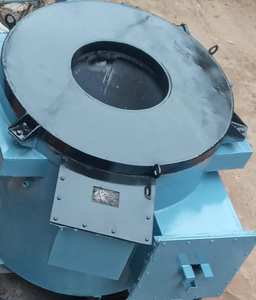
Hot s Energy Saving OEM Cement Rotary Kiln Tyre/wheel /Kaolin rotary kiln Wheel spare parts Forged Ring /Supporting Ring
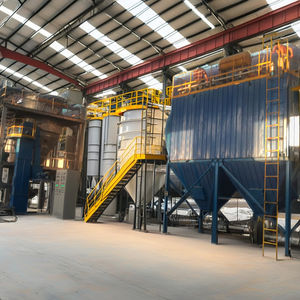
1100 Degree Indirect External Heating Rotary Kiln For Processing Active Carbon Carbonate Catalyst Mineral Powder Caclining
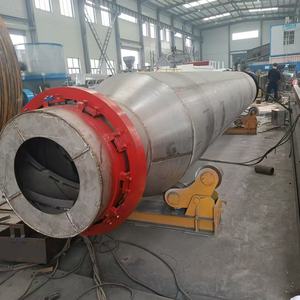
Large Wheel Large Diameter Spur Gear High Quality Cnc Machining Rotary Kiln Big Wheel
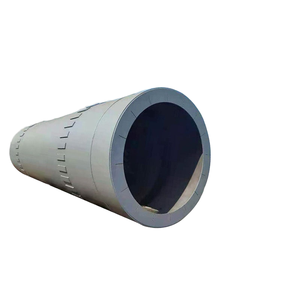