PRODUCT PARAMETERS
Description
Introduction of 1100 Degree Indirect External Heating Rotary Kiln For Processing Active Carbon Carbonate Catalyst Mineral Powder Caclining
A rotary kiln is a kind of industrial equipment used for material heating and processing, which is widely used in cement, metallurgy, chemical industry, etc. 1100 Degree Indirect External Heating Rotary Kiln For Processing Active Carbon Carbonate Catalyst Mineral Powder Caclining refers to various parts and components which are necessary for maintaining and repairing the normal operation of the rotary kiln, such as cylinder, baffle wheel, pallet, sealing device and so on.
Features and advantages of 1100 Degree Indirect External Heating Rotary Kiln For Processing Active Carbon Carbonate Catalyst Mineral Powder Caclining
High-temperature resistance: Due to the extremely high temperature of the working environment of the rotary kiln, the spare parts are usually made of refractory materials or special alloys to ensure that they can work stably under high temperatures.
High abrasion resistance: Long time material friction and chemical erosion require spare parts to have excellent abrasion resistance to prolong service life.
High structural strength: in order to withstand heavy loads and the pressure of continuous operation, the design of spare parts will place special emphasis on structural strength and reliability.
Easy to install and maintain: Considering the need for frequent replacement, many spare parts are designed to be simpler and easier for quick installation and maintenance.
Strong adaptability: different industries have different needs for rotary kilns, so spare parts need to have good versatility and adaptability to meet diverse application conditions.
(1100 Degree Indirect External Heating Rotary Kiln For Processing Active Carbon Carbonate Catalyst Mineral Powder Caclining)
Specifications of 1100 Degree Indirect External Heating Rotary Kiln For Processing Active Carbon Carbonate Catalyst Mineral Powder Caclining
This 1100-degree indirect external heating rotary kiln processes active carbon, carbonate catalysts, mineral powders, and similar materials. The kiln reaches temperatures up to 1100°C. The external heating method ensures heat transfers evenly to materials inside. This setup prevents direct contact between heat sources and processed substances. It reduces contamination risks. The design suits heat-sensitive applications.
The rotating drum structure improves material mixing. It promotes consistent thermal treatment. The kiln handles materials like active carbon. It processes carbonate catalysts for industrial use. Mineral powder calcining operates efficiently in this system. The indirect heating method uses gas or electric sources. Users adjust temperature profiles based on material requirements.
The kiln’s shell uses high-grade heat-resistant steel. Internal refractory layers withstand prolonged high-temperature exposure. Thermal insulation minimizes energy loss. The system maintains stable temperatures. It reduces energy consumption. A sealed design prevents gas leaks. It meets environmental standards.
Processing capacity varies with material type and particle size. Adjustable rotation speeds control residence time. This ensures optimal calcining results. The external heating chamber allows precise temperature management. It avoids overheating. Uniform heat distribution prevents material clumping.
Safety features include pressure relief valves and temperature sensors. Automatic shutdown triggers during abnormalities. The system supports continuous or batch operations. It fits small-scale labs and industrial production. Maintenance focuses on inspecting heating elements and seals. Routine checks ensure long-term reliability.
Customization options include drum dimensions, heating configurations, and control systems. Users integrate the kiln into existing production lines. Compatibility with automation software enables remote monitoring. The kiln suits research institutions and manufacturing plants.
Durable construction ensures years of service. The design prioritizes user safety and operational efficiency. It meets global standards for industrial heating equipment.
(1100 Degree Indirect External Heating Rotary Kiln For Processing Active Carbon Carbonate Catalyst Mineral Powder Caclining)
Applications of 1100 Degree Indirect External Heating Rotary Kiln For Processing Active Carbon Carbonate Catalyst Mineral Powder Caclining
The 1100-degree indirect external heating rotary kiln serves multiple industrial applications. It processes active carbon efficiently. High temperatures remove volatile substances from raw carbon materials. This activation increases surface area and adsorption capacity. The result is high-quality active carbon for water purification, air filtration, and chemical industries. Indirect heating prevents direct contact between materials and flames. This ensures consistent product quality.
The kiln handles carbonate catalyst preparation. It heats carbonate compounds to break them into oxides and carbon dioxide. Controlled temperature settings prevent overheating. This preserves catalyst structure and activity. Catalysts produced this way support chemical reactions in petroleum refining and synthetic fuel production. Uniform heat distribution inside the kiln guarantees stable catalyst performance.
Mineral powder calcining benefits from this equipment. Minerals like limestone or dolomite undergo thermal decomposition. The kiln’s external heating system allows precise temperature management. This avoids contamination from combustion gases. Processed mineral powders find use in construction, ceramics, and metallurgy. The rotary design ensures even exposure to heat. Material properties improve without risk of uneven processing.
Active carbon regeneration is another key use. Spent carbon loses adsorption capacity over time. The kiln reactivates it by burning off adsorbed impurities. Operating at 1100 degrees restores porosity and effectiveness. Reusing active carbon reduces waste and costs. Industries relying on filtration systems find this especially valuable.
The indirect heating method separates the heat source from processing materials. Combustion gases do not mix with products. This is critical for applications requiring high purity. Energy efficiency is optimized through heat recovery systems. Lower operational costs make the kiln a practical choice for large-scale production.
Durable construction handles continuous high-temperature operation. Advanced insulation minimizes heat loss. Automation allows real-time adjustments to temperature, rotation speed, and airflow. This ensures repeatable results across batches. Industries prioritize reliability and consistency. The rotary kiln meets these demands effectively.
Company Introduction
Established in 2001, plant Machinery Equipment Co.,ltd. focus on metal research and mining machinery spare parts. 2 factories over an area of 13,300 square meters, based on 100+ sets of equipment, our production capacity reaches 12000 Tons/Year. has passed ISO 9001 quality managment system certification in 2008.
Our mainly products are dragline excavator spare parts,rotary kiln spare parts, large modulus gear (gear shaft), gearbox ect. 40+ patents with over 45 years experience to help focus on improve the service life of spare parts. We belive that more than 80% reason of mechanical parts’ working life depends on hot processing (steel making/forging/casting/welding/heat treatment). Eight material engineers will control the quality from the original resource.
If you are interested, please feel free to contact us.
Payment
L/C, T/T, Western Union, Paypal, Credit Card etc.
Shipment
By sea, by air, by express, as customers request.
5 FAQs of 1100 Degree Indirect External Heating Rotary Kiln For Processing Active Carbon Carbonate Catalyst Mineral Powder Caclining
The 1100-degree indirect external heating rotary kiln processes active carbon, carbonate catalysts, mineral powders, and materials needing calcination. It uses high-temperature treatment to remove volatile components, activate surfaces, or change chemical structures. The indirect heating method keeps the material separate from combustion gases. This ensures product purity and avoids contamination.
What materials work with this kiln?
The kiln handles active carbon, carbonate catalysts, mineral powders like limestone or dolomite, and other heat-treated solids. It suits materials needing temperatures up to 1100°C. Organic substances, metal oxides, and minerals requiring controlled thermal reactions fit this system.
How does indirect external heating function?
Heating happens through an external source, like gas or electric heaters, warming the kiln’s outer shell. Heat transfers inward through the shell to the material inside. Combustion gases stay outside the processing chamber. This design prevents direct contact between materials and fumes. It improves product quality and reduces pollution.
Can temperature settings adjust for different materials?
Yes. The kiln includes precise temperature controls. Users set specific heating profiles based on material type and processing goals. Adjustments manage heating rates, hold times, and cooling phases. Uniform heat distribution ensures consistent results across batches.
What safety features protect the system?
The kiln has pressure relief valves, temperature sensors, and emergency cooling. Alarms trigger if temperatures exceed limits or pressure builds abnormally. Insulation layers prevent external overheating. Regular maintenance checks ensure parts like seals and bearings stay functional.
How often does maintenance occur?
Inspect seals, heating elements, and rotating parts weekly. Clean internal chambers monthly to remove residue. Replace worn components like thermocouples or refractory linings yearly. Follow the manufacturer’s schedule for lubrication and alignment checks. Proper upkeep prevents breakdowns and extends the kiln’s lifespan.
(1100 Degree Indirect External Heating Rotary Kiln For Processing Active Carbon Carbonate Catalyst Mineral Powder Caclining)
REQUEST A QUOTE
RELATED PRODUCTS
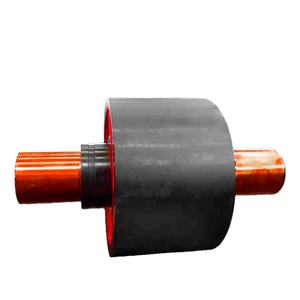
Hot ing Turning Spare Power Transmission Parts Custom Cast Iron Worm Gear Reducer Support Roller Rotary Kiln Shaft
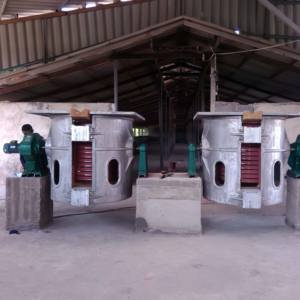
Customized Various Sizes Rotary Kiln Spare Parts Cement Ball Mill Drive Large Casting Gears
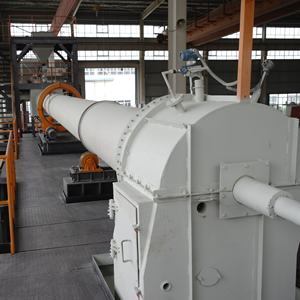
cement rotary kiln roller shaft with forging material
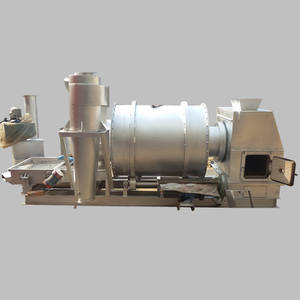
Professional rotary kiln spare parts steel plate/roller/refractory bricks rotary kiln
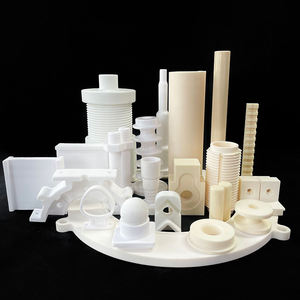
Rotary Kiln Spare Parts/Kiln Tyre/Shell
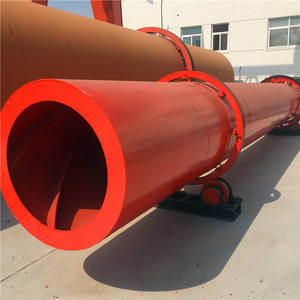