PRODUCT PARAMETERS
Description
Introduction of Support Roller For Kiln Small Rotary Kiln Used Rotary Kiln
A rotary kiln is a kind of industrial equipment used for material heating and processing, which is widely used in cement, metallurgy, chemical industry, etc. Support Roller For Kiln Small Rotary Kiln Used Rotary Kiln refers to various parts and components which are necessary for maintaining and repairing the normal operation of the rotary kiln, such as cylinder, baffle wheel, pallet, sealing device and so on.
Features and advantages of Support Roller For Kiln Small Rotary Kiln Used Rotary Kiln
High-temperature resistance: Due to the extremely high temperature of the working environment of the rotary kiln, the spare parts are usually made of refractory materials or special alloys to ensure that they can work stably under high temperatures.
High abrasion resistance: Long time material friction and chemical erosion require spare parts to have excellent abrasion resistance to prolong service life.
High structural strength: in order to withstand heavy loads and the pressure of continuous operation, the design of spare parts will place special emphasis on structural strength and reliability.
Easy to install and maintain: Considering the need for frequent replacement, many spare parts are designed to be simpler and easier for quick installation and maintenance.
Strong adaptability: different industries have different needs for rotary kilns, so spare parts need to have good versatility and adaptability to meet diverse application conditions.
(Support Roller For Kiln Small Rotary Kiln Used Rotary Kiln)
Specifications of Support Roller For Kiln Small Rotary Kiln Used Rotary Kiln
The Support Roller for Kiln is a vital component designed to ensure the steady and reliable procedure of small rotary kilns and made use of rotary kilns throughout sectors such as concrete, metallurgy, and chemical handling. These rollers bear the kiln’s weight, help with smooth turning, and lessen friction, ensuring lasting resilience under high thermal and mechanical tension. Secret requirements consist of product composition, measurements, load capacity, and thermal resistance. Built from high-grade alloy steel or created steel, assistance rollers undertake heat treatment processes like relieving and toughening up to improve solidity (normally HRC 45-55) and fatigue resistance. The surface area is frequently machined to a smooth coating (Ra ≤ 3.2 μm) to reduce endure the kiln’s riding rings. Standard sizes vary from 200 mm to 800 mm, with lengths varying based upon kiln size. Shaft diameters are crafted to line up with kiln tons needs, typically between 100 mm and 400 mm. Dynamic lots capacity usually extends 50– 300 metric heaps, accommodating both static and rotational anxieties. Running temperature levels endure up to 400 ° C, with optional heat-resistant finishings or materials for severe atmospheres. Spherical roller bearings or secured bearing systems are integrated to handle misalignment and heavy radial loads. Lubrication systems may include automatic grease dispensers or hands-on ports, making sure very little downtime. For used rotary kilns, assistance rollers are commonly reconditioned through machining, surface area solidifying, or bearing replacement to recover performance. Personalization options include tailored measurements, material qualities (e.g., ZG40CrMo), and birthing arrangements to match details kiln models. Installation calls for exact placement (tolerance within ± 1 mm) to avoid unequal wear. These rollers work with kiln diameters of 1.5– 4 meters and lengths of 15– 50 meters, typical in small-scale operations. Maintenance includes normal examination for fractures, wear, and lubrication performance. Security functions consist of robust layout to stand up to thermal expansion and shock lots. Ideal for applications in limestone calcination, waste incineration, or ore processing, these rollers guarantee functional connection, lowered energy usage, and extended kiln lifespan. Service warranty periods typically range from 12– 24 months, depending on usage problems.
(Support Roller For Kiln Small Rotary Kiln Used Rotary Kiln)
Applications of Support Roller For Kiln Small Rotary Kiln Used Rotary Kiln
Support rollers are critical components in the procedure of rotary kilns, including little and previously owned versions, guaranteeing stability, positioning, and smooth rotation of the kiln covering. These rollers bear the whole weight of the kiln while maintaining regular call with the riding rings, enabling reliable warm handling of products like concrete, lime, minerals, and waste. For little rotary kilns, support rollers are created to manage compact configurations without endangering tons capability. Their precision engineering minimizes friction and wear, even in high-temperature atmospheres, guaranteeing durability and minimizing upkeep prices. Tiny kilns frequently require tailored roller solutions to match specific dimensions and functional speeds, making versatile support systems crucial for optimum efficiency. In operation rotating kilns, support rollers play an essential duty in refurbishment and retrofitting projects. Older kilns might experience misalignment or roller deterioration in time, leading to unequal turning and power inadequacy. Changing or upgrading support rollers brings back equilibrium, reduces vibration, and prolongs the kiln’s functional life. Top notch rollers for made use of kilns are often constructed with advanced alloys to withstand thermal tension and mechanical pressure, guaranteeing integrity popular commercial setups. Key features of assistance rollers include robust construction, heat-resistant materials, and accuracy machining to keep limited resistances. They are engineered to distribute tons equally, avoiding deformation of the kiln shell and decreasing the risk of downtime. Lubrication systems incorporated into roller assemblies additionally boost performance by lessening friction and warm build-up. Applications cover sectors such as cement production, metallurgy, chemical handling, and ecological waste management. In cement plants, assistance rollers allow consistent clinker development, while in waste incineration kilns, they ensure stable turning for comprehensive material malfunction. Their versatility likewise includes mineral processing, where specific temperature level control and rotational stability are essential. For services purchasing used or tiny rotating kilns, choosing sturdy, well-designed support rollers is crucial for optimizing efficiency and lessening operational disturbances. Routine examination and upkeep of these components assist find very early indicators of wear, guaranteeing smooth kiln procedure and guarding long-term ROI.
Company Introduction
Established in 2001, plant Machinery Equipment Co.,ltd. focus on metal research and mining machinery spare parts. 2 factories over an area of 13,300 square meters, based on 100+ sets of equipment, our production capacity reaches 12000 Tons/Year. has passed ISO 9001 quality managment system certification in 2008.
Our mainly products are dragline excavator spare parts,rotary kiln spare parts, large modulus gear (gear shaft), gearbox ect. 40+ patents with over 45 years experience to help focus on improve the service life of spare parts. We belive that more than 80% reason of mechanical parts’ working life depends on hot processing (steel making/forging/casting/welding/heat treatment). Eight material engineers will control the quality from the original resource.
If you are interested, please feel free to contact us.
Payment
L/C, T/T, Western Union, Paypal, Credit Card etc.
Shipment
By sea, by air, by express, as customers request.
5 FAQs of Support Roller For Kiln Small Rotary Kiln Used Rotary Kiln
**What is a support roller in a rotary kiln?**
A support roller is a critical component that bears the kiln’s weight and ensures smooth rotation. It consists of a shaft, bearings, and wheels, designed to align with the kiln’s tires (riding rings). Properly functioning rollers distribute heat and load evenly, preventing mechanical stress and extending the kiln’s lifespan.
**How do I maintain support rollers?**
Regular lubrication of bearings, alignment checks, and monitoring wear patterns are essential. Inspect rollers for cracks, pitting, or uneven surfaces. Track operating temperatures—excessive heat indicates friction or misalignment. Clean debris and ensure seals protect against dust. Proactive maintenance minimizes unplanned downtime and optimizes performance.
**How often should support rollers be inspected?**
Inspect support rollers every 3–6 months, depending on usage intensity. High-temperature kilns or heavy-load operations may require monthly checks. Include alignment measurements, wear assessments, and lubrication quality in inspections. For used kilns, increase frequency due to potential prior wear.
**Can support rollers from a used rotary kiln be reused?**
Yes, if inspection confirms no cracks, minimal wear, and smooth rotation. Test bearing integrity and check for corrosion or distortion. However, replacing worn rollers during kiln refurbishment is often safer to avoid operational risks. Consult a technician to evaluate compatibility with your kiln’s specifications.
**What indicates a support roller needs replacement?**
Visible cracks, flat spots, excessive vibration, or irregular noise signal replacement. Overheating bearings or misalignment despite adjustments also indicate wear. Delaying replacement risks kiln shell damage or motor failure. Opt for high-grade steel rollers with heat-resistant properties, precision-machined to match your kiln’s load and size for optimal durability.
(Support Roller For Kiln Small Rotary Kiln Used Rotary Kiln)
REQUEST A QUOTE
RELATED PRODUCTS
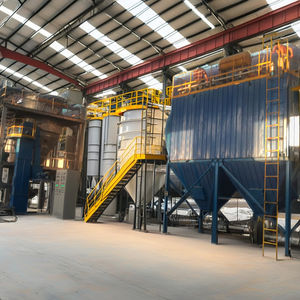
Cement Rotary Kiln Seal Rotary Kiln Barrel Parts
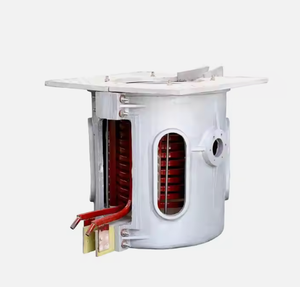
High quality Cement plant rotary kiln replacement parts large module ring gear
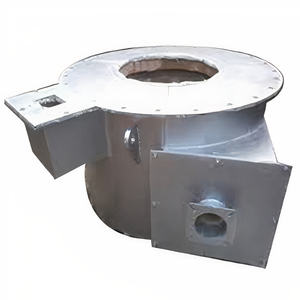
Jiangsu Pengfei Group Rotary kiln spare parts girth gear and tyre
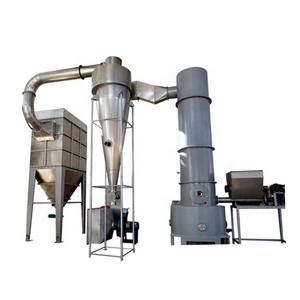
Wide Adaptability High Strength Double Swirl Rotary Kiln Burner Low Cost Double Swirl Rotary Kiln Burner
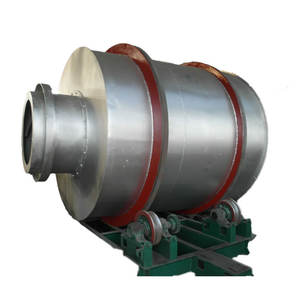
Citic Rotary kiln spare parts Rotary kiln supporting wheel bearing device Rotary kiln
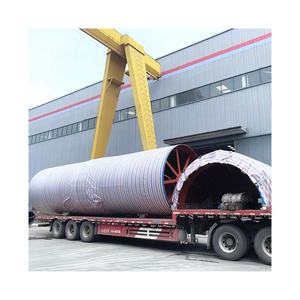