PRODUCT PARAMETERS
Description
Introduction of 600 Tons Per Day Rotary Kiln/Calcining Kiln for Oil, Gas, and Coal Burning
A rotary kiln is a kind of industrial equipment used for material heating and processing, which is widely used in cement, metallurgy, chemical industry, etc. 600 Tons Per Day Rotary Kiln/Calcining Kiln for Oil, Gas, and Coal Burning refers to various parts and components which are necessary for maintaining and repairing the normal operation of the rotary kiln, such as cylinder, baffle wheel, pallet, sealing device and so on.
Features and advantages of 600 Tons Per Day Rotary Kiln/Calcining Kiln for Oil, Gas, and Coal Burning
High-temperature resistance: Due to the extremely high temperature of the working environment of the rotary kiln, the spare parts are usually made of refractory materials or special alloys to ensure that they can work stably under high temperatures.
High abrasion resistance: Long time material friction and chemical erosion require spare parts to have excellent abrasion resistance to prolong service life.
High structural strength: in order to withstand heavy loads and the pressure of continuous operation, the design of spare parts will place special emphasis on structural strength and reliability.
Easy to install and maintain: Considering the need for frequent replacement, many spare parts are designed to be simpler and easier for quick installation and maintenance.
Strong adaptability: different industries have different needs for rotary kilns, so spare parts need to have good versatility and adaptability to meet diverse application conditions.
(600 Tons Per Day Rotary Kiln/Calcining Kiln for Oil, Gas, and Coal Burning)
Specifications of 600 Tons Per Day Rotary Kiln/Calcining Kiln for Oil, Gas, and Coal Burning
The 600 heaps per day rotating kiln/calcining kiln is a high-capacity industrial system created for calcination processes across industries such as concrete, lime, and mineral processing. It sustains oil, gas, and coal burning, providing versatility in gas selection to adapt to operational requirements and regional accessibility. The kiln includes a durable round steel covering lined with refractory materials to hold up against extreme temperature levels up to 1450 ° C, making sure longevity and thermal performance. Requirement dimensions include a length of 60– 90 meters and a size of 3.2– 4.5 meters, with a small disposition (2– 5%) and rotational speed of 0.5– 2.5 RPM to enhance product activity and house time for regular calcination. The kiln integrates multi-fuel burners compatible with fluid fuels, gas, or pulverized coal, coupled with sophisticated burning control systems to make best use of thermal effectiveness (commonly 75– 85%) and decrease fuel consumption. Discharges are taken care of through electrostatic precipitators, scrubbers, or bag filters to meet worldwide ecological requirements. Material handling is automated, including precision feeders for uniform feedstock distribution and a cooling system at the discharge end to stabilize product temperature. The drive system uses high-torque motors and gearboxes with variable rate control for smooth operation. Safety and security devices consist of pressure relief valves, temperature level sensing units, and emergency closure methods. A centralized PLC system allows real-time surveillance and change of parameters like temperature, turning rate, and air movement. Maintenance is streamlined via accessible examination ports and a resilient refractory cellular lining. The kiln complies with ISO, ASTM, and industry-specific certifications, guaranteeing reliability and conformity. Adjustable in dimension, gas arrangement, and automation degree, this rotary kiln provides high throughput, power performance, and low emissions, making it optimal for large industrial calcination needing accuracy and flexibility.
(600 Tons Per Day Rotary Kiln/Calcining Kiln for Oil, Gas, and Coal Burning)
Applications of 600 Tons Per Day Rotary Kiln/Calcining Kiln for Oil, Gas, and Coal Burning
The 600 lots daily rotating kiln, likewise called a calcining kiln, is a high-capacity thermal handling system made for industrial applications including oil, gas, and coal combustion. This functional devices facilitates the calcination of raw materials by exposing them to regulated heats (commonly 1200– 1500 ° C), allowing chemical or physical transformations important to multiple industries. Its durable building, gas flexibility, and advanced heat circulation systems make it ideal for large procedures needing precision and effectiveness.
In the ** oil industry **, this rotating kiln is widely made use of for calcining oil coke, a carbon-rich byproduct of oil refining. The process eliminates unpredictable parts and moisture, creating high-purity calcined coke important for making aluminum anodes and graphite electrodes. The kiln’s capability to operate on oil-based fuels guarantees seamless assimilation right into refinery operations while preserving power effectiveness.
For ** gas applications **, the kiln works as a sustainable option for handling minerals like sedimentary rock right into quicklime, a vital product in gas desulfurization. By using clean-burning gas, the kiln lessens emissions while providing regular thermal efficiency. It additionally sustains the production of stimulants and turned on carbon made use of in gas filtration and chemical synthesis.
In ** coal-driven procedures **, the kiln excels in calcining coal tar pitch and anthracite, boosting their carbon web content for use in steelmaking, carbon electrodes, and refractory products. Its coal-fired procedure is optimized for combustion performance, lowering waste and operational costs. Advanced exhaust control systems, consisting of scrubbers and real-time monitoring, make certain compliance with environmental laws.
The 600 TPD rotating kiln’s style prioritizes gas versatility, enabling operators to switch over between oil, gas, or coal based upon schedule and cost. Automated temperature and airflow controls ensure uniform product processing, while warm recuperation systems improve energy usage. Industries such as petrochemicals, metallurgy, and power rely on this kiln for its high throughput, sturdiness, and ability to fulfill strict environmental standards. By incorporating cutting-edge combustion technology with scalable efficiency, the rotary kiln stays a cornerstone of contemporary commercial calcination, driving performance and sustainability in resource-intensive markets.
Company Introduction
Established in 2001, plant Machinery Equipment Co.,ltd. focus on metal research and mining machinery spare parts. 2 factories over an area of 13,300 square meters, based on 100+ sets of equipment, our production capacity reaches 12000 Tons/Year. has passed ISO 9001 quality managment system certification in 2008.
Our mainly products are dragline excavator spare parts,rotary kiln spare parts, large modulus gear (gear shaft), gearbox ect. 40+ patents with over 45 years experience to help focus on improve the service life of spare parts. We belive that more than 80% reason of mechanical parts’ working life depends on hot processing (steel making/forging/casting/welding/heat treatment). Eight material engineers will control the quality from the original resource.
If you are interested, please feel free to contact us.
Payment
L/C, T/T, Western Union, Paypal, Credit Card etc.
Shipment
By sea, by air, by express, as customers request.
5 FAQs of 600 Tons Per Day Rotary Kiln/Calcining Kiln for Oil, Gas, and Coal Burning
The 600 Tons Per Day Rotary Kiln/Calcining Kiln is designed for high-temperature processing of materials like limestone, dolomite, petroleum coke, and industrial minerals using oil, gas, or coal as fuel. It supports flexible fuel options, enabling adaptation to regional availability or cost preferences without compromising thermal stability or output quality.
Thermal efficiency is optimized through advanced insulation, heat recovery systems, and preheating zones that reuse exhaust heat. This reduces energy consumption by up to 20% compared to conventional kilns, lowering operational costs and environmental impact while maintaining temperatures up to 1,500°C for consistent calcination.
Emission control integrates multi-stage systems, including electrostatic precipitators, bag filters, and scrubbers, to capture particulate matter, SOx, and NOx. Optional selective catalytic reduction (SCR) further reduces NOx emissions. The kiln complies with global standards like EPA and EU directives, ensuring eco-friendly operation.
Maintenance is streamlined via durable refractory linings with extended lifespans, easy-access inspection ports, and real-time monitoring sensors. Predictive maintenance alerts for wear-prone components like rollers and bearings minimize downtime, while automated controls reduce manual interventions.
Customization options include adjustable kiln dimensions, burner configurations, and control systems tailored to specific materials or production goals. Add-ons like preheaters, coolers, or waste heat recovery modules enhance functionality. Process parameters such as rotation speed and temperature profiles can be fine-tuned for optimal output quality and throughput.
(600 Tons Per Day Rotary Kiln/Calcining Kiln for Oil, Gas, and Coal Burning)
REQUEST A QUOTE
RELATED PRODUCTS
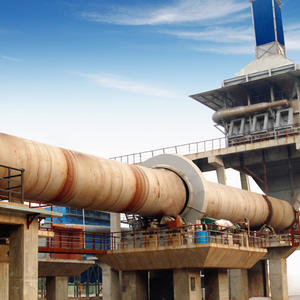
Rotary dryer spare parts Q235 mild steel welding kiln drum kiln shell
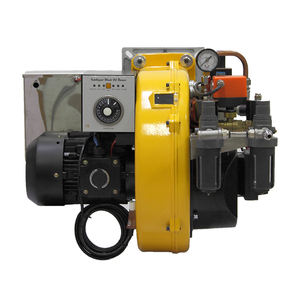
China Factory boiler air nozzle Boiler accessories Thermal power plant boiler air nozzle
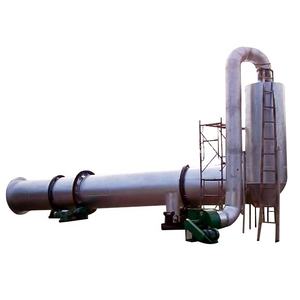
OEM Manufacture Casting Steel Rotary Kiln Spare Parts Ball Mill End Cover Casting Hollow Shaft
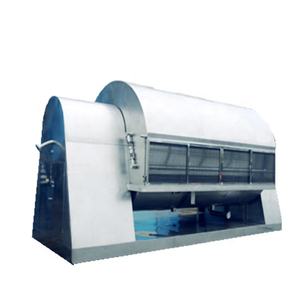
Rotary Kiln Spare Parts Steel 35 kiln tyre Large Casting Steel Kiln Riding Ring
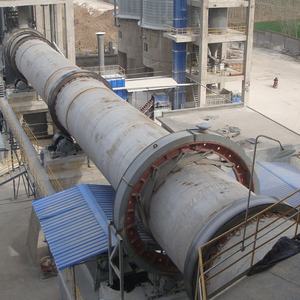
Citic Rotary kiln spare parts Rotary kiln forging supporting wheel
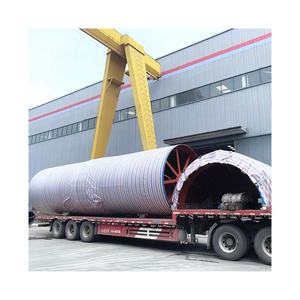