PRODUCT PARAMETERS
Description
Introduction of 300m3 per Day Shale Calcination Rotary Kiln Kaolin Rotary Kiln Leca China Rotary Kiln s
A rotary kiln is a kind of industrial equipment used for material heating and processing, which is widely used in cement, metallurgy, chemical industry, etc. 300m3 per Day Shale Calcination Rotary Kiln Kaolin Rotary Kiln Leca China Rotary Kiln s refers to various parts and components which are necessary for maintaining and repairing the normal operation of the rotary kiln, such as cylinder, baffle wheel, pallet, sealing device and so on.
Features and advantages of 300m3 per Day Shale Calcination Rotary Kiln Kaolin Rotary Kiln Leca China Rotary Kiln s
High-temperature resistance: Due to the extremely high temperature of the working environment of the rotary kiln, the spare parts are usually made of refractory materials or special alloys to ensure that they can work stably under high temperatures.
High abrasion resistance: Long time material friction and chemical erosion require spare parts to have excellent abrasion resistance to prolong service life.
High structural strength: in order to withstand heavy loads and the pressure of continuous operation, the design of spare parts will place special emphasis on structural strength and reliability.
Easy to install and maintain: Considering the need for frequent replacement, many spare parts are designed to be simpler and easier for quick installation and maintenance.
Strong adaptability: different industries have different needs for rotary kilns, so spare parts need to have good versatility and adaptability to meet diverse application conditions.
(300m3 per Day Shale Calcination Rotary Kiln Kaolin Rotary Kiln Leca China Rotary Kiln s)
Specifications of 300m3 per Day Shale Calcination Rotary Kiln Kaolin Rotary Kiln Leca China Rotary Kiln s
The 300m³ per day shale calcination rotary kiln processes kaolin, shale, and lightweight expanded clay aggregate (LECA). It handles high-temperature treatment for industrial applications. The kiln operates at temperatures up to 1250°C. This ensures effective calcination. The design includes a rotating steel cylinder lined with heat-resistant materials. The cylinder length ranges between 40-80 meters. The diameter varies from 2.5-4 meters. This allows flexibility for different production scales. The kiln uses natural gas, coal, or diesel as fuel. The system supports continuous operation with stable heat distribution.
Materials enter the kiln from the upper end. They move slowly toward the lower end due to rotation and tilt. Heat transfers evenly during this process. The residence time adjusts based on material type. This guarantees proper calcination. A dedicated combustion system maintains temperature accuracy. Exhaust gases pass through dust collectors and emission control units. This reduces environmental impact.
The kiln structure features support rollers and thrust rollers. These ensure smooth rotation. A gear-and-pinion drive system powers the rotation. Variable speed control adapts to process requirements. Refractory lining protects the shell from extreme heat. High-alumina bricks or castables line the interior. This extends service life. Thermal insulation layers minimize energy loss. Heat recovery systems reuse waste heat. This improves efficiency.
Automated controls monitor temperature, pressure, and airflow. Sensors send real-time data to a central panel. Operators adjust parameters for optimal performance. Safety mechanisms include emergency shutdowns and pressure relief valves. Regular maintenance checks prevent downtime. Access points simplify inspection and repairs.
The kiln produces activated kaolin for ceramics and paper coatings. It calcines shale for cement production. LECA output serves lightweight construction materials. The equipment suits large-scale mineral processing plants. Custom configurations match specific material needs. Durable construction ensures long-term reliability. Compact designs save space in industrial setups.
The rotary kiln meets international standards for industrial machinery. It combines high output with low operational costs. Robust materials withstand harsh operating conditions. Skilled engineers provide installation and training support. China-based manufacturers offer competitive pricing and technical services. The kiln is widely used in construction, ceramics, and chemical industries.
(300m3 per Day Shale Calcination Rotary Kiln Kaolin Rotary Kiln Leca China Rotary Kiln s)
Applications of 300m3 per Day Shale Calcination Rotary Kiln Kaolin Rotary Kiln Leca China Rotary Kiln s
The 300m³ per day shale calcination rotary kiln serves multiple industrial applications. It processes kaolin for ceramics, paper coatings, paints, and rubber. The kiln heats kaolin to remove impurities, improving brightness and chemical stability. This makes the material suitable for high-end products. The same kiln produces lightweight expanded clay aggregate (LECA). LECA is used in construction for insulation, lightweight concrete, and drainage systems. The kiln’s design ensures even heating, critical for creating uniform pore structures in LECA.
This rotary kiln operates at high temperatures, reaching up to 1,300°C. It uses advanced combustion systems for fuel efficiency. The rotating drum design allows continuous processing, reducing downtime. The kiln handles large volumes daily, making it ideal for industrial-scale production. Its structure includes heat-resistant materials, ensuring durability under extreme conditions.
The kiln supports customization. Adjustments can be made to temperature profiles, rotation speed, and retention time. This flexibility suits varying raw material qualities. For kaolin, precise control over calcination parameters enhances product purity. For LECA, adjusting heating rates optimizes expansion and strength.
Environmental compliance is a key feature. The kiln integrates dust collectors and emission control systems. These reduce particulate matter and gases released during operation. Energy recovery systems reuse waste heat, cutting fuel consumption. This aligns with stricter environmental regulations in industries worldwide.
Automation improves operational safety and consistency. Sensors monitor temperature, pressure, and gas levels in real time. Operators adjust settings remotely, minimizing human error. Automated systems trigger alerts for maintenance needs, preventing unexpected breakdowns.
The kiln’s construction uses high-grade steel and refractory bricks. This ensures long service life under thermal stress. Regular maintenance is simple, requiring basic checks of seals, bearings, and heating elements. Spare parts are widely available, reducing repair delays.
Reliability makes this kiln a preferred choice for manufacturers. It delivers stable performance across different materials and production goals. Its adaptability supports diverse industries, from construction to advanced material processing. Users benefit from consistent output quality, meeting international standards for industrial applications.
Company Introduction
Established in 2001, plant Machinery Equipment Co.,ltd. focus on metal research and mining machinery spare parts. 2 factories over an area of 13,300 square meters, based on 100+ sets of equipment, our production capacity reaches 12000 Tons/Year. has passed ISO 9001 quality managment system certification in 2008.
Our mainly products are dragline excavator spare parts,rotary kiln spare parts, large modulus gear (gear shaft), gearbox ect. 40+ patents with over 45 years experience to help focus on improve the service life of spare parts. We belive that more than 80% reason of mechanical parts’ working life depends on hot processing (steel making/forging/casting/welding/heat treatment). Eight material engineers will control the quality from the original resource.
If you are interested, please feel free to contact us.
Payment
L/C, T/T, Western Union, Paypal, Credit Card etc.
Shipment
By sea, by air, by express, as customers request.
5 FAQs of 300m3 per Day Shale Calcination Rotary Kiln Kaolin Rotary Kiln Leca China Rotary Kiln s
1. What does a 300m³ per day shale calcination rotary kiln do? It heats shale to high temperatures. This removes water and organic substances. The process activates materials for industries like construction. The kiln handles 300 cubic meters of material daily. It ensures consistent heat distribution for quality output.
2. How does the kaolin rotary kiln function? The kaolin rotary kiln rotates slowly. Materials move from the upper end to the lower end. Heat is applied gradually. This removes chemical impurities. It adjusts temperatures based on kaolin purity. The result is high-grade kaolin for ceramics or paper.
3. What materials work with the LECA China rotary kiln? It processes lightweight expanded clay aggregate (LECA). Raw materials include clay or shale. The kiln expands these materials at high heat. This creates porous, lightweight pellets. The pellets are used in construction for insulation or concrete.
4. What energy efficiency does the rotary kiln offer? The kiln uses advanced heat recovery systems. Insulation layers reduce heat loss. It supports multiple fuel types like gas or coal. Automated controls optimize burning efficiency. This cuts energy waste. Operating costs stay low.
5. How long does the rotary kiln last? Regular maintenance extends its lifespan. Components like refractory lining need periodic checks. Wear-resistant materials reduce damage from high temperatures. Proper care ensures 8-15 years of service. Spare parts are easy to replace. Downtime remains minimal.
(300m3 per Day Shale Calcination Rotary Kiln Kaolin Rotary Kiln Leca China Rotary Kiln s)
REQUEST A QUOTE
RELATED PRODUCTS
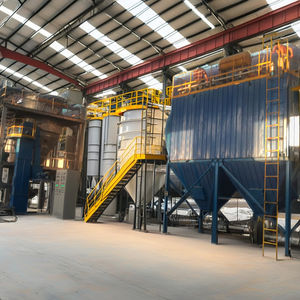
1100 Degree Indirect External Heating Rotary Kiln For Processing Active Carbon Carbonate Catalyst Mineral Powder Caclining
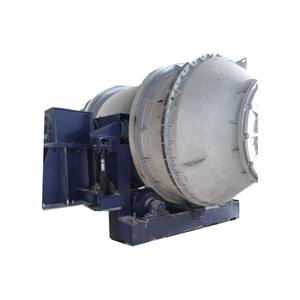
600 Tons Per Day Rotary Kiln/Calcining Kiln for Oil, Gas, and Coal Burning
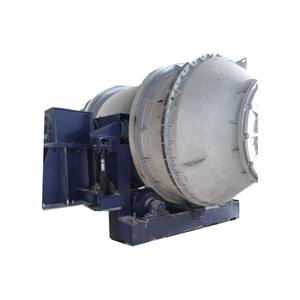
Rotary kiln for thermal processing Rotary kiln for energy-efficient operations Rotary kiln for environmental management
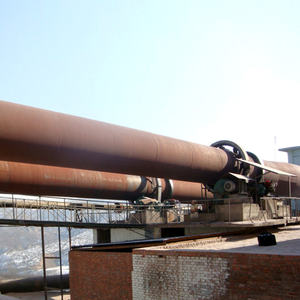
Large cement plant mill head rotary kiln spare parts welding ball mill welding drum
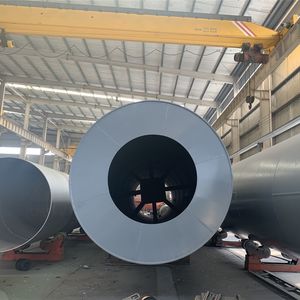
Rotary Kiln Spare Part Kiln Sealing/Big Gear Ring/Support Roller
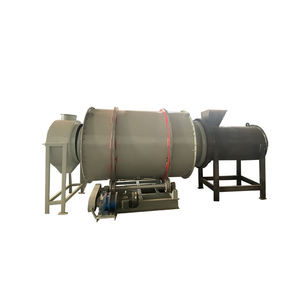