PRODUCT PARAMETERS
Description
Introduction to Industrial drying drum system, rotary drum dryer for asphalt mixing plant
Industrial drying drum system, rotary drum dryer for asphalt mixing plant is for repairing, replacing or upgrading worn, damaged or deteriorated parts in drying equipment. These spare parts can include heating elements, drums, belts, fans, temperature and humidity controls, etc., to ensure that the dryer will run efficiently and consistently.
Advantages and features of Industrial drying drum system, rotary drum dryer for asphalt mixing plant
High-quality materials: manufactured using durable and heat-resistant materials to ensure long life and high reliability.
Precise Fit: Precisely designed for specific models of dryers to ensure easy installation and perfect fit.
Rapid Response: Provide fast spare parts supply service to reduce downtime and improve production efficiency.
Technical Support: Equipped with a professional technical support team to provide installation guidance and troubleshooting assistance.
Cost-effectiveness: Reduce long-term operating costs by extending the service life of the equipment.
(Industrial drying drum system, rotary drum dryer for asphalt mixing plant)
Specifications of Industrial drying drum system, rotary drum dryer for asphalt mixing plant
The industrial drying drum system, likewise referred to as a rotary drum dryer, is a crucial component in asphalt blending plants, made to efficiently remove dampness from accumulations while making sure optimal temperature level control for asphalt manufacturing. This durable system includes a revolving cylindrical drum made of top-quality, heat-resistant steel, engineered to withstand continuous procedure under extreme thermal and mechanical anxiety. The drum is commonly lined with sturdy interior trips that raise and waterfall aggregates, advertising consistent warm circulation and making the most of call with hot gases produced by the incorporated heater system.
Trick requirements include a drum diameter ranging from 1.5 to 3 meters and a length of 6 to 12 meters, depending on plant capacity. Turning rates are flexible in between 5 to 10 RPM, guaranteeing exact control over drying time and aggregate circulation. The system sustains accumulated throughput abilities from 80 to 400 loads per hour, accommodating small to large-scale asphalt manufacturing needs. The heater, powered by diesel, natural gas, or hefty oil, delivers a thermal output of 8 to 40 million kcal/h, with fire modulation technology for gas efficiency and constant heating.
Warmth exchange efficiency is improved by counterflow style, where aggregates move opposite to the direction of hot gases, reducing power usage. Temperature level sensing units and automated control systems preserve drum departure temperatures in between 150 ° C to 200 ° C, vital for proper asphalt binder attachment. The clothes dryer is geared up with a dirt collection system, including cyclones or baghouse filters, to record airborne fragments and comply with ecological policies.
Durable equipment electric motors, trunnion rollers, and drive systems make certain smooth, low-maintenance procedure. Insulation layers minimize warmth loss, while abrasion-resistant cellular linings prolong service life. Adjustable setups consist of variable drum disposition (3-5 levels) and choices for parallel or counterflow operation. The system integrates effortlessly with asphalt plant controls, allowing real-time monitoring of dampness degrees, temperature, and manufacturing prices. Developed to ISO and CE criteria, this rotary drum dryer guarantees reliability, longevity, and high performance in diverse commercial conditions.
(Industrial drying drum system, rotary drum dryer for asphalt mixing plant)
Applications of Industrial drying drum system, rotary drum dryer for asphalt mixing plant
Industrial drying drum systems, especially rotary drum clothes dryers, are crucial parts in asphalt mixing plants, made to efficiently completely dry and warm aggregates such as sand, crushed rock, and crushed rock. These systems make certain the removal of moisture from resources, an important action in producing high-grade asphalt blends. Dampness in accumulations can compromise the bonding with bitumen, resulting in weak sidewalk frameworks. The rotary drum clothes dryer utilizes a turning round drum integrated with a high-temperature heater– powered by fuels like diesel, natural gas, or recycled oils– to accomplish uniform drying out. As the drum revolves, aggregates are raised and cascaded via the warmed air flow, ensuring constant exposure to temperatures in between 150 ° C and 200 ° C. This process not just eliminates wetness but also preheats the products, enhancing their preparedness for mixing with bitumen. A crucial application of rotating drum dryers is in the manufacturing of warm mix asphalt (HMA), where accurate temperature control and dampness elimination are important for sturdiness. They likewise sustain sustainable practices by refining recycled asphalt pavement (RAP), allowing the reuse of old asphalt materials while maintaining mix stability. Modern systems are engineered for adaptability, handling varying accumulated dimensions and wetness levels, and are typically integrated with recycling components to decrease waste. Energy performance is a hallmark of sophisticated rotating clothes dryers, integrating attributes like warmth recuperation systems and protected drums to lessen fuel consumption. Environmental conformity is attended to with discharge control innovations, including baghouse filters and scrubbers, which capture particle matter and reduce contaminants. Developed from robust, heat-resistant materials like high-grade steel, these clothes dryers endure extreme operating conditions, ensuring lengthy life span with minimal upkeep. Personalized configurations, such as adjustable turning speeds, heater kinds, and automation user interfaces, enable seamless integration right into existing asphalt plants. By ensuring regular drying performance, rotating drum dryers boost the top quality of asphalt blends, adding to the construction of resilient roads. Their dependability, efficiency, and versatility make them crucial in modern asphalt production, straightening with industry demands for cost-effectiveness and environmental duty.
Company Introduction
Established in 2001, plant Machinery Equipment Co.,ltd. focus on metal research and mining machinery spare parts. 2 factories over an area of 13,300 square meters, based on 100+ sets of equipment, our production capacity reaches 12000 Tons/Year. has passed ISO 9001 quality managment system certification in 2008.
Our mainly products are dragline excavator spare parts,rotary kiln spare parts, large modulus gear (gear shaft), gearbox ect. 40+ patents with over 45 years experience to help focus on improve the service life of spare parts. We belive that more than 80% reason of mechanical parts’ working life depends on hot processing (steel making/forging/casting/welding/heat treatment). Eight material engineers will control the quality from the original resource.
If you are interested, please feel free to contact us.
Payment
L/C, T/T, Western Union, Paypal, Credit Card etc.
Shipment
By sea, by air, by express, as customers request.
5 FAQs of Industrial drying drum system, rotary drum dryer for asphalt mixing plant
What is a rotary drum dryer in an asphalt mixing plant?
A rotary drum dryer is a critical component in asphalt production, designed to remove moisture from aggregates like sand, stone, and gravel. It uses a rotating cylindrical drum heated by a burner to evaporate water, ensuring optimal moisture content (typically below 0.5%) for proper asphalt mixing. The dried aggregates are then mixed with bitumen to produce high-quality asphalt.
How does a rotary drum dryer work?
The system feeds cold, wet aggregates into one end of a rotating drum. As the drum rotates, flights inside lift and cascade the material, exposing it to hot gases from a burner (temperatures between 150°C to 400°C). This continuous tumbling ensures uniform drying. The dried aggregates exit the drum’s opposite end, while exhaust gases pass through a filtration system to reduce emissions.
What maintenance is required for a rotary drum dryer?
Regular maintenance includes inspecting and replacing worn flights, checking burner nozzles for clogs, monitoring drum alignment, and lubricating bearings. Cleaning heat exchangers and ensuring insulation integrity prevents heat loss. Daily inspections of temperature sensors, drive belts, and seals help avoid unexpected downtime. Annual shutdowns for thorough internal inspections and refractory lining repairs are recommended for longevity.
How to optimize the efficiency of a rotary drum dryer?
Efficiency depends on proper burner calibration, consistent feed rates, and maintaining optimal drum speed. Use high-quality fuel for clean combustion, and ensure aggregates are pre-screened to avoid oversized particles. Insulating the drum minimizes heat loss, while recycling exhaust heat via secondary systems (e.g., thermal oil heaters) improves energy use. Regularly monitor moisture levels to adjust drying parameters dynamically.
What are common issues with rotary drum dryers?
Common problems include uneven drying (caused by worn flights or inconsistent feed), excessive fuel consumption (due to poor insulation or burner issues), and drum misalignment leading to vibration. Blockages from sticky or oversized materials can disrupt flow, while overheating may damage the drum or aggregates. Addressing these requires routine checks, timely part replacements, and calibrating equipment to manufacturer specifications.
(Industrial drying drum system, rotary drum dryer for asphalt mixing plant)
REQUEST A QUOTE
RELATED PRODUCTS
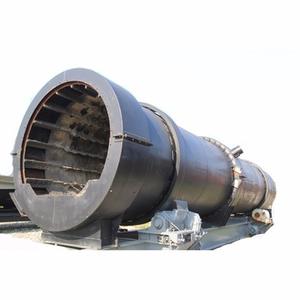
High quality Dryer parts Electric Dryer Heating Element 3387747 Heating parts 3387747

Centrifugal Nozzle Spray Dryer Atomizer with Rotary Disk Atomizer
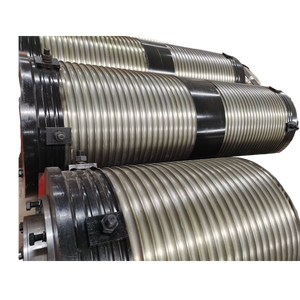
a 10tph rotary drum dryer Coal Slime Cassava Rotary Dryer With Spare Parts
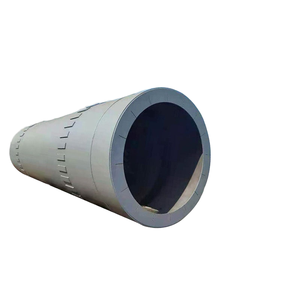
Heat Source Sawdust Dryer Rotary Dryer and Drum Dryer for Drying Coconut Shell
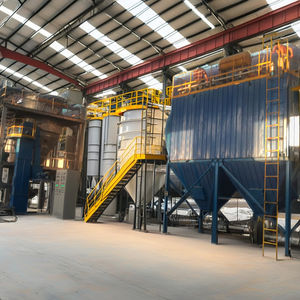
Mud Coal Slag Rotary Dryer Cement Ore Powder Rotary Drum Dryer Sand Dryer for
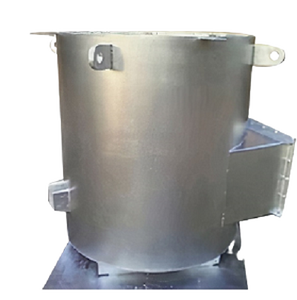