PRODUCT PARAMETERS
Description
Introduction of Design and manufacture environmental protection equipment rotary kiln incinerator equipment
A rotary kiln is a kind of industrial equipment used for material heating and processing, which is widely used in cement, metallurgy, chemical industry, etc. Design and manufacture environmental protection equipment rotary kiln incinerator equipment refers to various parts and components which are necessary for maintaining and repairing the normal operation of the rotary kiln, such as cylinder, baffle wheel, pallet, sealing device and so on.
Features and advantages of Design and manufacture environmental protection equipment rotary kiln incinerator equipment
High-temperature resistance: Due to the extremely high temperature of the working environment of the rotary kiln, the spare parts are usually made of refractory materials or special alloys to ensure that they can work stably under high temperatures.
High abrasion resistance: Long time material friction and chemical erosion require spare parts to have excellent abrasion resistance to prolong service life.
High structural strength: in order to withstand heavy loads and the pressure of continuous operation, the design of spare parts will place special emphasis on structural strength and reliability.
Easy to install and maintain: Considering the need for frequent replacement, many spare parts are designed to be simpler and easier for quick installation and maintenance.
Strong adaptability: different industries have different needs for rotary kilns, so spare parts need to have good versatility and adaptability to meet diverse application conditions.
(Design and manufacture environmental protection equipment rotary kiln incinerator equipment)
Specifications of Design and manufacture environmental protection equipment rotary kiln incinerator equipment
The rotating kiln incinerator is an advanced environmental management tools designed for secure and efficient disposal of hazardous, medical, commercial, and metropolitan solid waste. Engineered to satisfy strict ecological policies, this system incorporates robust layout, advanced burning technology, and exhaust control mechanisms to minimize ecological impact while ensuring optimum performance.
The rotary kiln is built from top-quality refractory materials and alloy steel, making sure sturdiness under severe temperatures varying from ** 800 ° C to 1,200 ° C ** in the main chamber. The round, slowly revolving kiln (normally ** 0.5– 2.5 RPM **) facilitates continuous waste agitation, promoting uniform combustion and complete burnout of natural and inorganic matter. An additional combustion chamber (SCC) runs at ** 1,100– 1,300 ° C **, guaranteeing detailed destruction of unpredictable compounds and dioxins. The system supports a ** residence time of 30– 90 minutes ** in the kiln, flexible based on waste make-up.
Integrated discharge control systems consist of relieve towers, dry or wet scrubbers, triggered carbon shot, and baghouse filters to neutralize acidic gases (SOx, HCl), capture particle issue, and adsorb heavy metals. Advanced models feature Discerning Non-Catalytic Decrease (SNCR) or Discerning Catalytic Decrease (SCR) systems to lower NOx discharges listed below ** 50 mg/Nm ³ **. Real-time monitoring using PLC and SCADA systems ensures exact control of temperature level, air flow, and feed prices, while gas analyzers (O ₂, CARBON MONOXIDE, NOx) warranty conformity with EU, EPA, or other international requirements.
The burner deals with ** 50– 5,000 kg/h ** of waste, with adjustable sizes for small-scale or commercial applications. Gas alternatives consist of natural gas, diesel, or waste-derived fuels, enhanced for energy performance. Complementary systems include automated waste feeding, ash removal, and warmth recovery units (e.g., waste heat central heating boilers) to convert thermal energy into vapor or electrical power, enhancing sustainability.
Produced under ISO 9001 and ISO 14001 criteria, the tools undertakes extensive screening for watertight performance, thermal stability, and architectural integrity. Safety and security functions consist of explosion-proof designs, emergency situation shutdown procedures, and pressure relief valves. Upkeep is streamlined using modular elements and easy-access inspection factors.
Perfect for contaminated materials plants, medical facilities, and industrial complicateds, this rotating kiln burner delivers dependable, environment-friendly waste administration, lowering land fill dependency and suppressing greenhouse gas emissions.
(Design and manufacture environmental protection equipment rotary kiln incinerator equipment)
Applications of Design and manufacture environmental protection equipment rotary kiln incinerator equipment
Rotating kiln burner devices stands for an essential advancement in environmental protection technology, created to deal with the growing challenges of waste monitoring and air pollution control. These systems are crafted for high-efficiency thermal therapy of diverse waste kinds, integrating robust style with sophisticated burning processes to lessen environmental influence. A rotating kiln burner runs by turning a cylindrical chamber, making certain uniform warmth circulation and optimum blending of waste products. This device enables full combustion, lowering damaging discharges and transforming waste right into inert ash, flue gas, and recoverable power.
Secret applications of rotary kiln burners cover several sectors. In contaminated materials management, they safely get rid of poisonous chemicals, pharmaceutical results, and industrial deposits, reducing the effects of pathogens and complex substances. Clinical facilities rely upon these systems to destroy contagious waste, consisting of sharps and biohazard products, preventing contamination. Districts make use of rotary kilns for large-scale strong waste handling, decreasing landfill dependency and creating power through waste-to-heat recuperation. Industrial sectors, such as petrochemical and manufacturing, deploy them to deal with sludge, oily wastes, and process results, making sure conformity with discharge policies. Furthermore, agricultural and electronic waste streams gain from their ability to handle pesticides, infected raw material, and non-recyclable e-waste components.
Layout advancements concentrate on toughness, with refractory linings and corrosion-resistant products to endure severe temperature levels and abrasive materials. Integrated emission control systems– such as scrubbers, bag filters, and discerning catalytic reduction systems– capture particulate issue, acidic gases, and dioxins, guaranteeing conformity with international standards like EPA and EU instructions. Automation improves functional safety and security and efficiency, with real-time tracking of temperature, oxygen degrees, and discharges.
Ecological advantages consist of considerable decreases in greenhouse gas discharges, garbage dump quantities, and soil/water contamination. Energy recuperation components convert combustion warm right into steam or power, sustaining round economic climate goals. By supplying scalable, functional services, rotary kiln burners play a critical function in lasting waste monitoring, aligning commercial development with ecological preservation. Their adoption highlights a dedication to regulatory adherence, public health security, and resource effectiveness in a quickly evolving ecological landscape.
Company Introduction
Established in 2001, plant Machinery Equipment Co.,ltd. focus on metal research and mining machinery spare parts. 2 factories over an area of 13,300 square meters, based on 100+ sets of equipment, our production capacity reaches 12000 Tons/Year. has passed ISO 9001 quality managment system certification in 2008.
Our mainly products are dragline excavator spare parts,rotary kiln spare parts, large modulus gear (gear shaft), gearbox ect. 40+ patents with over 45 years experience to help focus on improve the service life of spare parts. We belive that more than 80% reason of mechanical parts’ working life depends on hot processing (steel making/forging/casting/welding/heat treatment). Eight material engineers will control the quality from the original resource.
If you are interested, please feel free to contact us.
Payment
L/C, T/T, Western Union, Paypal, Credit Card etc.
Shipment
By sea, by air, by express, as customers request.
5 FAQs of Design and manufacture environmental protection equipment rotary kiln incinerator equipment
What is a rotary kiln incinerator? A rotary kiln incinerator is a thermal processing system designed to safely dispose of solid, liquid, and gaseous waste through high-temperature combustion. It consists of a rotating cylindrical chamber tilted to allow waste to move from the feed end to the discharge end. The kiln operates at temperatures between 800°C and 1,300°C, ensuring complete breakdown of hazardous materials, including organic compounds, medical waste, and industrial byproducts. Its design enables efficient mixing and prolonged exposure to heat, maximizing combustion efficiency.
Why choose a rotary kiln incinerator over other waste disposal methods? Rotary kilns offer superior versatility, handling diverse waste types in a single system. Their rotating design ensures uniform heat distribution, minimizing incomplete combustion and reducing harmful byproducts. Compared to static incinerators, they achieve higher thermal efficiency, lower emissions, and better residue management. They are ideal for complex waste streams, including sludge, chemicals, and contaminated solids, making them a preferred choice for large-scale, environmentally compliant operations.
Which industries use rotary kiln incinerators? Industries such as hazardous waste management, healthcare, pharmaceuticals, chemical manufacturing, and municipal waste treatment rely on rotary kiln incinerators. They are also used in cement production (co-processing waste) and sewage sludge disposal. Their ability to safely destroy toxic substances, pathogens, and volatile organic compounds aligns with strict environmental regulations, making them critical for sectors prioritizing eco-friendly waste solutions.
How do rotary kiln incinerators ensure environmental protection? Advanced emission control systems, including scrubbers, bag filters, and electrostatic precipitators, remove particulate matter, acidic gases, and dioxins. Continuous monitoring of flue gases ensures compliance with emission standards. High combustion temperatures eliminate organic pollutants, while automated controls optimize oxygen levels and residence time to minimize carbon monoxide and unburned residues. Some systems integrate waste heat recovery to reduce energy consumption, further enhancing sustainability.
What factors are critical in designing and manufacturing rotary kiln incinerators? Key considerations include kiln dimensions (length, diameter), refractory lining material to withstand extreme heat, rotational speed, and temperature zones tailored to waste types. Engineers prioritize residence time, turbulence for mixing, and integration of air pollution control devices (APCDs). Compliance with local and international regulations (e.g., EPA, EU directives) is mandatory. Durability, corrosion resistance, and automation for real-time adjustments are also vital to ensure operational efficiency and long-term reliability.
(Design and manufacture environmental protection equipment rotary kiln incinerator equipment)
REQUEST A QUOTE
RELATED PRODUCTS
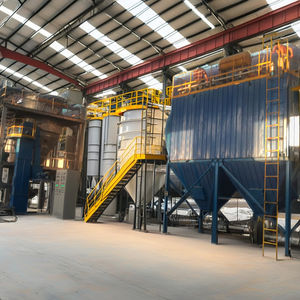
1100 Degree Indirect External Heating Rotary Kiln For Processing Active Carbon Carbonate Catalyst Mineral Powder Caclining
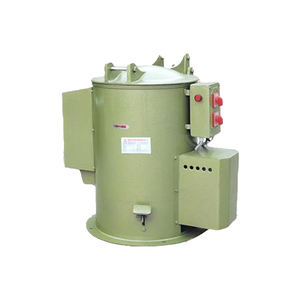
Refractory Cordierite Ceramic Heating parts Factory Direct
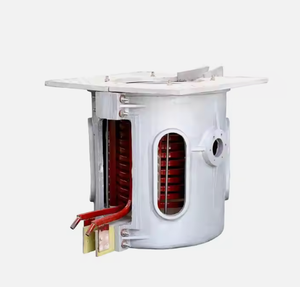
China factory identification of high quality hot ing unique kiln rotary calcining rotary kiln production line
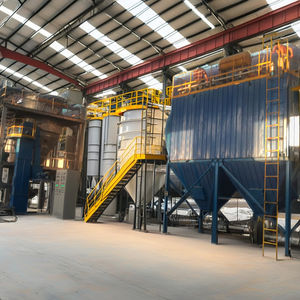
Factory Hongxing Mini 180TPD rotary kiln for calcining cement clinker lean iron ore nickel and aluminum plant with good
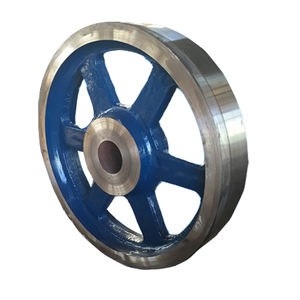
Metal Metallurgy Machinery Top ing For Producing Parts Advanced Machines High Quality Arc Metal Industrial Sintering Furnace
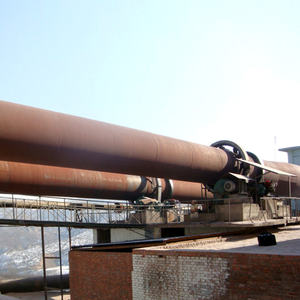