PRODUCT PARAMETERS
Description
Introduction of Hot ing Support Roller Rotary Kiln Shaft with low
A rotary kiln is a kind of industrial equipment used for material heating and processing, which is widely used in cement, metallurgy, chemical industry, etc. Hot ing Support Roller Rotary Kiln Shaft with low refers to various parts and components which are necessary for maintaining and repairing the normal operation of the rotary kiln, such as cylinder, baffle wheel, pallet, sealing device and so on.
Features and advantages of Hot ing Support Roller Rotary Kiln Shaft with low
High-temperature resistance: Due to the extremely high temperature of the working environment of the rotary kiln, the spare parts are usually made of refractory materials or special alloys to ensure that they can work stably under high temperatures.
High abrasion resistance: Long time material friction and chemical erosion require spare parts to have excellent abrasion resistance to prolong service life.
High structural strength: in order to withstand heavy loads and the pressure of continuous operation, the design of spare parts will place special emphasis on structural strength and reliability.
Easy to install and maintain: Considering the need for frequent replacement, many spare parts are designed to be simpler and easier for quick installation and maintenance.
Strong adaptability: different industries have different needs for rotary kilns, so spare parts need to have good versatility and adaptability to meet diverse application conditions.
(Hot ing Support Roller Rotary Kiln Shaft with low )
Specifications of Hot ing Support Roller Rotary Kiln Shaft with low
The Hot Ing Support Roller Rotary Kiln Shaft is built for heavy-duty commercial applications. It takes care of high-temperature procedures efficiently. The shaft is made from state-of-the-art alloy steel. This makes sure resilience under severe warm. The external surface is covered with heat-resistant material. This safeguards the framework from thermal damage. The roller diameter varies from 800 mm to 2000 mm. Custom-made sizes are readily available based on kiln requirements. Each roller sustains lots up to 500 lots. This capacity fits large manufacturing demands. The design includes self-aligning bearings. These reduce friction during rotation. Upkeep is streamlined due to modular elements. Substitute parts are easy to set up. The rollers run smoothly at temperature levels as much as 1000 ° C. Air conditioning systems are integrated to prevent overheating. Power consumption is enhanced for power efficiency. The kiln shaft rotates at flexible rates. This permits exact control over material handling. An electronic tracking system tracks performance in real time. Operators get informs for irregularities. The surface is polished to decrease wear. This prolongs the tools’s life expectancy. Installment calls for marginal foundation. The shaft links effortlessly to existing kiln arrangements. Security functions include emergency situation braking systems. These halt procedures instantaneously throughout breakdowns. Lubrication ports are placed for simple gain access to. Regular greasing lowers component anxiety. The rollers are tested for balance and positioning. This stops resonance throughout usage. Sound levels are kept low for work environment safety and security. The kiln shaft abides by international commercial criteria. It appropriates for cement, metallurgy, and chemical sectors. Functional costs are decreased via energy-saving designs. Downtime is reduced as a result of reliable building. Technical support is available for repairing. Extra components are stocked for quick distribution. The tools is shipped pre-assembled. On-site installation services are optional. Training is provided for safe operation.
(Hot ing Support Roller Rotary Kiln Shaft with low )
Applications of Hot ing Support Roller Rotary Kiln Shaft with low
Warm support roller rotating kiln shafts manage high-temperature procedures in sectors such as concrete production, metallurgy, and chemical manufacturing. These parts sustain turning kilns throughout product handling. Their layout makes certain security under severe heat, reducing wear and enhancing functional performance.
In cement plants, these rollers help rotate kilns throughout clinker production. They endure temperatures over 1000 ° C, preserving structural stability. This protects against kiln contortion, ensuring constant output. The low-friction layout decreases energy usage, reducing prices.
Metallurgical sectors make use of these rollers in steel ore processing. They endure harsh problems throughout smelting and refining. Their robust building and construction minimizes downtime caused by equipment failure. This integrity sustains constant procedure, important for meeting manufacturing targets.
Chemical manufacturing counts on these rollers for refining raw materials like limestone and gypsum. High heat resistance allows smooth operation in aggressive atmospheres. The rollers’ even weight distribution stops irregular wear, extending service life.
Mining procedures gain from these elements in mineral handling. They take care of heavy loads and unpleasant products without shedding performance. The low-maintenance layout minimizes frequent repairs, conserving time and resources.
Waste treatment facilities make use of these rollers in incineration systems. They manage thermal development during waste-to-energy procedures. This avoids mechanical anxiety, guaranteeing system long life. The rollers’ flexibility to temperature level variations boosts procedure control.
These applications highlight the roller’s versatility. Resilient materials like alloy steel and advanced warmth therapy methods improve performance. Normal lubrication systems keep friction reduced, stopping overheating. Customized sizing options fit various kiln specifications, providing flexibility.
Operators value the decreased need for substitutes. This lowers long-lasting expenses while keeping high safety and security requirements. The rollers’ precision engineering aligns kilns appropriately, avoiding imbalance issues. This uniformity sustains efficient warmth transfer, optimizing item top quality.
Industries prioritize these rollers for essential high-temperature tasks. Their function in preserving operational continuity makes them necessary for massive production. The mix of stamina, warmth resistance, and efficiency addresses challenges in heavy commercial setups.
Company Introduction
Established in 2001, plant Machinery Equipment Co.,ltd. focus on metal research and mining machinery spare parts. 2 factories over an area of 13,300 square meters, based on 100+ sets of equipment, our production capacity reaches 12000 Tons/Year. has passed ISO 9001 quality managment system certification in 2008.
Our mainly products are dragline excavator spare parts,rotary kiln spare parts, large modulus gear (gear shaft), gearbox ect. 40+ patents with over 45 years experience to help focus on improve the service life of spare parts. We belive that more than 80% reason of mechanical parts’ working life depends on hot processing (steel making/forging/casting/welding/heat treatment). Eight material engineers will control the quality from the original resource.
If you are interested, please feel free to contact us.
Payment
L/C, T/T, Western Union, Paypal, Credit Card etc.
Shipment
By sea, by air, by express, as customers request.
5 FAQs of Hot ing Support Roller Rotary Kiln Shaft with low
1. What is a Hot Ing Support Roller Rotary Kiln Shaft?
This part supports the rotary kiln during operation. It handles high temperatures and heavy loads. The roller ensures smooth rotation. It is made of heat-resistant materials. This prevents damage from prolonged heat exposure.
2. How does the support roller work in a rotary kiln?
The roller sits under the kiln’s rotating cylinder. It helps distribute weight evenly. The kiln turns continuously during heating. The roller reduces friction during rotation. This keeps the kiln stable. It stops misalignment or uneven wear.
3. What maintenance does the support roller need?
Check the roller surface regularly for cracks or wear. Lubricate bearings to reduce friction. Monitor temperature during operation. Clean debris around the roller area. Replace parts showing significant damage. Follow the manufacturer’s schedule for inspections.
4. What affects the lifespan of a support roller?
Material quality impacts durability. High heat speeds up wear. Proper alignment extends service time. Regular maintenance prevents early failure. Overloading the kiln strains the roller. Operating conditions like dust or moisture matter.
5. What problems happen with support rollers?
Common issues include uneven roller wear. This comes from poor alignment or unbalanced loads. Bearing failure occurs without enough lubrication. Surface cracks form from thermal stress. Roller skewing causes kiln vibration. Fix these quickly to avoid downtime.
(Hot ing Support Roller Rotary Kiln Shaft with low )
REQUEST A QUOTE
RELATED PRODUCTS
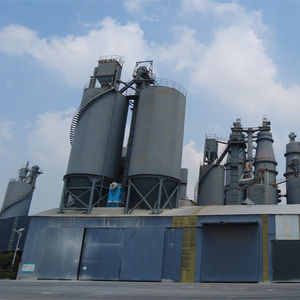
Rotary Kiln For lime, Cement Making Machinery Production Line Spare parts, Support Roller Quick Lime Rotary Kiln
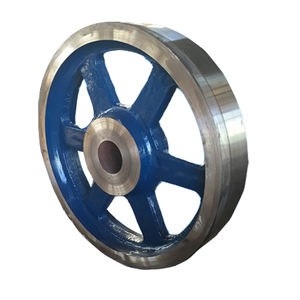
Metal Metallurgy Machinery Top ing For Producing Parts Advanced Machines High Quality Arc Metal Industrial Sintering Furnace
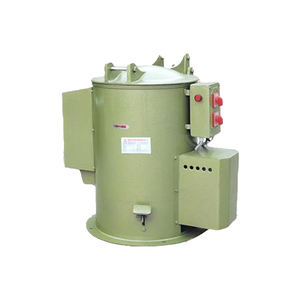
Refractory Cordierite Ceramic Heating parts Factory Direct
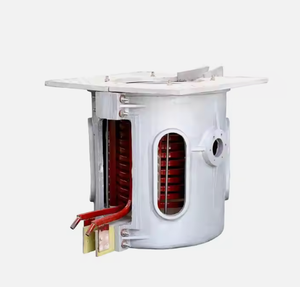
Industrial Metal Melting Furnace Arc Top ing Equipment Machine For Producing Parts By Powder Metallurgy Met
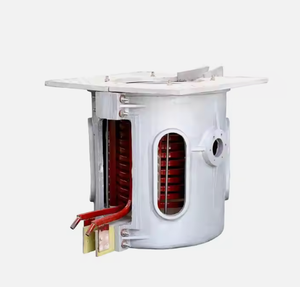
China factory identification of high quality hot ing unique kiln rotary calcining rotary kiln production line
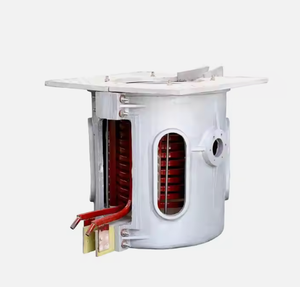